Снятие фаски – один из видов металлообработки для решения нескольких задач: доведения геометрии заготовки до требуемых параметров, придания эстетичности, снижения рисков травмирования при эксплуатации изделия, а также получения нужных характеристик, продиктованных особенностями механизма или конструкции, в которой деталь будет использоваться. В этой статье расскажем, как снимать фаски, какие способы для этого используются. Рассмотрим назначение данной конструктивной части.
Зачем нужна фаска?
Фаска является переходной поверхностью, располагающейся между двумя гранями. Она представляет собой находящуюся под определённым углом зону, созданную путём скоса по краю торцевой части изделия. Эта область может быть прямой или, например, закруглённой.
Фаски снимаются с различных деталей – с плоских достаточной толщины (планок, тонких брусков, листов), а также с полых или цельных тел вращения: фланцев, валов, труб, ступиц. Этот вид обработки применим к разным материалам, но чаще всего используется при изготовлении продукции из металлов.
Фаска – часто используемый конструктивный элемент изделий из разных сфер. Она снимается для улучшения прочностных свойств и эксплуатационных характеристик, для придания нужной эргономики, в декоративных или технологических целях.
Фаски играют важную роль в конструкторских или архитектурных процессах, технологических операциях, сборке конструкций, строительстве – везде, где необходимо достичь заданной степени эстетики, функциональности, точности конфигурации, безопасности, работоспособности.
Операция снятия фаски – один из этапов металлообработки: промежуточный или финишный. Обычно этот процесс обеспечивает подготовку прокатной, штампованной, литой или другой продукции к дальнейшим работам: сварочным, сборочным, отделочным. Фаски снимаются не только для улучшения эстетических и функциональных качеств, но и для проведения определённых технологических операций: соединения, стыковки деталей в узлах, механизмах, многокомпонентных конструкциях.
Виды фасок
Виды различаются по способам срезания кромок. Это такие методы:
- Y-образный. Часто используется на производствах, особенно при предварительной обработке металлоизделий перед сварочными работами. Такое название присвоено, потому что при стыковке двух кромок со снятыми фасками формируется соединение, напоминающее соответствующую букву латинского алфавита.
- X-образный. Этот метод также распространён. Соединение двух изделий их кромками образует букву «X».
- V-образный. При соединении двух кромок образуется подобие буквы «V».
- J-образный. Полученные этим способом фаски называют рюмочными, так как по форме срез похож на данную букву, а при стыковке двух кромок прослеживается символ U (поэтому другое название метода – U-образный). Применяют специализированные автоматизированные устройства – фаскосниматели. Методика позволяет создавать увеличенные по объёму сварочные ванны.
- Другие, например, K-образный. По таким технологиям создаются фаски криволинейных конфигураций, которые позволяют формировать сварочные швы с высокой точностью. Это необходимо, если свариваемые детали сложные по конструкции.
По форме поверхности варианты делятся на прямые, полукруглые, фигурные, угловые. Первые – наиболее простые и распространённые. Срез осуществляется прямо, рабочий инструмент при обработке обычно движется прямолинейно или возвратно-поступательно. Полукруглые фаски отличаются закруглением: либо выпуклым, либо вогнутым (радиусным), углубляющимся в материал. Угловая конфигурация – это скошенный край, сформированный под отличным от 45 градусов углом. Фигурные варианты имеют сложные формы, например, витые, создаваемые сверлением спиралевидных ямок, ступенчатые с переходами, комбинированные с сочетанием нескольких методов.
По назначению фаски бывают:
- Переходными. Создаются, чтобы сглаживать зоны переходов между углами, радиусами.
- Декоративными. Бывают прямыми или фигурными, подходят для придания изделиям большей привлекательности, применяются при изготовлении элементов архитектуры, ландшафтного или интерьерного дизайна.
- Служебными. Улучшают функциональные характеристики изделий, повышают герметичность и надёжность соединений, позволяют добиваться лучшей стыковки элементов механизмов или конструкций. Этот вид применяется для обработки кабельных отводов, выпускных и выпускных отверстий.
- Отделочными. Одна из них – микрофаска, которая требует высокой точности выполнения работ, снимается инструментом с очень тонким заострённым краем для повышения конечного качества, для удаления дефектов, таких как излишки материала, наплавы, заусенцы.
- Специальными, пример – контргрань. Её применяют для формирования на заготовке противоположной грани, которая корректирует конфигурацию и габариты, а также повышает устойчивость, улучшает зрительное, тактильное восприятие.
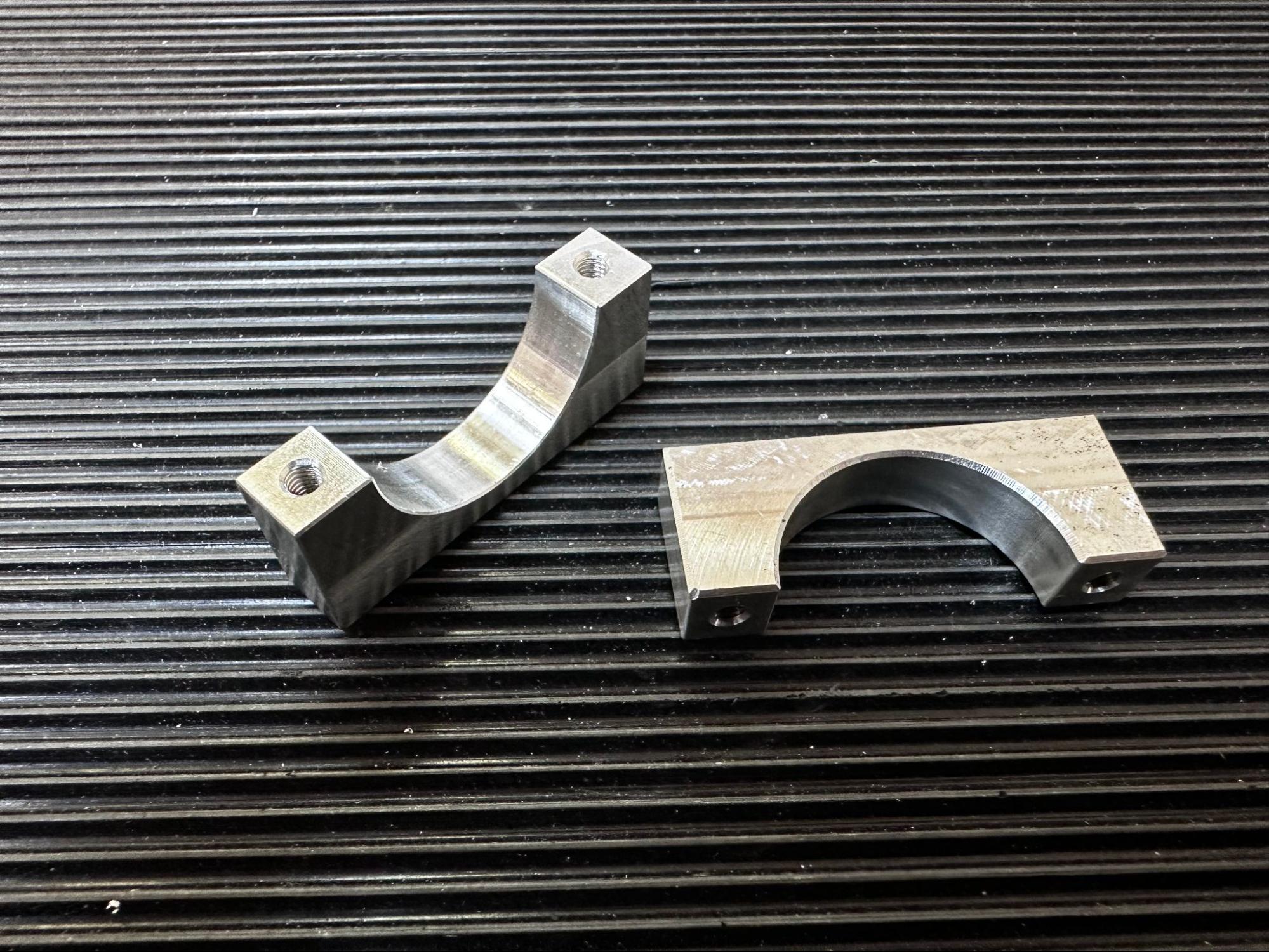
Основные способы снятия фаски на металле
Фаски снимаются разными способами, которые позволяют удалять краевую часть механическим, химическим или термическим воздействием. Рассмотрим все методы ниже.
Ручное
Примитивный, непроизводительный, трудоёмкий, отличающийся невысокой точностью способ. Он предполагает обработку краёв вручную с применением простых инструментов, таких как наждак, стамеска, ручная фреза. Чтобы убирать края металлических изделий своими руками, необходимы соответствующие навыки, а также большой опыт. Если всё это есть, можно добиться достойного качества.
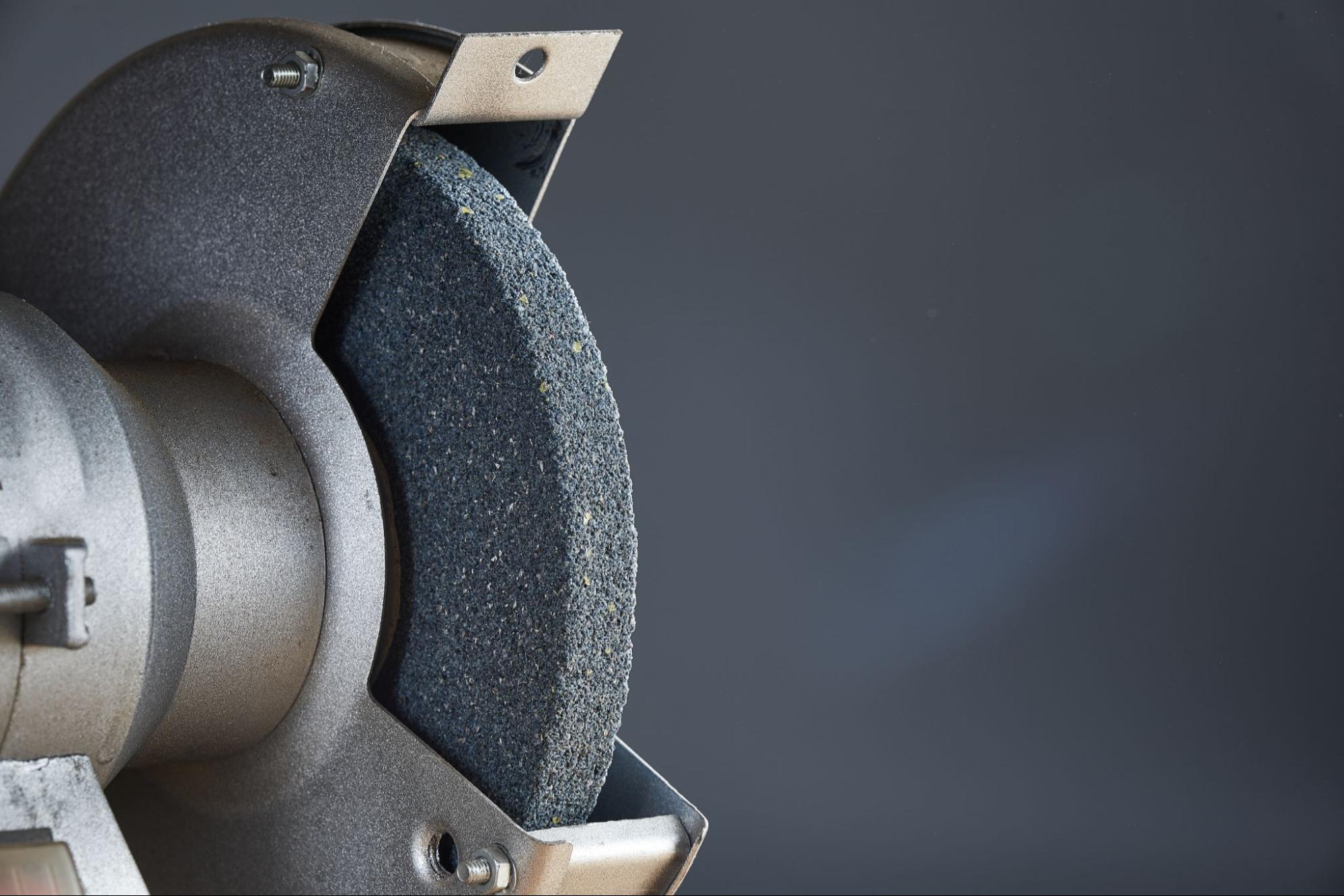
Механическое
Требует использования механизированных инструментов с разной степенью автоматизации. Это станки (фрезерные, фаскозачистные, токарные, универсальные), шлифовальные машины, а также специализированные приборы – кромкорезы, фаскосниматели, кромкоскалыватели.
Механическая обработка оборудованием более точная, быстрая, эффективная, качественная и производительная, чем ручная. Она помогает экономить время и трудовые ресурсы, достигать максимальной надёжности и герметичности швов, разъёмных резьбовых соединений, а также сохранять структуру, строение и физико-химические свойства металлов.
Суть механообработки обычно заключается в применении режущих инструментов, которые либо вращаются и подаются на зафиксированные в статичном положении заготовки, либо движутся возвратно-поступательно и снимают слой материала с крутящихся изделий.
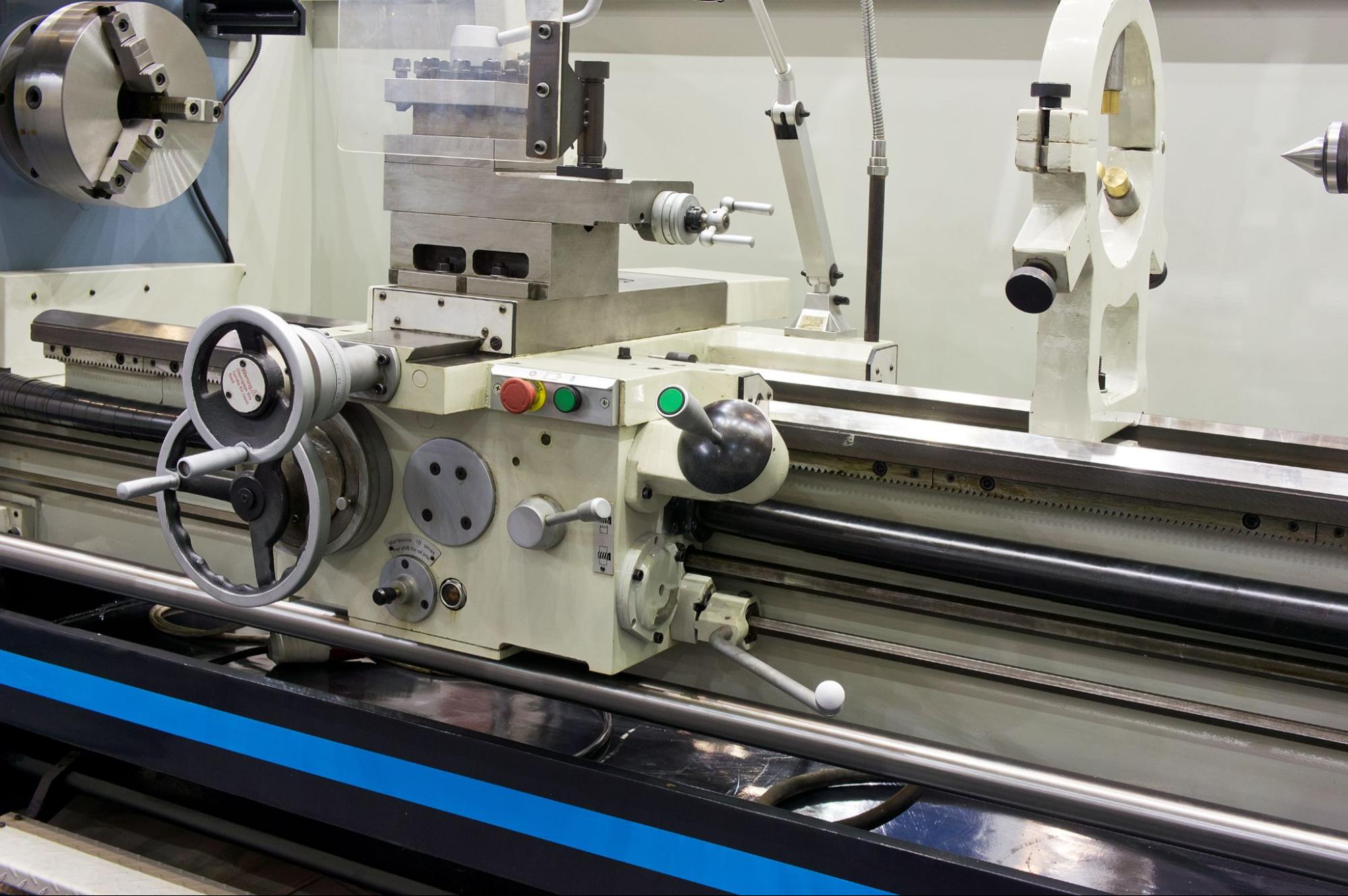
Химическое
Такие методы используют нечасто, только для металлов, подвергающихся воздействию особых химических составов. Последние разрушают, удаляют поверхностные слои материала за счёт агрессивного воздействия на него. Но такие методы требуют строгого соблюдения мер безопасности, повышенной аккуратности, а также точного дозирования химикатов и их локального, направленного, контролируемого применения в зоне снятия.
Лазерное
Этот способ эффективен, позволяет получать ровные поверхности с минимальными повреждениями окружающих зон металла. Луч лазера действует локально, но за счёт своей тепловой энергии провоцирует частичное расплавление материала, что повышает его расход, требует учёта припусков.
Лазерное оборудование требует навыков обращения с ним. Нарезать таким способом можно только прямые фаски. С ломаными, криволинейными работать невозможно из-за особенностей подачи луча. Устройства дорогие, что повышает стоимость обработки. Операции сопровождаются выделением испарений и газов, поэтому помещение должно хорошо вентилироваться.
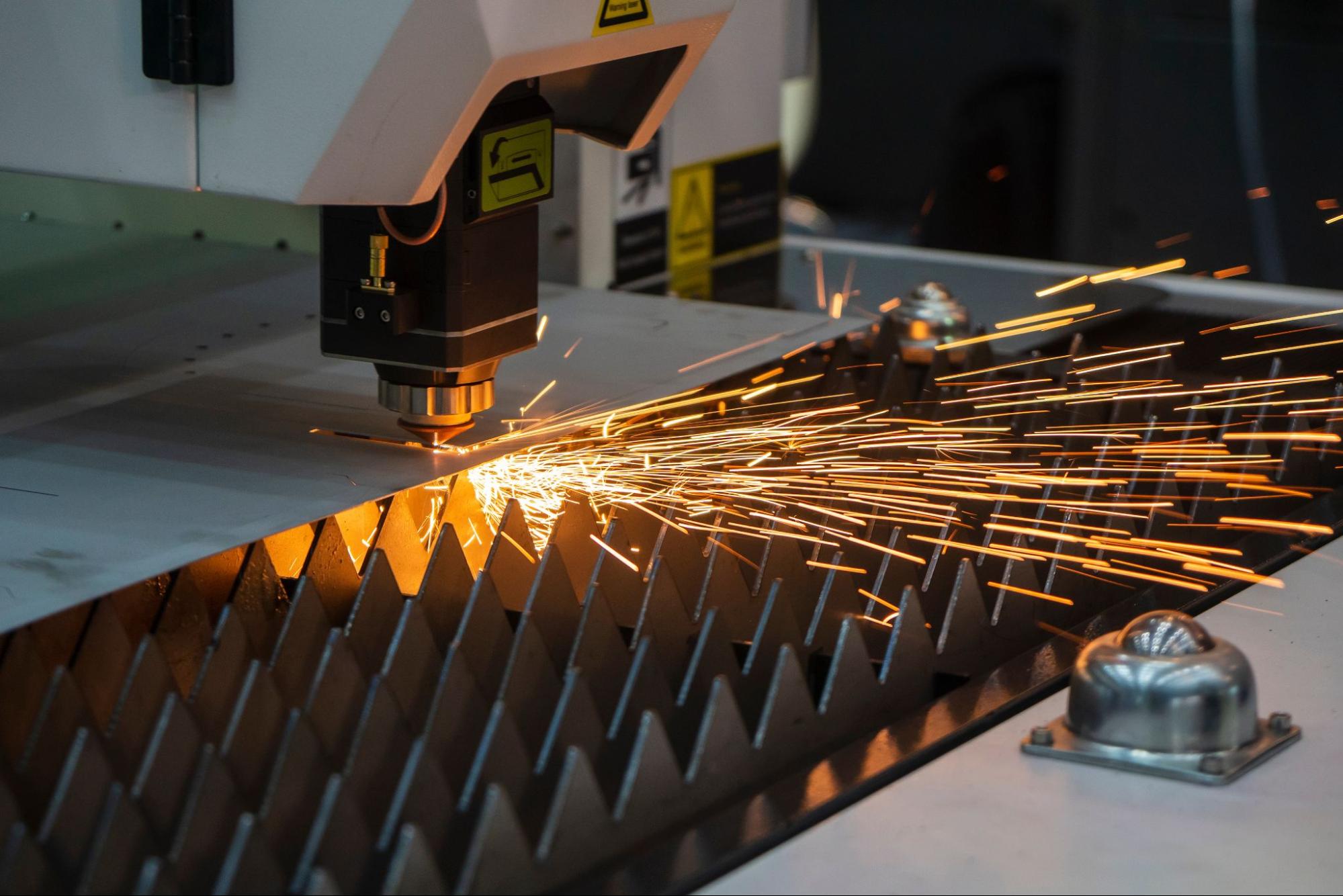
Газовое
Такой метод недорогой, производительный, подходит для обработки толстых металлов – от 30 миллиметров до 100-150. Газовое оборудование бывает как стационарным, используемым только в оборудованных помещениях, так и портативным, мобильным. Это делает возможным применение технологии в разных зонах, в том числе в полевых условиях.
Если провести две последовательные нарезки, то на плоском листе можно получить за один проход непрямую фаску, например, X-образную. Если нужно обработать трубу или цилиндрическую заготовку, то выбирают автоматизированное газовое оборудование с цифровым управлением, с оснасткой в виде независимых двух поворотных головок.
Среди минусов методики невозможность снятия фасок сложных форм, невысокая точность реза, выделение вредных летучих веществ (необходима мощная вентиляция), обусловленные термическим воздействием изменения в области реза, а также появление наплывов, бугров или других дефектов.
Плазменное
Такой способ уступает лазерному в конечной гладкости поверхности и в точности реза. С его помощью нельзя снимать фаски ломаной конфигурации. Стоимость работ средняя, меньше цены металлообработки лазером. Возможно разрезание металлов толщиной до 100 мм. Производительность высока.
Поток плазмы расплавляет металл, что обусловливает возникновение дефектов в виде наплывов, неровностей. Неверный подбор режимов, неисправность оборудования или ошибки оператора чреваты появлением криволинейных контуров. Выделяются мелкие фрагменты окалины, вредные газы, а также небезопасное для органов зрения ультрафиолетовое излучение.
Для высокой точности поверхность должна быть гладкой, а заготовку нужно располагать под определённым углом.
Газоплазменное
Принцип – точечный нагрев обрабатываемой области с удалением поверхностных слоёв расплавляемого материала. Функцию источника энергии выполняет электрическая дуга, которая работает в комплексе с газами и повышает температуру до формирования струи плазмы.
Стоимость работ невысокая, производительность хорошая. Но по качеству рез получается хуже, чем при механообработке. Часто требуется финишное шлифование для достижения нужной гладкости или допустимой шероховатости. Газоплазменное воздействие вызывает появление области термовлияния: тут физико-химические свойства изменены, что негативно отражается на надёжности будущих сварных швов.
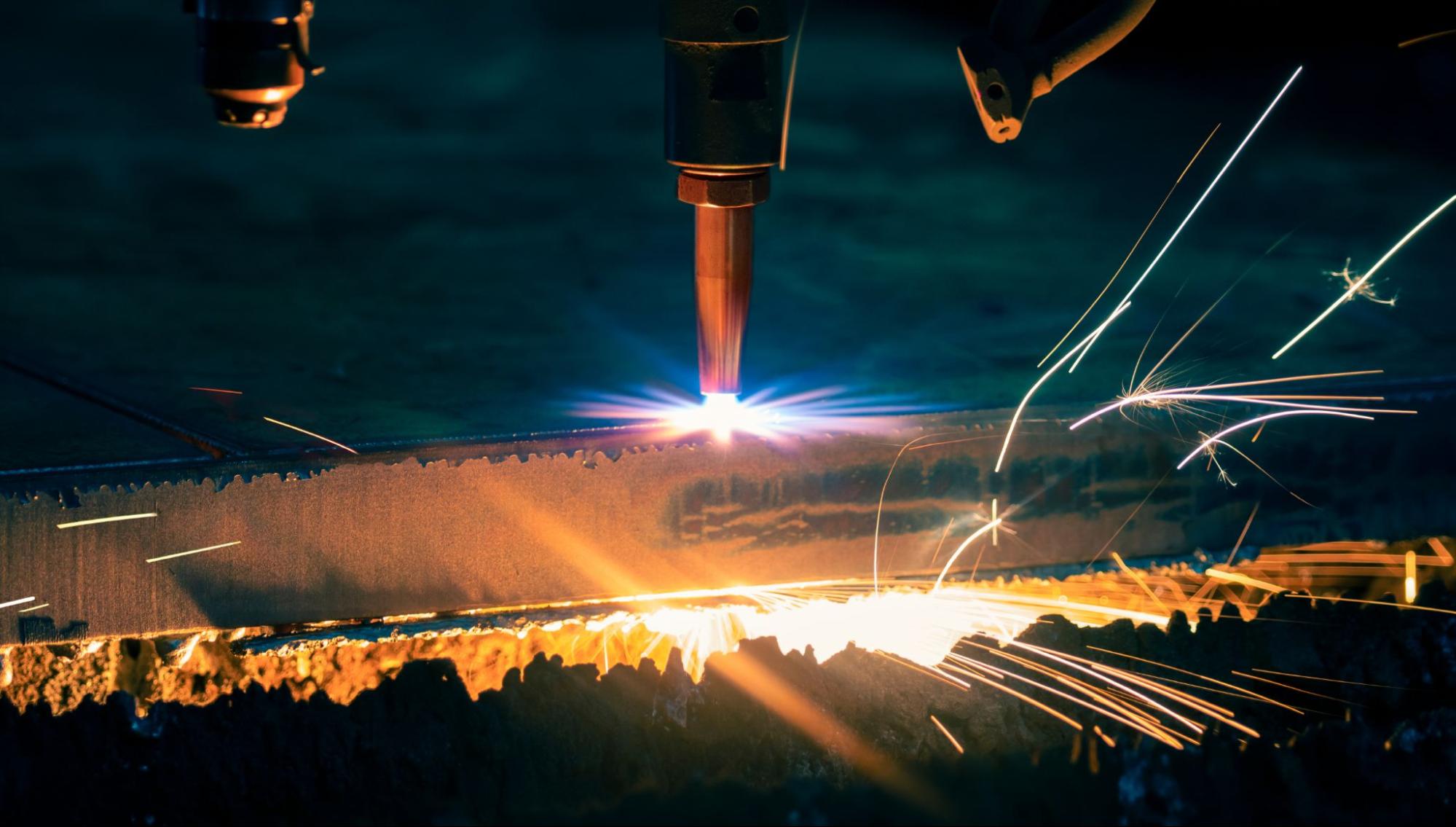
Инструменты для снятия фаски
Используются такие инструменты и автоматизированные агрегаты:
- продольно-строгальные станки – агрегаты, снимающие поверхностные слои за счёт возвратно-поступательных прямолинейных перемещений рабочего стола с закреплённым на нём изделием;
- кромкоскалыватели – агрегаты, которые скалывают кромки;
- фаскорезы, обрабатывающие краевые и кромочные участки не очень твёрдых металлов;
- фрезерные станки – металлорежущее оборудование, оснащаемое вращающимися фрезами, которые обрабатывают неподвижные заготовки;
- токарное оборудование – установки, обрабатывающие металлические или другие вращающиеся заготовки (валы, втулки, муфты) точением, резанием;
- кромкофрезеры – ручные или более массивные стационарные приборы с вращающимися фрезами, снимающими верхние слои материалов;
- шлифовальные машины с кругами из абразивных материалов;
- ручные фрезы – инструменты в виде стержня с единственным или несколькими режущими острыми лезвиями или зубьями, располагающимися по винтовой линии либо по всей поверхности рабочего элемента (заострённые кромки различаются по форме);
- ножи-фаскосниматели и торцеватели труб, снимающие кромки по краям трубных элементов;
- напильники – инструменты из твёрдых металлов с насечками на рабочей поверхности для обработки разных материалов
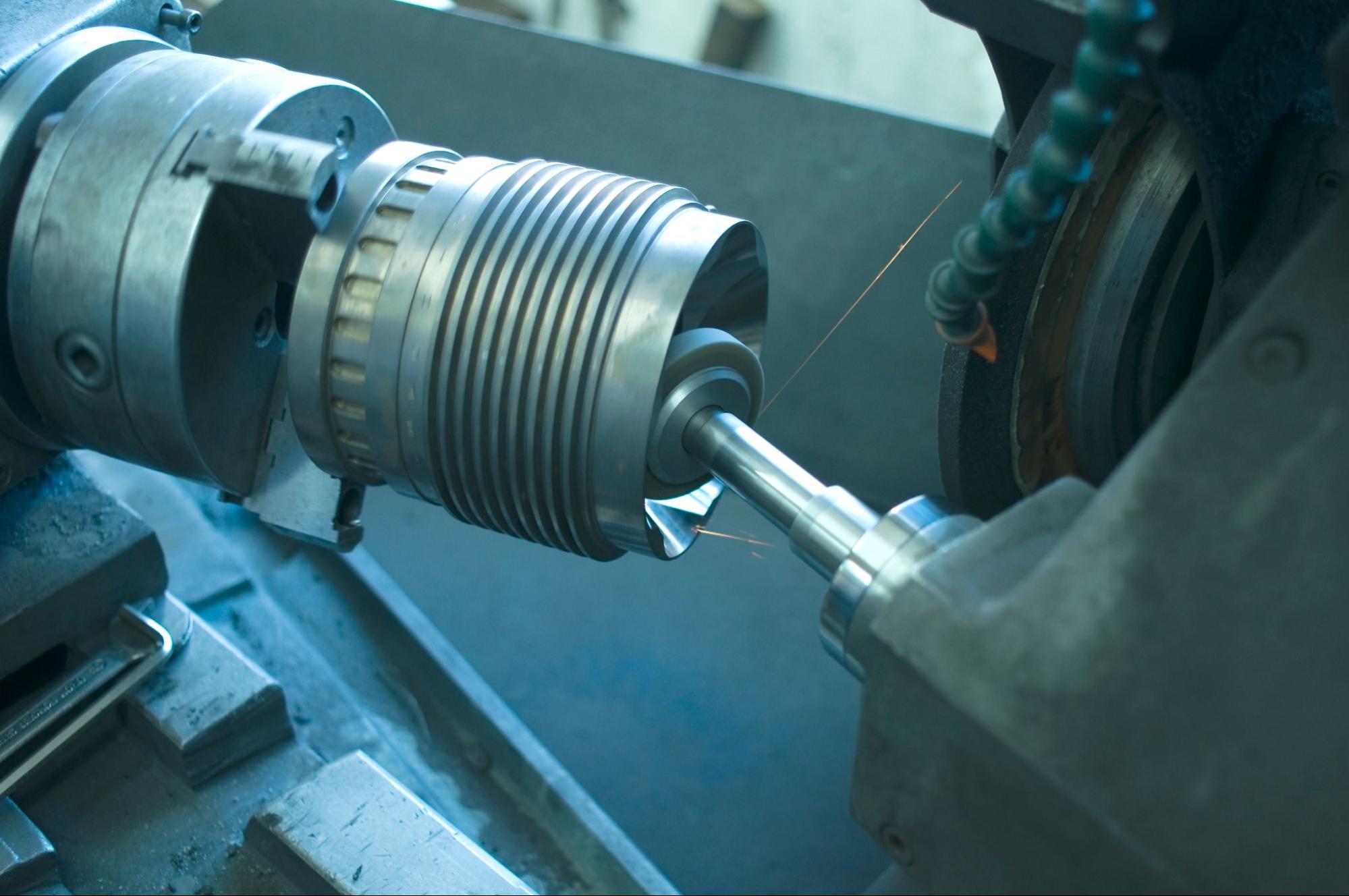
Угол снятия фаски
Под каким углом снимаются фаски? Его значение определяется с учётом вида и технологии предстоящей сварки или другого технологического процесса, толщины металла, конфигурации и размеров изделия, его назначения, конструктивных характеристик, действующих стандартов, чертежей, технических документов, требований производителей.
Угол – обычно от 30 градусов до 45. Стандартный показатель для листов – 45°. Значения для труб отличаются и могут составлять 30 градусов для стандартных трубных изделий или 37,5 градусов для толстостенных. Если стенки тонкие, угол может составлять 45°.
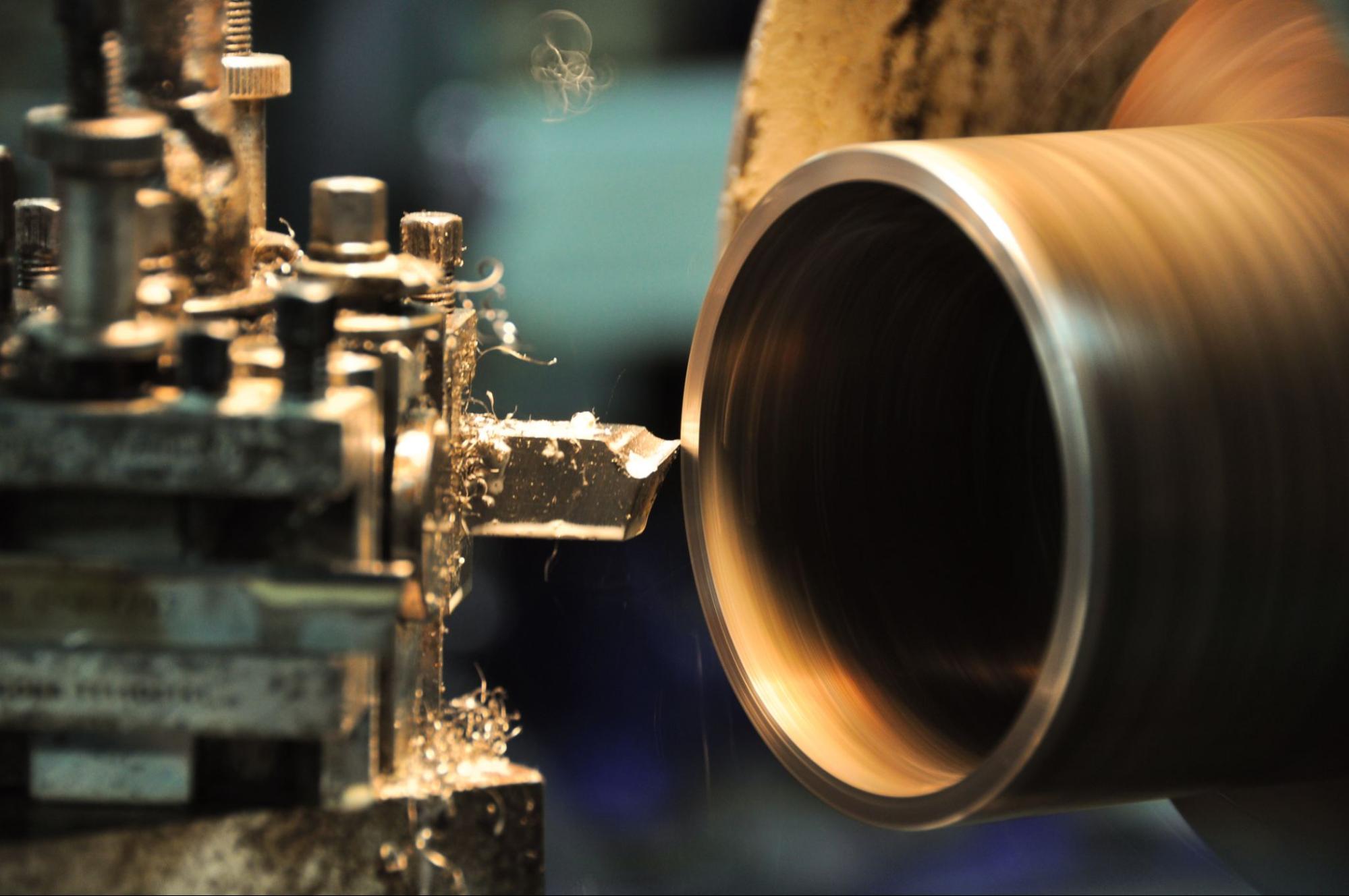
Особенности процесса
Процесс включает этапы:
- Выбор инструмента. Он осуществляется с учётом характеристик детали, типа и способа предстоящей эксплуатации или обработки (сварка, сборка конструкции, формирование соединения), необходимой формы фаски, толщины, обрабатываемого материала, свойств металла или сплава.
- Подготовка изделия. Оно должно быть очищенным, доведённым до нужного состояния. Иногда нужна предварительная обработка.
- Фиксация детали. Она крепится в рабочей зоне, например, на столе, в струбцине, на шпинделе, в патроне. При недостаточной фиксации может произойти смещение, что спровоцирует появление дефектов или даже получение травмы оператором.
- Настройка оборудования. Сегодня часто используют станки с числовым программным управлением (ЧПУ): их нужно точно настраивать, задавая скорость вращения инструмента и передвижения заготовки, подачу, траекторию движения, глубину осуществляемого резания. Ручной инструмент также надо наладить: установить насадку (круг, фрезу), зафиксировать её, выбрать оптимальный скоростной режим.
- Обработка. Инструмент должен проходить вдоль кромки плавно, с постоянной скоростью, со стабильным, небольшим давлением. Если используется станок с ЧПУ, то степень подачи, скорость вращения, угол расположения фрезы или другого элемента и другие параметры заносятся в программу, контролируются системой. Иначе рабочие показатели должен поддерживать и проверять оператор.
- Контроль качества. Деталь внимательно осматривается, проверяется на момент наличия дефектов. Если выявлены изъяны, они оперативно устраняются, например, сменой рабочей головки или корректировкой настроек, иногда ручной обработкой. Если изделие признаётся браком, оно утилизируется или перерабатывается на сырьё для последующего производства.
Если применяется портативный фаскосниматель, то его нужно надёжно зафиксировать на трубе (на внутренней стороне) или на краю листа. Затем следует отрегулировать угол срезки. Теперь можно включать машину: резцовая головка автоматически подведётся к зоне обработки, начнётся процесс снятия фаски. Когда процедура завершена, оборудование выключается, а резец перемещается, занимает исходную позицию. Далее осуществляется анализ качества. Если оно устраивает, можно переходить к последующим этапам производства.
Длительность снятия зависит от сложности процесса, от габаритов заготовки. Если фаска сложной формы, а технологическая операция с несколькими этапами и последовательной сменой инструмента, то на всё уйдёт много времени. В других случаях продолжительность процедуры – не более нескольких минут.
Снимать фаски нужно на полностью исправном оборудовании: перед операцией оно тестируется для выявления возможных поломок. Работы выполняются в подготовленной зоне, а оператор должен использовать средства индивидуальной защиты – очки, рабочий специальный костюм, маску-респиратор, а также наушники. Ещё одно важное правило – надёжное крепление заготовки. Его следует проверить перед стартом работ.
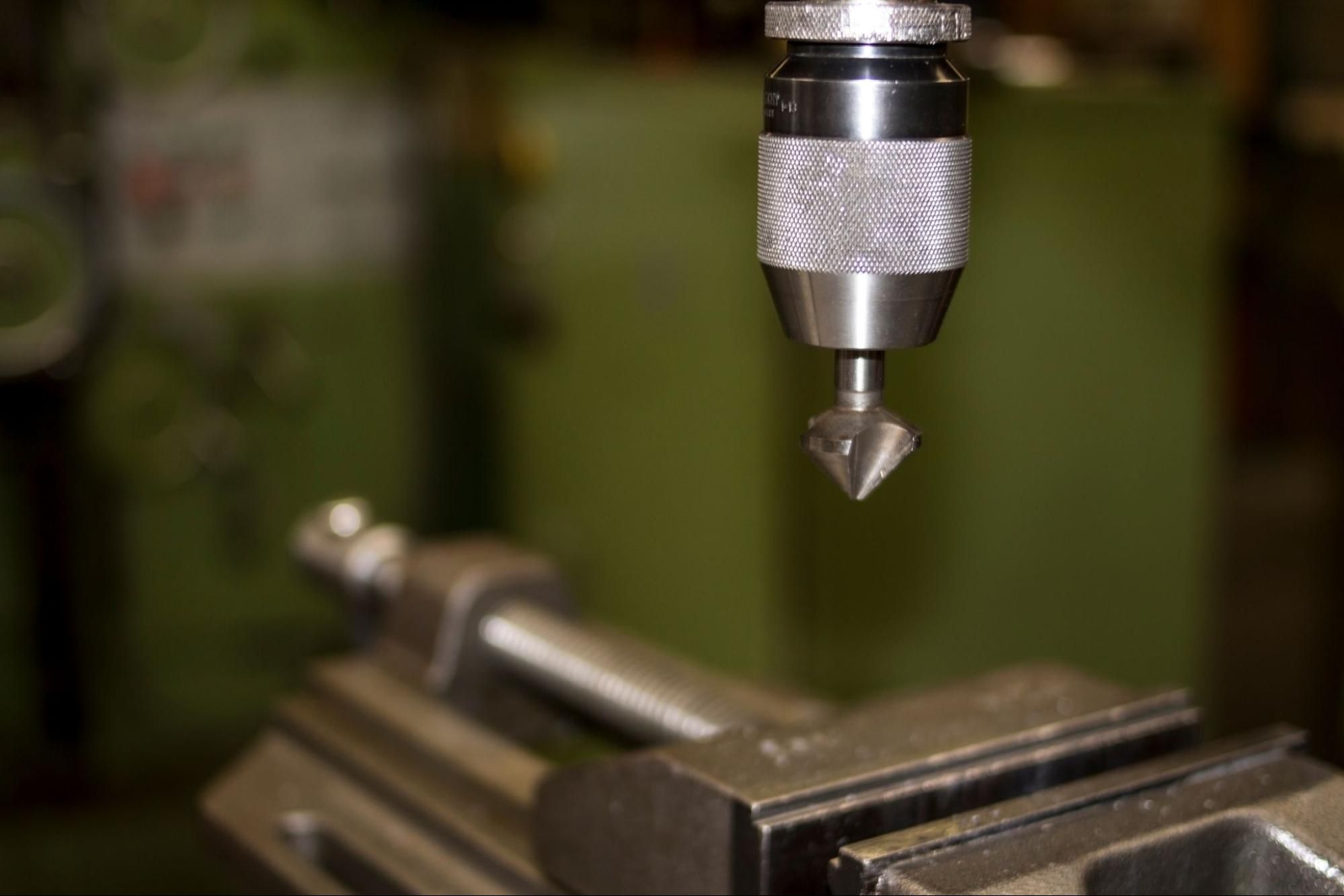
Почему необходимо выполнять снятие фаски?
Зачем нужна фаска на металле, почему так важно снимать её с некоторых деталей? Она, в зависимости от конфигурации поверхности, типа и назначения, может:
- Обеспечивать требуемое качество сварочных швов, надёжность создаваемых соединений, а также хороший провар, то есть степень достигаемого сплавления стыкуемых металлов. Если не снимать фаски с изделий толщиной от 5 миллиметров, то при активной эксплуатации прочность конструкции заметно снизится. Также вероятно расхождение сварочных швов.
- Сокращать время, затрачиваемое на работы. Благодаря улучшению сварочной ванны период сварки сокращается.
- Снижать риски получения сотрудниками металлообрабатывающих и производственных предприятий травм, обусловленных наличием острых граней и углов.
- Упрощать монтаж конструкций за счёт более качественной стыковки отдельных элементов.
- Не делать шлифовку краевых зон труб и листов вручную или с помощью инструментов, к примеру, шлифовальных машин.
- Дополнительно защищать от коррозии. На скошенной поверхности меньше, чем на остром краю, скапливается влага, грязь, пыль. Это снижает риски появления ржавчины, которая часто возникает именно на кромках.
- Улучшать эстетику. Вид детали после снятия фаски действительно становится более приятным, аккуратным, эстетичным.
- Защищать кромки от быстрого износа, от механических воздействий. При косом срезе вероятность сколов, расслоений, истирания краёв гораздо ниже, так как трение движущихся деталей минимальное.
- Обеспечивать необходимую функциональность. Иногда фаски снимаются, чтобы детали лучше работали, особенно в соединениях, механизмах. Так, в случае резьбовых отверстий обработка облегчает вход в них винтов, а также позволяет скрывать головки, чтобы они не выступали над поверхностью.
- Упрощать сборку. В механических разъёмных соединениях детали быстрее, легче устанавливаются, лучше и точнее выравниваются.
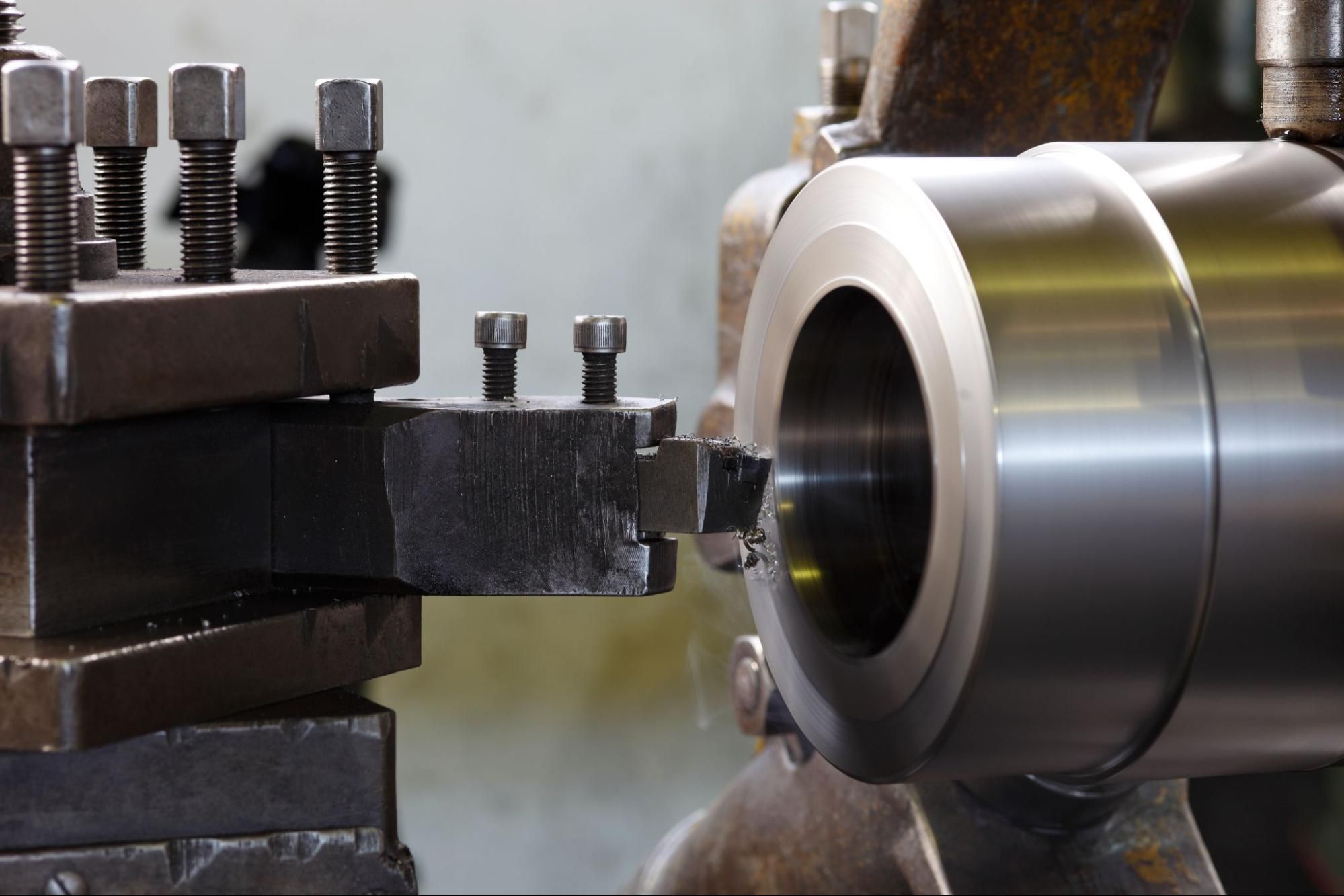
Заключение
Снятие фасок нужно доверять только профессионалам, чтобы получать отличные результаты. Компания Profbau выполняет такие работы профессионально, на современном оборудовании, с соблюдением технологий. Мы добиваемся максимальной точности, учитываем стандарты и требования клиентов, оказываем услуги оперативно и недорого.