Зенкерование отверстий – разновидность механической металлообработки, которая позволяет добиваться высокой точности и качества, соответствия диаметра и нужной степени гладкости. Такая операция проводится на специальных станках, требует соблюдения технологии и имеет некоторые особенности. В статье рассмотрим сущность зенкерования, его назначение, применяемые инструменты и оборудование.
Что такое зенкерование
Зенкерование – это получистовая обработка заготовки, имеющей отверстие. Последнее может быть сформировано на первых этапах производства при литье или штамповке либо позже, в процессесверления.
Название образовано от слова «зенкер». Так называется специальный инструмент, применяемый для выполнения операции. Он получил название от немецкого «senken», что в переводе на русский означает «углублять» или «проходить».
Технология
Штампованные, отлитые или просверленные сквозные или глухие отверстия обычно получаются неточными, требующими доработок для достижения нужного диаметра, геометрии, допустимой степени шероховатости. И для этого используют зенкерование, которое выполняется на специальном оборудовании. Обычно оно осуществляется перед другим этапом обработки – развёртыванием.
Для проведения операции используют сверлильный станок, но стандартное сверло в нём заменяется зенкером. Он похож на сверлильный инструмент, но имеет особую конфигурацию. Хотя принцип работы идентичен.
Зенкер фиксируется в патроне станка. Его хвостовик размещается в пиноли бабки после проверки совпадения бабки и шпинделя по оси. Зафиксированная заготовка вращается с заданной скоростью. Рабочий инструмент подаётся в зону и двигается поступательно.
Для достижения нужных результатов важно грамотно задать режим резания, главные параметры которого – это частота оборотов инструмента при вращении, глубина резания и необходимые припуски. Всё это определяется с учётом состава и характеристик материала, а также изначальных размеров и диаметра и конечных геометрии и габаритов.
Скорость вращения составляет обычно от 40-50 м/мин до 100-150. Её, как и скорость и глубину резания, определяют по специальным формулам. Так, глубина – это припуск на диаметр (разница между окончательным значением и первоначальным), делённый на два. В современном оборудовании достаточно установить необходимые параметры, чтобы электронный блок самостоятельно задал подходящие настройки для последующей работы.
Важно знать! Так как зенкерование относится к точным операциям, проводить его классической электрической дрелью или вручную нельзя. Допустимо использование только станка с настройками и автоматизацией процесса.

Назначение зенкерования
Назначение рассматриваемой металлообработки – это максимальная точность размеров деталей, которая должна соблюдаться до микронов. Любые неровности провоцируют проблемы при функционировании конструкций, состоящих из элементов с отверстиями. К возможным последствиям относят люфт, преждевременный износ, сбои в работе, поломки.
Зенкерование позволяет достигать следующих целей:
- Добиваться строго цилиндрической формы каналов по всей протяжённости. Это необходимо, чтобы тяги, валы, шпиндели, резьбовые соединения проходили через отверстия без зазоров, без трения, без повышенного напряжения.
- Сохранять диаметр по всей длине. Это сокращает люфт, предотвращает быстрый износ металлов, а также продлевает сроки эксплуатации передаточных механизмов.
- Расширять отверстия, если они не соответствуют заданным параметрам – меньше по диаметру, чем требуется.
- Убирать дефекты, возникшие при производстве путём литья, ковки, штампования.
- Увеличивать показатели конечной чистоты канала. Уменьшая шероховатость и получая требуемую гладкость, можно сокращать количество образующейся при трении и вибрациях стружки, а также делать конструкцию более долговечной, надёжной.
Если класс точности отверстия находится в пределах 3-го, то зенкерование с последующим развёртыванием обязательно. Оно применяется для литых, кованых, штампованных изделий, а также просверленных.
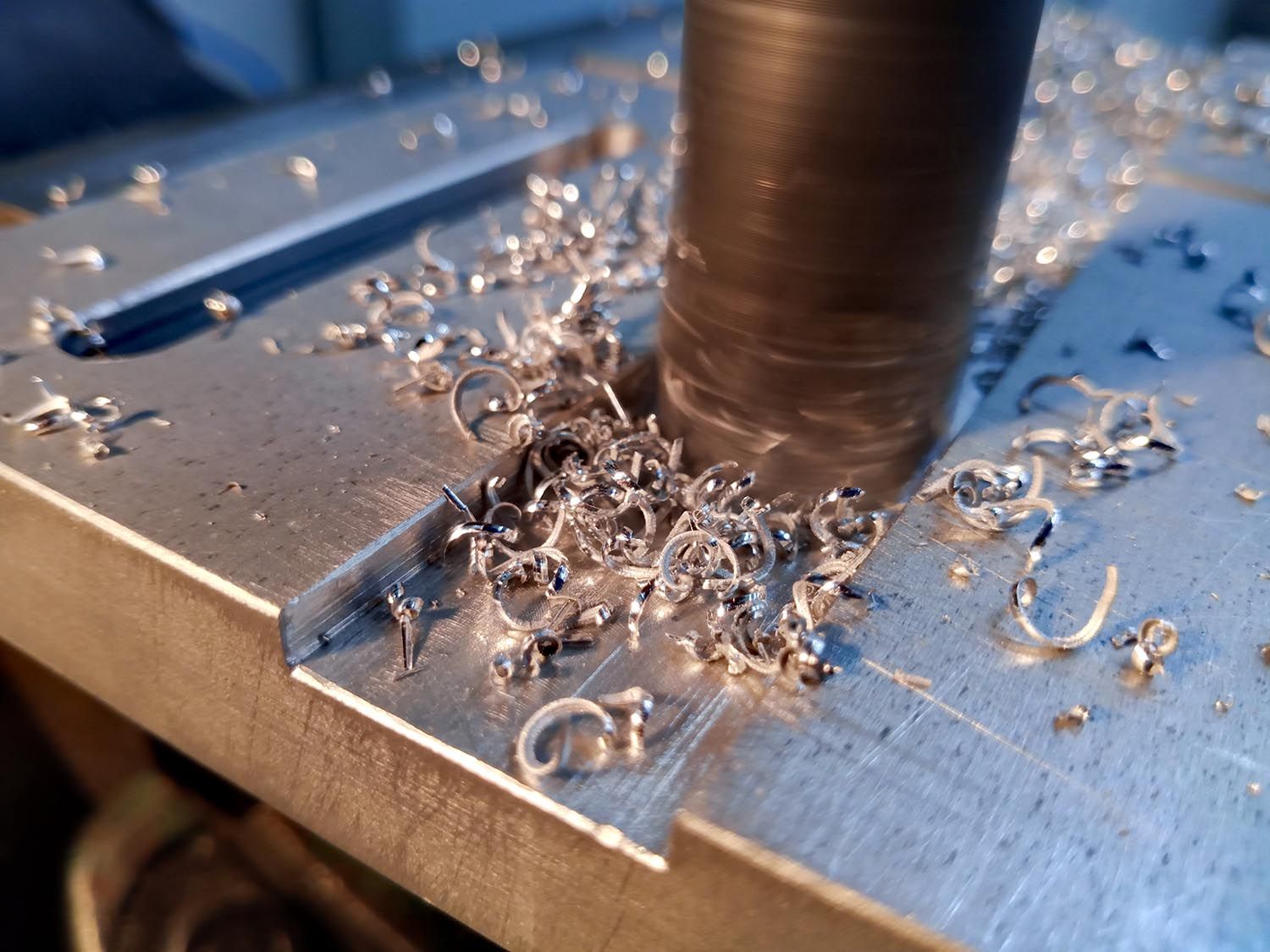
Принцип зенкерования металла
Принцип обработки связан с резанием посредством рабочего инструмента, оснащённого располагающимися по спирали режущими кромками. Они при прохождении зенкера через сформированный канал снимают с поверхности металла тонкий слой. Его удаление осуществляется при движении. Первый вариант – одновременные вращательные и поступательные перемещения зенкера. Второй – вращение заготовки и поступательное движение инструмента.
Процесс имеет такие особенности:
- Правильный подбор зенкера. Он должен иметь подходящую конфигурацию и диаметр, который позволит получить конечный заданный размер отверстия.
- Использование токарного либо сверлильного станка, в котором инструмент закрепляется в участке хвостовика (основания).
- Обрабатываемая заготовка устанавливается и фиксируется так, чтобы её канал находился напротив инструмента и совпадал с ним по оси.
- На станке устанавливают настройки: частоту оборотов вращения шпинделя (он приводит в действие зенкер), скорость резания и его глубину. На такие параметры влияют вид и размер рабочего инструмента, начальный и конечный диаметры, а также свойства металла или состав сплава, который предстоит просверливать.
- В некоторых случаях в зону обработки для исключения перегрева подаётся охлаждающая специальная жидкость.
- У зенкера много острых выступов, что обусловливает его большую жёсткость (по сравнению со свёрлами). Именно это обеспечивает качественную обработку, чистоту поверхностей, точность направления перемещения. При сверлении квалитет (совокупность допусков) 11 или 12, а шероховатость составляет около 20 микрометров. При зенкеровании показатель шероховатости – всего 2,5 мкм. Квалитет – от 9 до 11.
Отличия зенкерования от зенкования
Есть другой процесс, который называется похоже – зенкование. Но он не идентичен зенкерованию. С помощью зенкеров отверстиям придают максимальную точность – соответствие заданным диаметру, степени гладкости, форме.
При зенковании используют другие инструменты – зенковки. Ими снимают фаски, формируют опорные круговые плоскости, а также создают вокруг каналов углубления цилиндрической или конической формы. Это необходимо, если нужно получить переходную кромку между гранями, сделать гнёзда для скрытого монтажа винтов, заклёпок, болтов и другого крепежа с потайными головками.
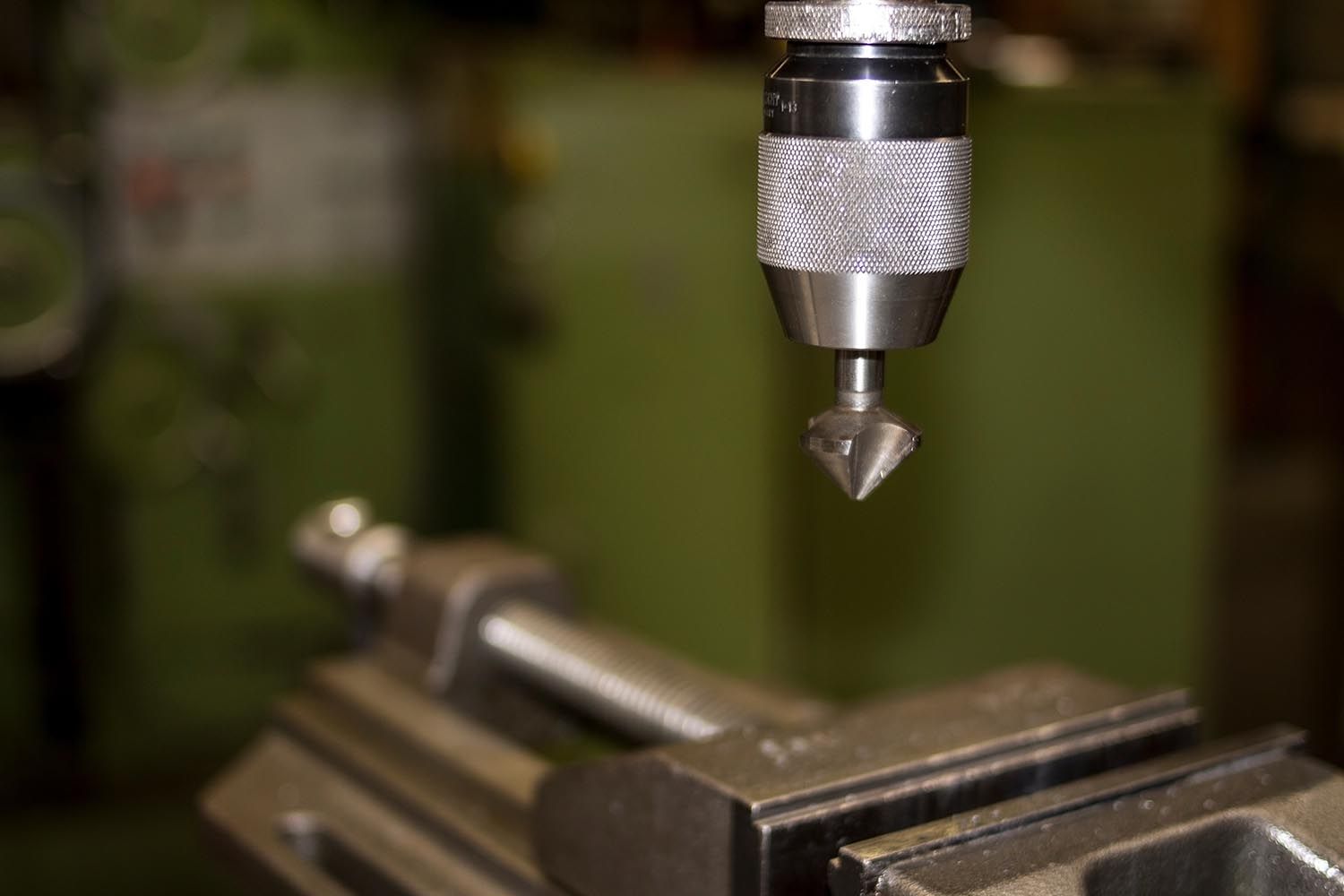
Виды и конструкция зенковок
Зенковка является многолезвийным режущим элементом и состоит из хвостовика (основания, фиксируемого в станке) и рабочей головки. Хвостовик оснащается направляющей цапфой, обеспечивающей стабильность оси при выборке выемок.
Зенковка применяется в токарных или сверлильных станках, а также в обрабатывающих многокоординатных центрах. Электродрели или другие ручные инструменты эксперты советуют не использовать, так как с их помощью невозможно добиваться соосности и минимальных погрешностей.
Зенковки бывают:
- Коническими. Ими формируют углубления, имеющие конфигурацию конуса. Это могут быть выемки для последующей установки крепежа, снимаемые фаски, конические заглубленные зоны в нижней части каналов.
- Цилиндрическими. С их помощью вокруг отверстий в верхних частях каналов создают цилиндрические выемки, в которых можно скрывать головки крепёжных элементов – заклёпок, гаек, винтов. Цилиндрическое зенкование популярно в разных производствах.
- Торцевыми, плоскими. Такие инструменты называют цековками. Они призваны зачищать ранее созданные выемки для фиксации креплений. Благодаря торцевому зенкованию можно добиться плотного вхождения и прилегания шляпок без зазоров.
По диаметру зенковки делятся на малые (от 0,5 мм до 1,5), средние (1,5-6 мм) и крупные (7-12 миллиметров). Все инструменты изготавливаются в соответствии с действующими в России ГОСТ.
Основные правила обработки зенкерованием
Чтобы выполнить зенкерование грамотно, нужно строго соблюдать его технологию. Она определяется для конкретных деталей с учётом множества исходных условий, к которым относятся цель производимых работ (например, удаление шероховатости или расширение), свойства металла, тип обрабатывающего инструмента, а также характеристики канала – его длина, начальный диаметр, конфигурация. Берутся во внимание и ожидаемые результаты – нужная гладкость, итоговый размер канала.
Действуют следующие правила:
- Выбор зенкера осуществляется по типу отверстия, которое может быть сквозным, глухим или сложным ступенчатым.
- Для отверстий, полученных штамповкой, просверливанием или отливкой, припуск на зенкерование находится в диапазоне 0,5-3 миллиметра.
- Скорость вращения резца, выполненного из быстрорежущей прочной стали, такая же, как и для стандартных свёрл по металлу.
- Если кромки резца выполнены из твердосплавного материала, их скорость вращения может быть в два или три раза выше, чем для обычных зенкеров.
- Для высокоточной обработки глубоких каналов, полученных штампованием или при литье, перед получистовой зенкеровкой выполняют предварительный черновой проход резцом. Материал при этом обрабатывается на глубину ½ части рабочего тела зенкера. А по диаметру резец совпадает с режущей кромкой.
- Если рабочий инструмент из быстрорежущей стали, то его головка и обрабатываемый канал охлаждаются и смазываются специальным составом. Это исключает чрезмерное трение и перегревание.
- Мастера для работы используют схемы, в которых рабочие процессы описываются латинскими буквами: L1 – цилиндрический путь, L4 – величина фаски, L3 – глубина воздействия зенкера, J – угол отклонения, d1 – основной, то есть начальный диаметр, d2 – значение конечного, требующегося диаметра.
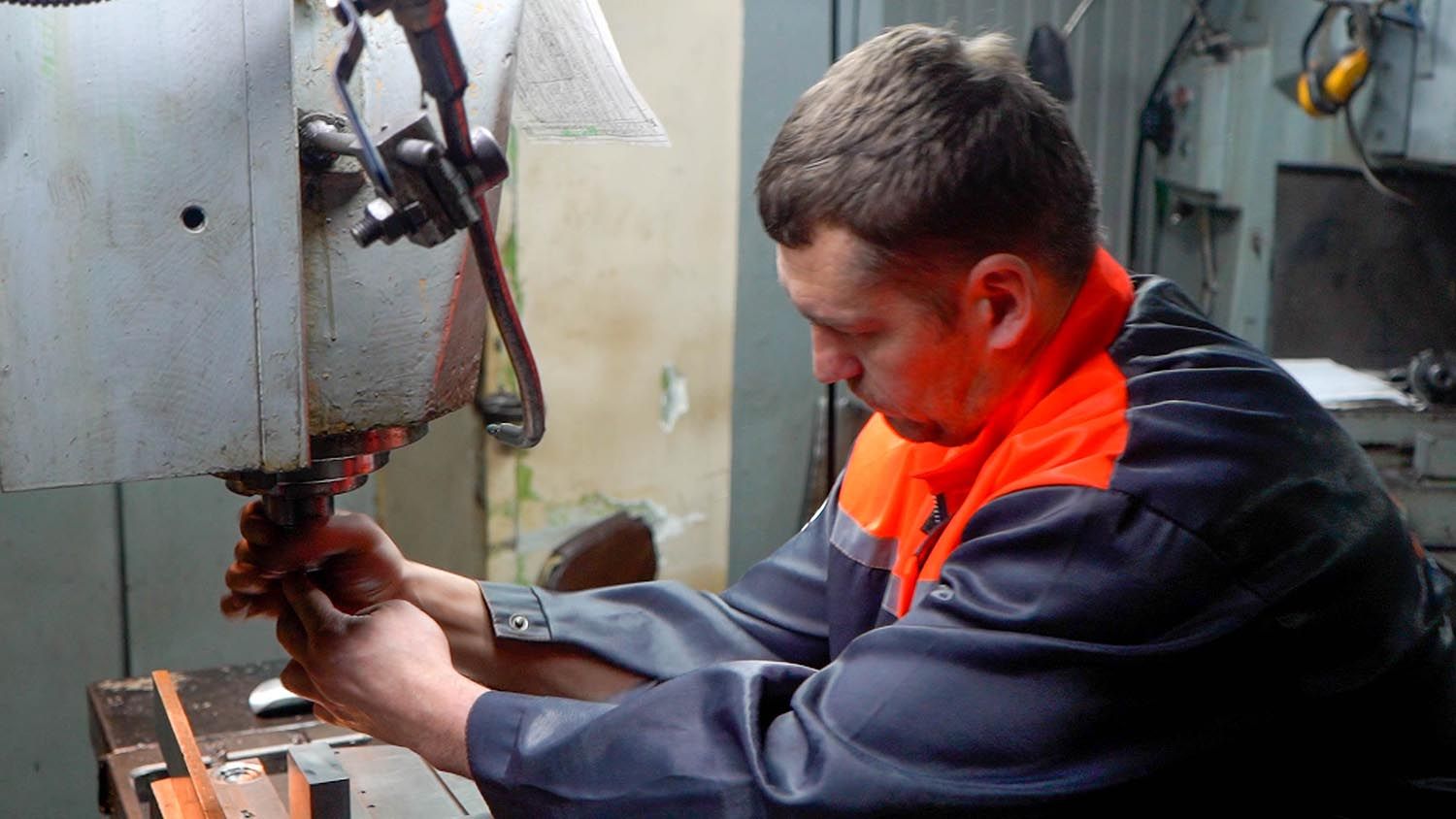
Оборудование
Чтобы своими руками расширить отверстие, например, под болт или винт, можно воспользоваться обычной ручной электродрелью и оснастить её классическим сверлом. Но стенки канала при этом не будут достаточно гладкими.
Если же нужно добиться максимальной точности и минимальной шероховатости, то следует применить зенкер, который может монтироваться в станки следующих видов:
- Сверлильные. Именно их используют наиболее часто из-за конструктивной схожести свёрл с зенкерами.
- Токарные. Применяются для зенкерования очень часто.
- Расточные. Эти агрегаты подходят больше для проведения вторичных, вспомогательных операций.
- Вертикальные и горизонтальные фрезерные. Обычно это современные автоматизированные модели с ЧПУ (числовым программным управлением), в которых зенкерование является этапом сложной многошаговой программы.
- Агрегатные. В таких устройствах зенкеры внедряются при необходимости добавления вспомогательной операции в автоматическую технологическую линию.
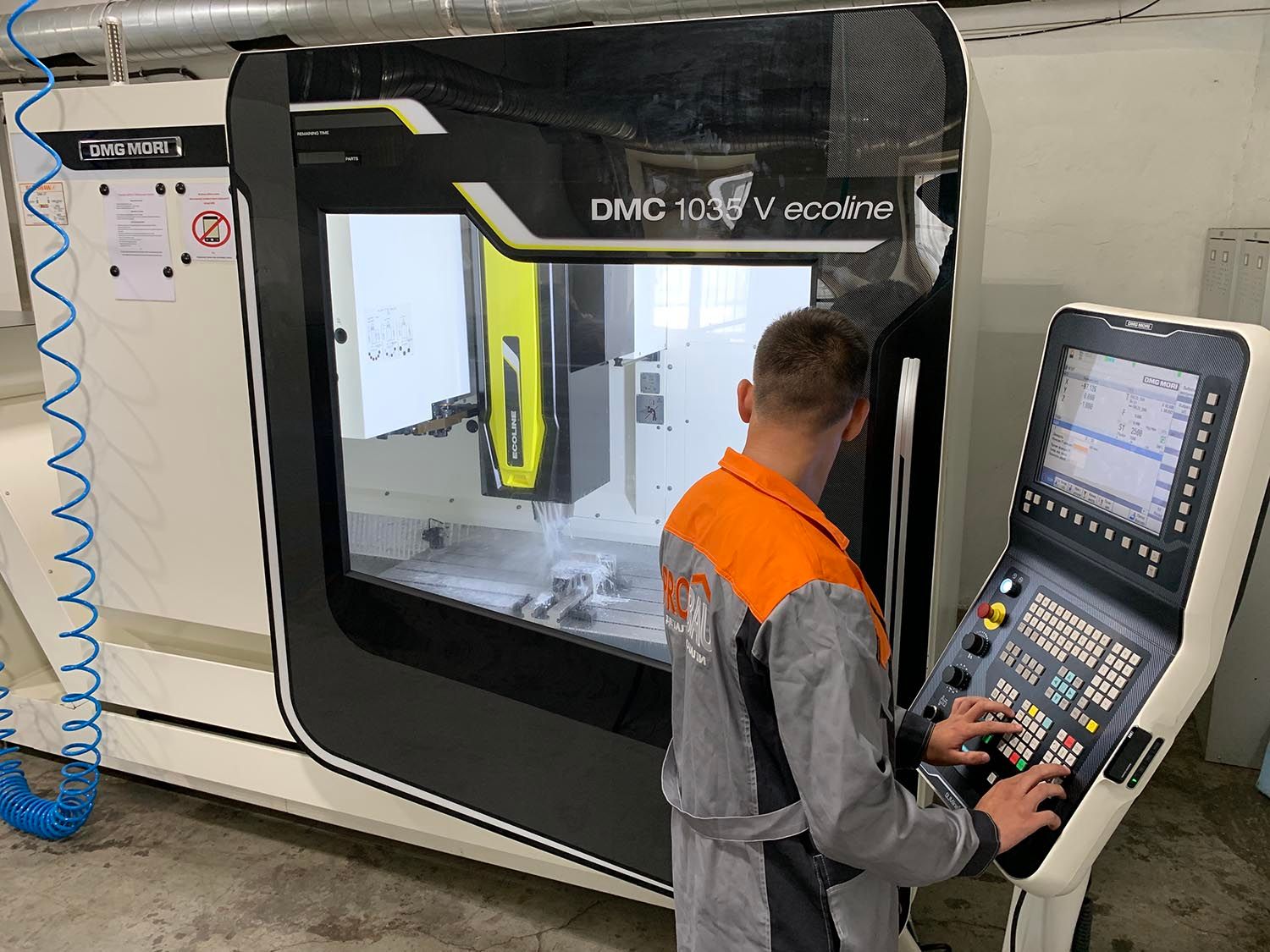
Инструменты
Для проведения рассматриваемой в статье металлообработки используются зенкеры. В конструкции предусмотрено три части:
- Хвостовик. Зона, фиксируемая в патроне сверлильного, фрезерного, токарного или другого оборудования. Это основание.
- Рабочая часть. Она включает калибрующую и режущую зоны, которые снимают поверхностный слой металла и обеспечивают выравнивание поверхности. Количество лезвий может варьироваться от 3-4 до 10-12.
- Шейка. Промежуточный участок, располагающийся между хвостовиком и режущей частью. Она защищает станок от повреждений и поломок: при перегрузке или нарушении режима работы зенкер лопнет именно в области шейки, что позволит беспрепятственно извлечь хвостовик из патрона и рабочую часть из канала. Само оборудование при этом не пострадает.
По конструкции зенкеры делятся на:
- цельнометаллические с коническими хвостовиками;
- насадные, насаживаемые на вращающийся элемент станка и оснащаемые твердосплавными резцами;
- с хвостовиками и режущими кромками с напаянными пластинами из твердосплавного материала;
- насадные со вставными ножами.
Зенкеры обычно изготавливают из быстрорежущих легированных сталей, выдерживающих большие нагрузки и подходящих для высоких скоростей резания, а также из твёрдых сплавов с добавлением тугоплавких металлов, таких как вольфрам, титан, хром, тантал и другие химические элементы.
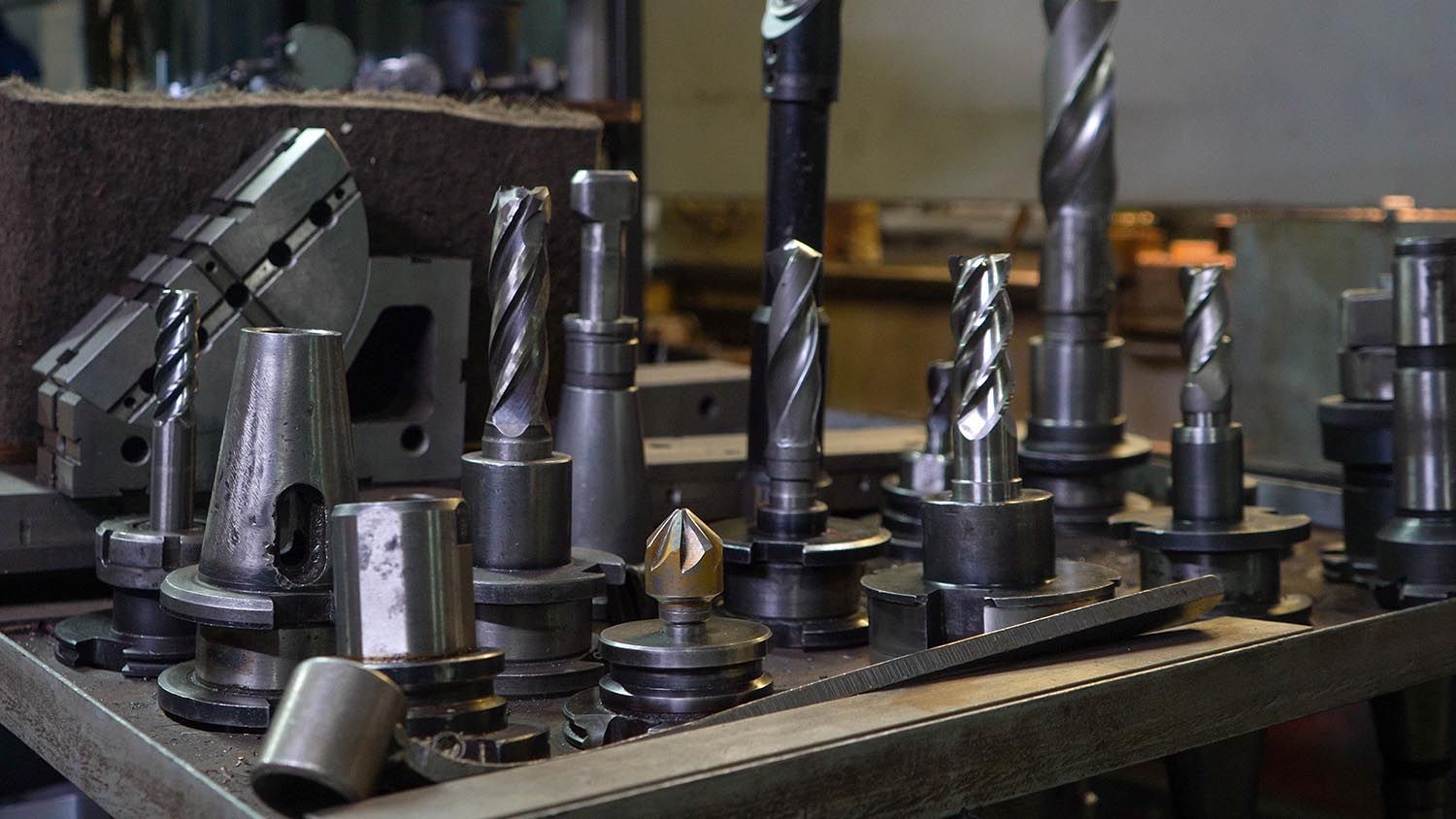
Как правильно выбрать инструмент
От выбора зенкера зависят напрямую результаты обработки. Подбирая его, нужно учитывать несколько главных факторов:
- Материал заготовки. Он определяет необходимую твёрдость металла инструмента, скорость его вращения и поступательных движений.
- Диаметр канала, его глубина, требуемая точность обработки. Всё это влияет на размер и конфигурацию инструмента, например, количество лезвий.
- Способ крепления. Он зависит от вида станка, а также от конструкции зенкера.
- Интенсивность обработки. Чем она выше, тем более прочным должен быть инструмент.
- Опыт мастера. Так, если он небольшой, есть смысл выполнить зенкерование в два этапа: с первичным снятием слоя для расширения отверстия и с финишной обработкой для получения гладкой поверхности.
Выбирая зенкер, нужно изучить информацию, указываемую в специализированной справочной литературе. Также надо знать технические условия и нормативы, регламентированные государственными стандартами. Для зенкерования действует ГОСТ под номером 12489-71. В нём есть следующие положения:
- Для заготовок из конструкционной стали с отверстиями не больше 40 миллиметров в диаметре применяют инструменты из быстрорежущей стали. Для резки достаточно трёх или четырёх зубцов. Диаметр зенкера составляет от 10 мм до 40.
- Если предмет изготовлен из труднообрабатываемой стали или закалённой, то для расточки необходима оснастка с твердосплавными пластинами от 14 мм до 50 в диаметре. Количество зубьев – три или четыре.
- Для деталей из конструкционных сталей с отверстиями, которые в диаметре не превышают 80 мм, подбирают рабочие элементы из быстрорежущих сталей. Их насадные головки имеют размер от 32 миллиметров до 80.
- Для чугунных заготовок и сделанных из цветных металлов подходят перовые зенкеры, предназначенные для глухих отверстий.
- Если отверстие глухое и имеет диаметр от 15 миллиметров до 25, то нужна специальная оснастка – с корпусом, в котором имеется канал. Через него в обрабатываемую область подаётся охлаждающая смесь.
Очень важно грамотно подобрать диаметр оснастки. Он должен совпадать с конечным диаметром изделия. Если за зенкерованием последует чистовое развёртывание, то диаметр инструмента может быть меньше стандартного на 0,15-0,3 миллиметра. При предварительной подготовке отверстий и перед черновым растачиванием можно оставлять припуск на сторону, равный от 0,5 мм до 2 мм.
Сферы применения зенкерования
Зенкерование нашло применение в различных направлениях промышленности: в машиностроении, авиационной отрасли, судостроении, станкостроении, автомобилестроении. Также высокая точность отверстий обязательна в электротехнике, электронике, бытовой технике.
Обработка используется при производстве различных деталей и элементов сложных конструкций: торцевых прокладок, корпусов двигателей, опорных дисков. Любая продукция благодаря качественному зенкерованию соответствует высоким стандартам и жёстким требованиям.
Зенкерованием возможно:
- получать ровные и чистые стенки отверстий перед нарезанием резьбы, перед развёртыванием;
- калибровать отверстия под шпильки, болты и другие крепёжные детали;
- корректировать профили отверстий, например, чтобы увеличить верхнюю зону углубления под головку крепежа;
- обрабатывать торцы.
Зенкерование – одно из направлений деятельности компании Profbau. Мы выполняем такую металлообработку качественно, точно в срок и с соответствием всем требованиям благодаря высокой квалификации и профессионализму сотрудников, использованию современного оборудования, тщательному подбору инструментов и строгому соблюдению технологии. Чтобы узнать подробности, можно позвонить нам, написать на электронную почту, оставить заявку на сайте или приехать в офис.