Есть разные способы обработки металлов и сплавов. Одни требуют повышенных температур, другие предполагают отливку расплавленного сырья в формы, третьи включают воздействие электротока или отдельных химических веществ. Но самой популярной остаётся механическая обработка металла. О ней расскажем подробно в этой статье.
Что такое механическая обработка металла
Механическая обработка – это внешнее воздействие, требующее применения вспомогательных средств и предполагающее изменения внешних параметров изделия: его конфигурации, степени гладкости или шероховатости, габаритов. При этом структура, то есть строение материала сохраняется, но могут корректироваться физико-химические свойства.
В качестве средств, провоцирующих изменения параметров, используются различные инструменты. Это метчики, сверла, фрезы, протяжки, резцы. Все операции проводятся на оборудованных металлообрабатывающих предприятиях, со строгим соблюдением техники безопасности, по технологическим картам, а также с соответствием имеющимся заданиям, чертежам и ГОСТ (распространяются на стандартизированные изделия).
Согласно технологическим планам, используемым на фабриках и заводах и описывающим последовательное выполнение операций, под механической обработкой подразумевается подгон заготовок, полуфабрикатов и деталей под заданные, установленные стандартами или индивидуальными требованиями характеристики. После процесса металлоизделия обретают нужные размеры и формы, поэтому могут корректно устанавливаться в механизмах, внедряться в многокомпонентные узлы, использоваться по назначению.
История
Люди начали осуществлять обработку уже тогда, когда получили первые инструменты, способные менять свойства металлов. Эти приспособления создавались из высокопрочных материалов, способных воздействовать на более мягкие составы. Инструменты имели особую конструкцию и применялись так, чтобы риски необратимых повреждений обрабатываемых предметов были минимальными.
Раньше точность была неважной. Технологии прошлого были примитивными, поэтому не позволяли добиваться строгого соответствия определённым характеристикам. Да и необходимости точного соблюдения требований просто не было.
Когда в мире началась индустриальная революция, домашние мастерские, в которых использовались ручные инструменты, постепенно стали заменяться фабриками и мануфактурами. Их масштабы и мощности, а также внедрение станков позволяли запускать серийные производства и изготавливать однотипные металлические изделия практически с идентичными характеристиками.
Важность точной мехобработки возникла при запуске первых оружейных производств. Продукция должна была отвечать строгим требованиям, так как имела специфическое назначение и не могла давать осечек. В то время начали разрабатывать станки, которые помогали рассверливать дула винтовок и другого оружия, шлифовать и полировать корпусы. Из оружейной промышленности механическая обработка начала стремительно распространяться и в другие сферы.
Сферы применения
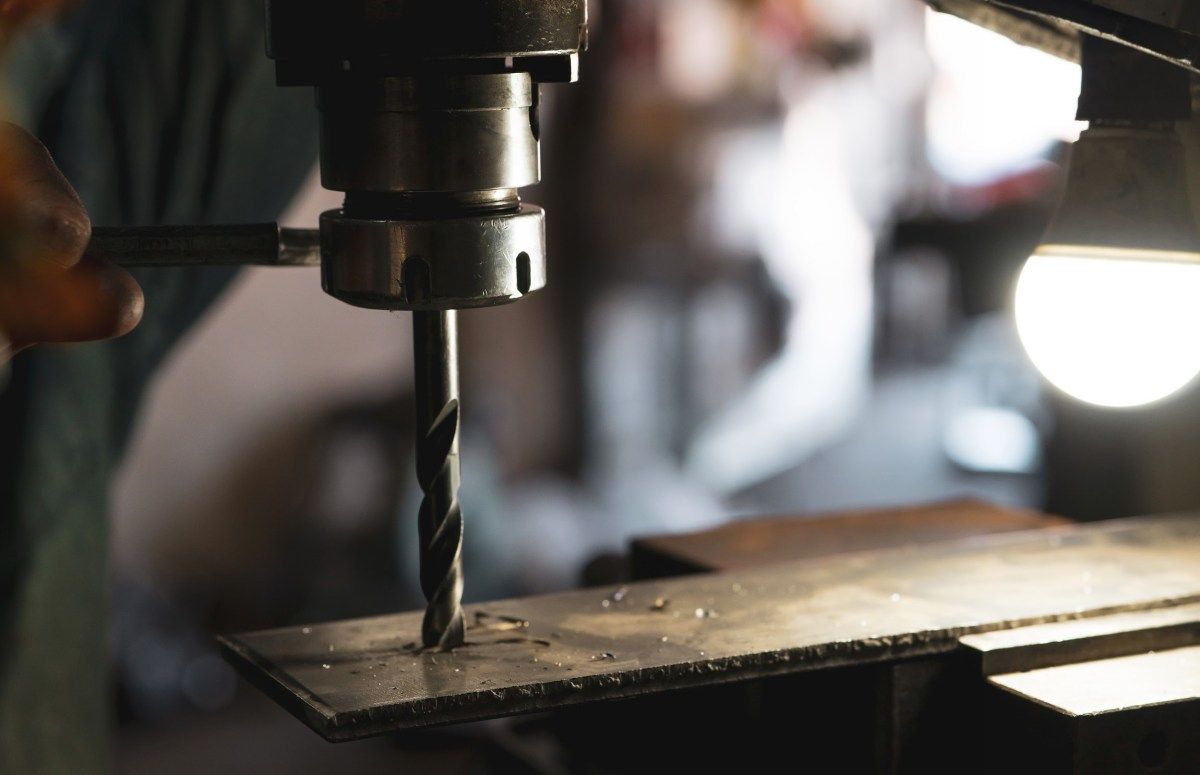
Механообработка нужна везде, где требуется получать металлические изделия с заданными размерами, геометрией. Технология получила широкое распространение и используется в различных сферах:
Для некоторых целей, в промышленных секторах со специфической и узкоспециализированной деятельностью необходимы нестандартные металлоизделия. Найти их на современном рынке не всегда удаётся. Единственное решение – механообработка, выполняемая по индивидуальным техническим заданиям или чертежам. Сегодня это возможно благодаря многочисленным передовым технологиям, автоматизированному оборудованию, отточенным навыкам мастеров и их профессионализму.
Способы механической обработки металлов
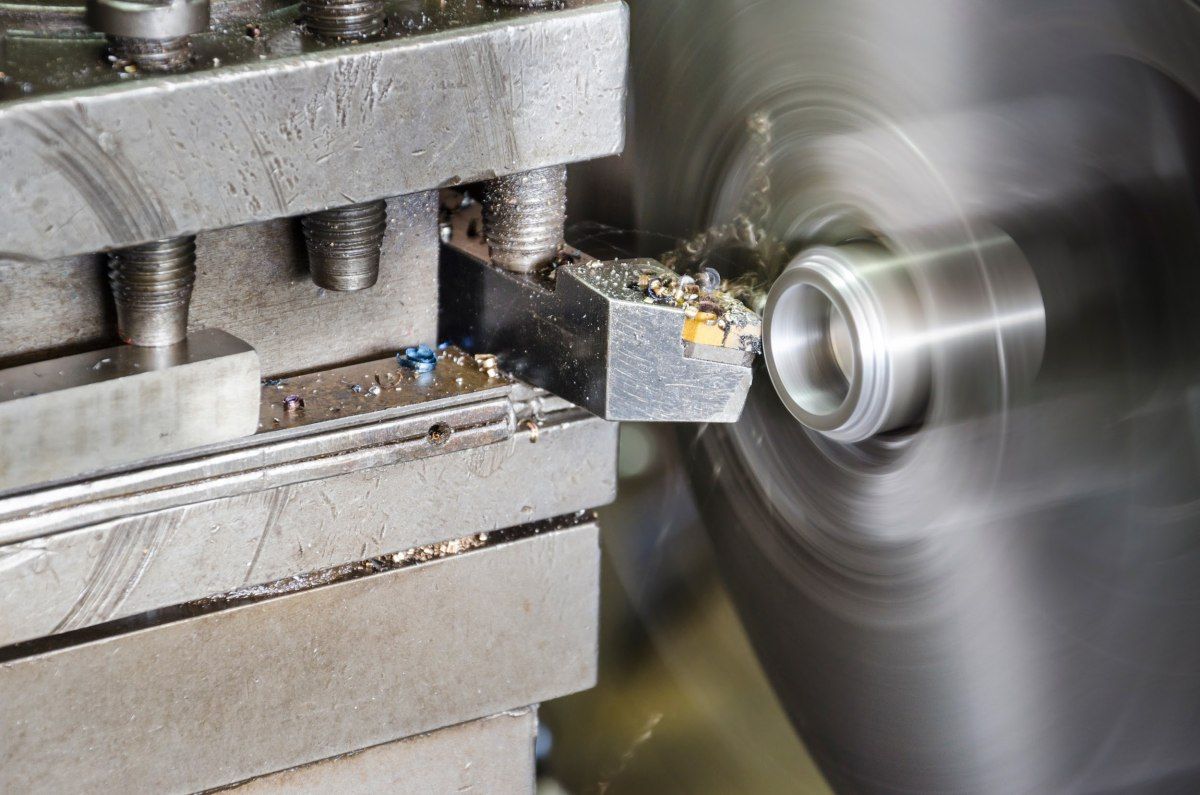
Все существующие способы делятся на две группы. Первая предполагает снятие поверхностных слоёв. Они удаляются с помощью специального инструмента, обязательно имеющего режущие кромки. Это развертки, метчики, свёрла, резцы. Они устанавливаются в станы, предназначенные для проведения отдельных специфических операций или для решения различных задач (многофункциональные модели).
К способам, при которых верхние слои удаляются, относят долбление, фрезерование, шлифование, зенкерование, сверление, строгание, точение. Они могут применяться отдельно или комбинироваться. Иногда требуется сначала подогнать заготовку под заданные конфигурацию и размеры, а потом обточить её, довести до нужной гладкости шлифовкой.
Второй тип – это металлообработка, при которой поверхностные слои остаются. Воздействие оказывается обычно сильными ударами или значительным давлением. Металлы сохраняют свою массу, но меняют геометрию. В эту категорию входят штамповка, волочение, ковка, прессование, прокат. Также существуют методы с применением подаваемого под большим давлением воздуха, воды, потока частиц с абразивными свойствами.
Выбор осуществляется с учётом следующих факторов:
Основные виды механообработки
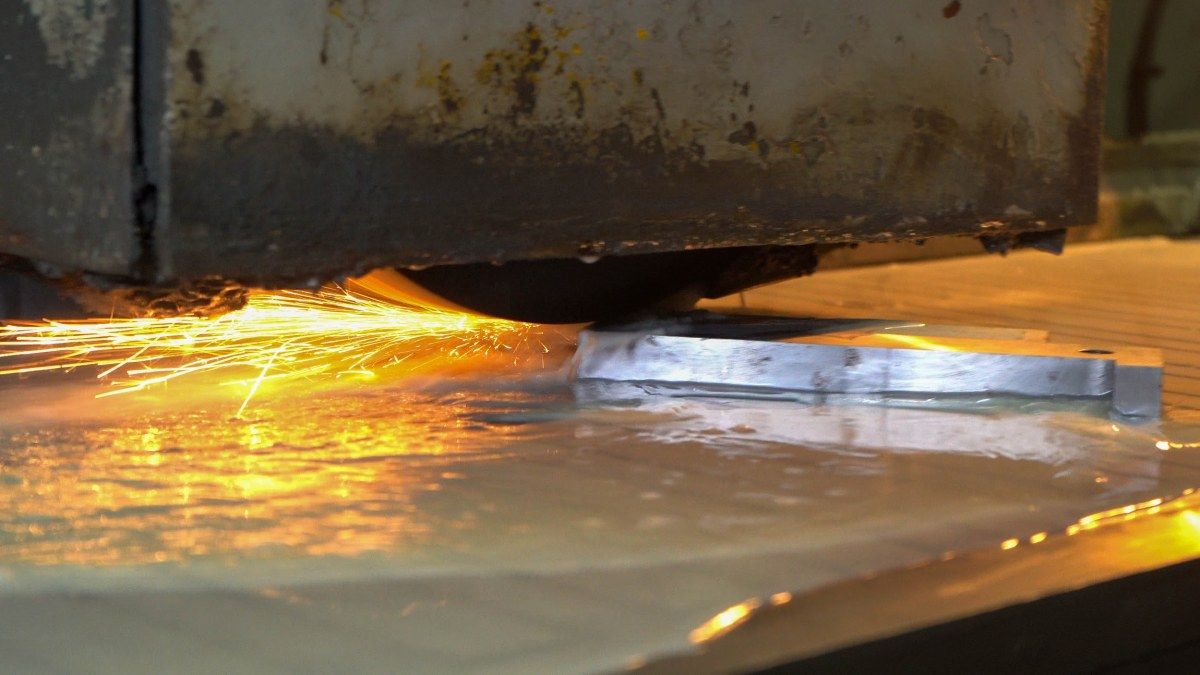
Есть разные виды механообработки. Они используются отдельно, самостоятельно или в комбинациях, если необходим многоэтапный, последовательный процесс. Рассмотрим популярные разнообразные методы.
Штамповка
При ней происходит пластическая деформация. Вариант применим к чёрным металлам и состоящим из них сплавам, позволяет максимально сохранять целостность полуфабрикатов. Агрегаты для штамповки задают значительное давление, резко и с большой скоростью направляемое на всю деталь или её отдельную рабочую зону. Такое влияние дополнительно увеличивает прочность за счёт повышения плотности материала.
Выделяют два вида: листовая штамповка и объёмная. В первом случае формируют плоские детали. При объёмном варианте детали получаются объёмным. В штамповочном станке два главных рабочих элемента – пуансон и матрица. Одна часть остаётся неподвижной, а вторая перемещается. Между ними размещается обрабатываемая заготовка и штамп с очертаниями, которые должна в итоге обрести деталь. Излишки перемещаются в зазоры и отводятся. Есть агрегаты без зазоров. Чтобы использовать их правильно, нужно проведение точного расчёта исходных размеров, объёма полуфабрикатов.
Штамповка бывает отрезной и формообразующей. При последней деталям придаются определённые изгибы. А отрезной метод предполагает фигурную резку, применяемую обычно на листах.
Прессование
Напоминает штамповку, но отличается более щадящим воздействием: рабочие элементы перемещаются медленно, сдавливая заготовки постепенно. Такой вариант подходит для хрупких металлов, например, алюминия, чугуна.
Перед стартом основных работ полуфабрикаты могут нагреваться. Далее они крепятся в матрице с отверстиями. Пресс перемещается и выдавливает материал. Матрицы выполняются из жаропрочных сталей.
Холодное прессование без нагревания подойдёт для олова, алюминия, меди. А горячее используют для сплавов с титаном и никелем, для чугуна.
Прокат
Прокатная технология позволяет получать трубы, листы. Заготовки пропускаются через систему вальцов. При сдавливании профиль детали получает необходимую конфигурацию, а поперечное сечение уменьшается. Полуфабрикат во время проката может сжиматься в поперечном направлении, продольном или в поперечно-винтовом. Подбор варианта требует учёта конечных исходных характеристик.
Фрезерование
Метод, суть которого заключается в обработке фрезами, оснащаемыми режущими лезвиями (кромками), располагающимися по спирали. Такие рабочие элементы устанавливаются во фрезерные станки и с нужной скоростью вращаются. На них подаются заготовки, с которых снимаются поверхностные слои в виде стружки. Фрезеруемые детали могут располагаться горизонтально, под углом, вертикально. Обычно таким способом формируют углубления. Фрезерование может быть периферийным, торцевым, фасонным, концевым.
Точение
Оно выполняется на токарных станках, в которых устанавливаются резцы. Заготовка крепится на шпинделе и осуществляет вращения вокруг собственной оси. Резец же движется в продольном, поперечном или комбинированном поперечно-продольном направлении.
Заготовки, как правило, конические или цилиндрические. Это всевозможные тела вращения: валы, пальцы, фланцы, диски, кольца, муфты, втулки, цапфы, гайки. С помощью точения их можно подрезать, обтачивать с наружной стороны, растачивать внутри, а также создавать резьбы, канавки.
Точение бывает черновым, выполняемым на первых этапах металлообработки, а также чистовым, которое формирует окончательные формы, размеры и гладкость, подготавливает детали к установке в конструкции, к эксплуатации.
Современные токарные станки имеют числовое программное управление – сокращённо ЧПУ. При нём параметры, которые нужно получить, заносятся в компьютерную программу через модуль управления. А установленное на агрегате ПО передаёт настройки на автоматизированную рабочую зону. Операции проводятся по заданным параметрам, с максимальной точностью, минимальной вероятностью отклонений.
Волочение
При нём сокращается поперечное сечение. Заготовки пропускаются через волочильные станы и получают необходимый диаметр. Именно так делают проволоку. Волочение бывает влажным и сухим, горячим и холодным, черновым и чистовым, многократным и однократным.
Сверление
Его можно отнести к технологии резания. Цель – сформировать сквозное либо глухое отверстие необходимых глубины и диаметра. Для этого используют свёрла, которые имеют заострённые кромки и быстро вращаются. Отверстия требуются для фиксации крепежа типа болтов, а также для дальнейшего создания резьбы.
В промышленных масштабах сверление реализуется на сверлильных станках. В них фиксируют заготовки с помощью зажима или тисков. Далее монтируется оснастка. Она подбирается по длине, диаметру и материалу с учётом размеров будущего отверстия, характеристик материала (прочности, пластичности). Затем начинается сверление, при котором изделие не перемещается, а сверло углубляется в него с одновременным осевым вращением.
Свёрла производятся из сталей (обычно углеродистых), а для особо прочных материалов подходят алмазные инструменты. Сверлить отверстия можно и самостоятельно, вручную. Для этого используют обладающие высокой мощностью шуруповёрты, электрические дрели.
Зенкование
Таким способом в металлических изделиях обрабатывают отверстия. Они к моменту зенкования уже готовы и только доводятся до соответствия технической документации. Решаемые задачи могут быть следующими:
Главный рабочий инструмент – зенковка. Это многолезвийный элемент, который острыми кромками снимает фаски. Процесс относительно несложен, если специалист имеет должный опыт.
Есть другая процедура, именуемая зенкерованием. Но при ней воздействию подвергается весь канал полностью. Зенкование же затрагивает только начальную зону отверстия.
Зубофрезерование
Подвид фрезерования, для которого также применяют многолезвийные фрезы, но имеющие специфическую форму. Это оснастка червячного типа, которая, как и стандартная, вращается, создавая выступы – зубья определённого профиля.
Данная технология реализуется на зубофрезерных станках, на которых получают различные детали: шестерни, зубчатые прямозубые и косозубые колёса, используемые в цепных передачах звёздочки, венцы, муфты. Всё это востребовано в авиационной и машиностроительной промышленности, в автомобилестроении, в некоторых других областях.
Шлифование
Шлифовать можно автоматически на специальных агрегатах или ручными инструментами. После завершения такого технологического процесса деталь доводится до нужного уровня качества, обретает допустимую степень шероховатости или нормированную гладкость.
Шлифование – обычно завершающий этап. При нём с поверхности изделия убирается тончайший слой, который по толщине иногда не превышает несколько микрон. Работы проводятся шлифовальными вращающимися кругами. Они различаются по зернистости, то есть величине зёрен (абразивных частичек). Материалы кругов определяются по составу шлифуемых металлоизделий. А зернистость зависит от требуемой гладкости: чем она выше, тем мельче зёрна.
Нарезание резьбы
Резьбы нарезаются для формирования резьбовых соединений, которые используются для сборки различных конструкций, например, трубопроводов. Используют разные способы, рассмотренные ниже.
Резцами
Для работ применяют токарные универсальные станки с устанавливаемыми в них резцами. Последние перемещаются вглубь заготовок, вращающихся по своей оси и закреплённых в державке оборудования. Благодаря винтовому ходу создаётся чередование выступов и канавок, формирующих резьбу: наружную или внутреннюю.
Такой вариант больше подойдёт для штучного или мелкосерийного производства, потому что скорость не очень высокая. Метод используют для получения витков на ходовых винтах, валах червяного типа. Преимущества – простота, достойное качество, высокая точность.
Метчиками и плашками
Плашка – это округлый или раздвижной (клупповый) режущий рабочий инструмент, отличающийся плавным заходом и располагающейся внутри резьбой. Стандартный элемент имеет диаметр не более 5,2 см, применяется для формирования наружных резьб на изделиях, используемых в строительстве, ремонте, при монтаже. Раздвижные плашки способны обрабатывать заготовки более крупных размеров. Они состоят из двух фиксируемых в клуппе частей, которые при нарезании движутся друг к другу.
Если нужно получить внутреннюю резьбу, подойдёт метчик. Это стержень с канавками винтовой или прямой конфигурации, образующими режущие кромки. Такая конструкция позволяет не забивать инструмент выходящей стружкой. Метчики подбираются по резьбе (трубной, метрической), обычно применяются комплектами для последовательного, постепенного нарезания.
Накатывание
Накатку выполняют на резьбонакатных агрегатах либо на токарных универсальных, оснащаемых накатывающими роликами. Рабочий механизм – это либо ролики с держателем, либо трёхголовый инструмент.
Обрабатывающий элемент, проходя по поверхности, деформирует её, но не снимает слой, а вдавливает в определённых зонах. Заготовка фиксируется плашками и цилиндрическими роликами со сформированными на них рисками. Метод подходит для деталей небольших диаметров, позволяет достигать минимальных погрешностей.
Протягивание
Относится по технологии к резанию, проводится многозубчатыми инструментами – протяжками. Они осуществляют поступательные режущие движения, затрагивающие всю обрабатываемую зону. Такая операция часто внедряется в серийные, массовые производства. Протягивание подходит для обработки деталей как снаружи, так и внутри. Геометрия и габариты получаются точными. Но протяжки стоят довольно дорого, что повышает стоимость работ.
Особенности мехобработки металла
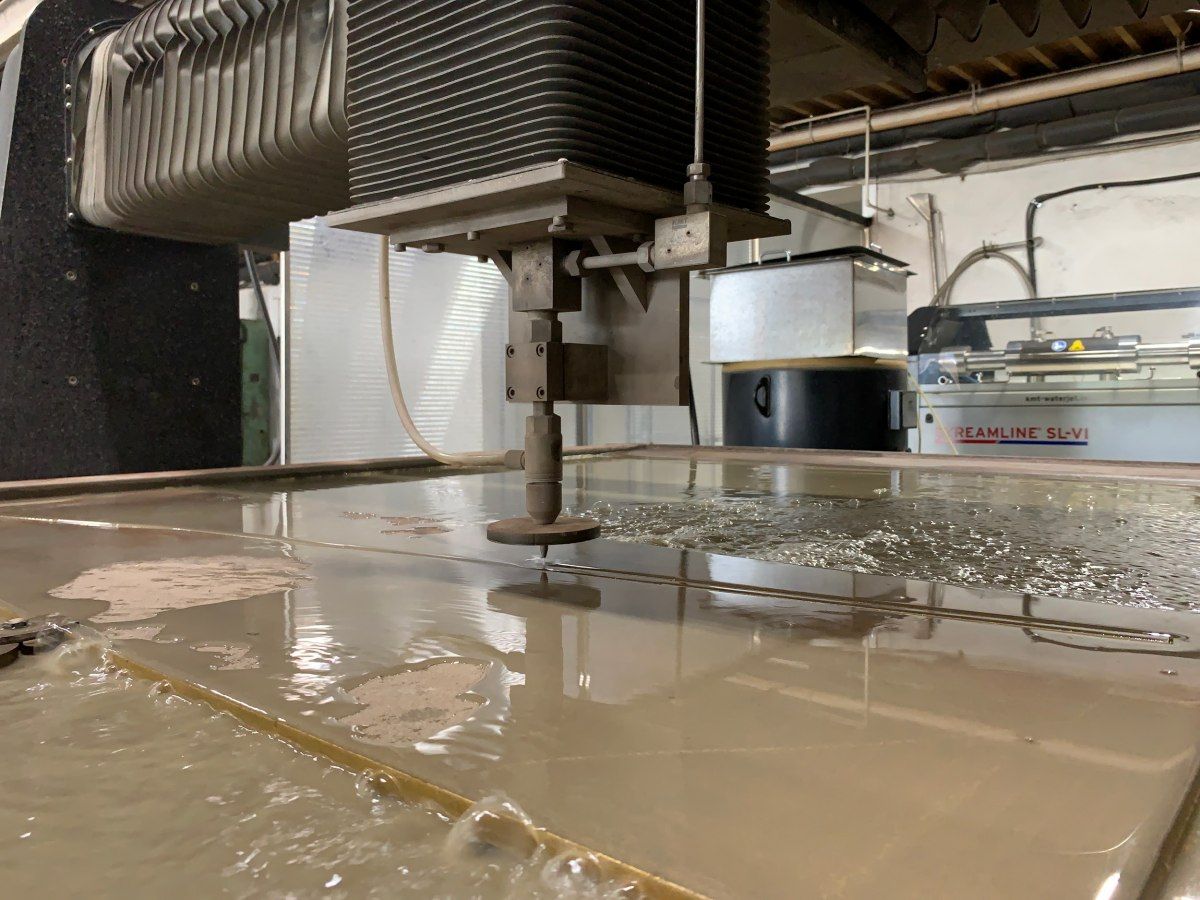
Главная задача воздействия, оказываемого извне, – изменить размер, геометрическую форму, текстуру поверхности. Но при этом исходное строение в основном объёме материала остаётся прежним, хотя в поверхностных слоях, на которые приходятся нагрузки, могут меняться физико-химические свойства. Это обусловливается пластической деформацией, которая искажает изначальную кристаллическую решётку, влияет на микроструктуру, а также придаёт кристаллическим зёрнам однородную ориентацию.
При пластических холодных деформациях увеличиваются предел прочности, плотность и твёрдость. Но пластичность при этом снижается. А при некоторых способах из-за высокоскоростного вращения рабочих инструментов, из-за интенсивного трения происходит значительный нагрев с последующим охлаждением. Это обусловливает протекающие в поверхностных слоях структурные превращения и фазовые.
После проведения технологических работ сплавы и металлы изменяют свои качественные, габаритные и конфигурационные характеристики, а иногда и химические, физические свойства. Коррекция поверхностных слоёв производится фрезами, резцами, шлифовальными дисками, сверлами. Механообработку выбирают для работ со многими металлоконструкциями, используемыми в промышленности, народном хозяйстве, быту, строительстве.
Результат – это появление новой, соответствующей установленным требованиям поверхности. Для этого исходные детали деформируются, их поверхностные слои убираются или отдаляются от основной части. Часто при операциях формируется стружка – побочный продукт. А отделяемый избыточный слой – это припуск. Когда его снимают, металлоизделие становится таким, каким должно быть в итоге.
Оборудование
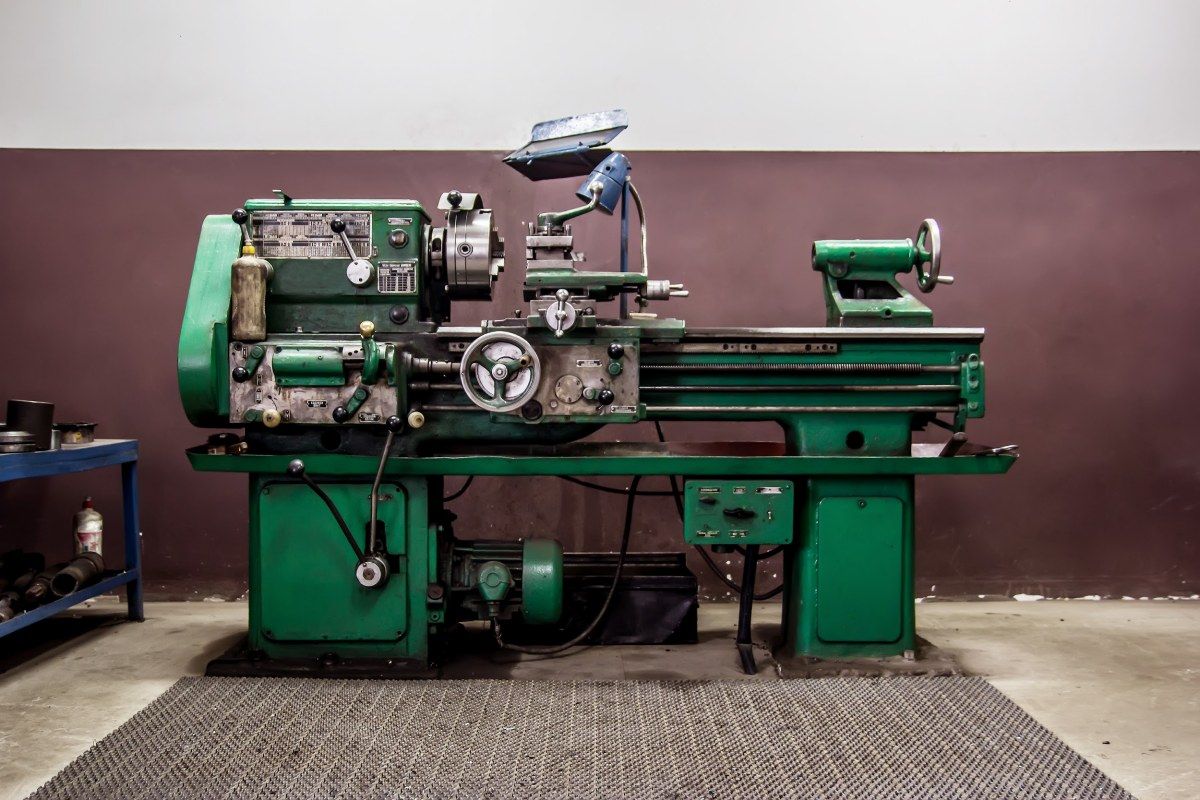
Для работ используют станки нескольких видов:
Это оборудование сегодня используется на всех металлообрабатывающих предприятиях. Заводы и фабрики постоянно модернизируют свои производства, внедряя автоматизированные линии. Современные станки оснащаются ЧПУ, поэтому, во-первых, ускоряют операции, во-вторых, минимизируют участие оператора, в-третьих, благодаря работе по заданным настройкам демонстрируют соответствие устанавливаемым параметрам и сокращают погрешности до минимума.
Термические методы
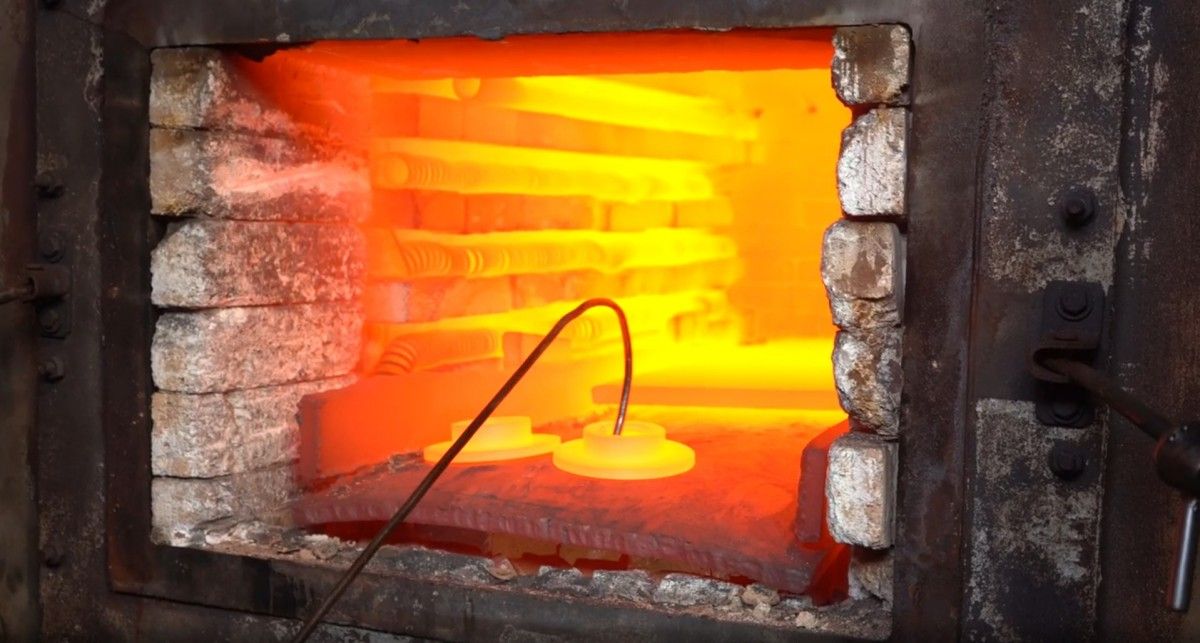
К механическим видам металлообработки относятся технологии, предполагающие термические воздействия, то есть нагревание до определённых повышенных температур. Такой подход, во-первых, необходим для усиления свойств пластичности. Раскалённое сырьё более податливое в ходе пластических деформаций с давлением, ударами.
Во-вторых, термообработка влияет на конечное качество изделий, адаптирует их к специфике использования. Металлы сохраняют свой химический состав, но становятся более прочными, износостойкими, устойчивыми к старению и нагрузкам. Такие эксплуатационные характеристики требуются во многих отраслях, например, в машиностроении.
Ковка
Разновидность механообработки, предполагающая термическое воздействие, – это ковка. При ней происходит пластическая деформация. В технологический процесс включен этап предварительного нагрева. Температурный режим подбирается индивидуально с учётом особенностей материала. Но значения всегда ниже температур плавления. На предварительно нагретую, иногда раскалённую деталь воздействуют механически.
Ковка имеет следующий пошаговый алгоритм:
Ручная ковка считается художественной и применяется для изготовления эксклюзивных изделий замысловатых форм, например, ограждений, аксессуаров для украшения интерьеров, мебели. Но на предприятиях используют оборудование, снабжаемое механическими молотами. По весу некоторые из них достигают 3-5 тонн: они используются для работ с объёмными, очень крупными деталями. Готовые кованые заготовки могут дополнительно свариваться, подвергаться рубке.
Современные методы механообработки металлоизделий
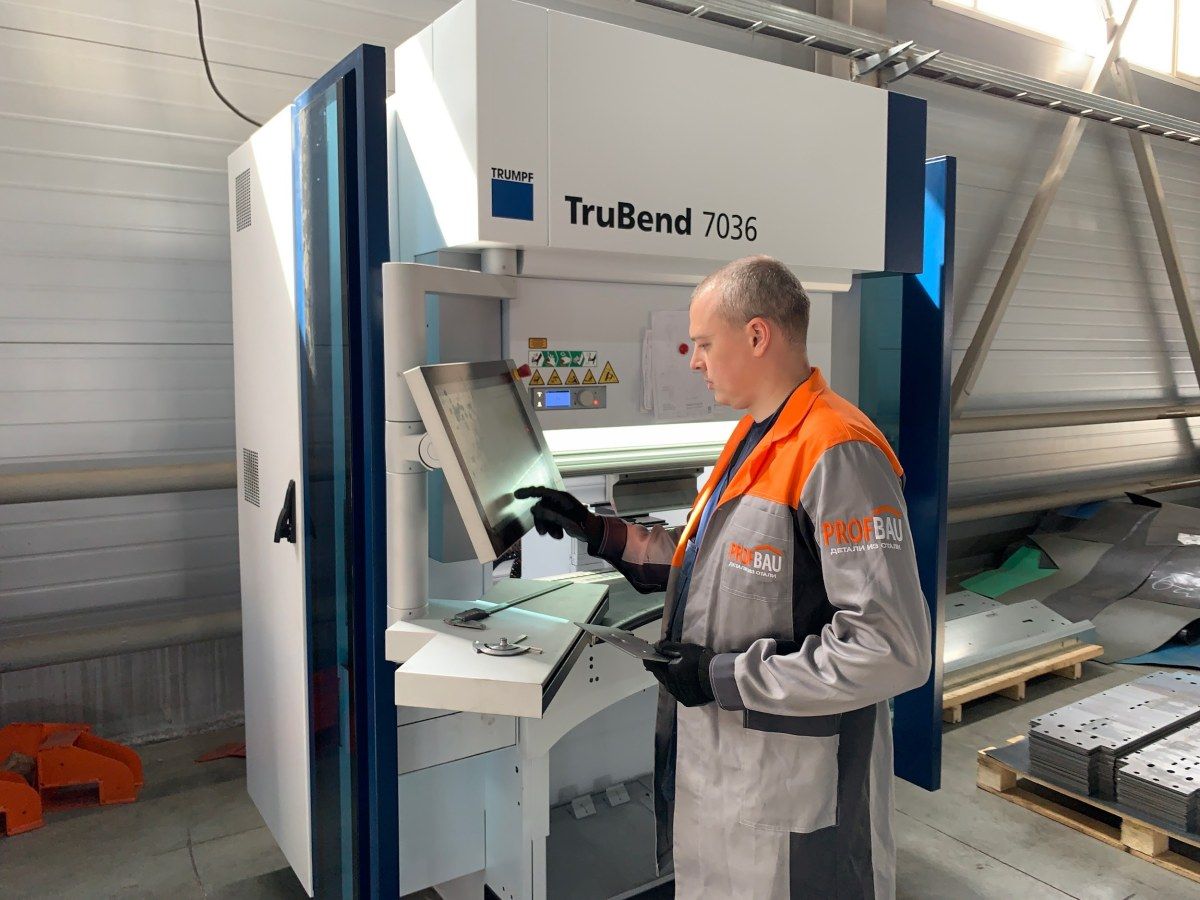
Наряду с классическими, стандартными методами, используются также современные. Они пока менее распространённые, но высокотехнологичные, высокоточные. Рассмотрим их ниже.
Ультразвук
Ультразвуковые волны с частотой 16-30 килогерц активируют действие абразивных мелких частиц, например, электрокорунда, карбида бора. Они разрушают тончайший слой материала, что позволяет работать с каналами, глухими отверстиями.
Электроэрозионная технология
Разрушение поверхностных слоёв в этом случае запускается мощными разрядами тока, возникающими между материалом и электродом. В зоне влияния повышается температура, выделяющаяся тепловая энергия буквально испаряет малые количества металлов, образуя эрозионные выемки. Метод подходит для отверстий разной сложности, для самых твёрдых материалов.
Абразивный способ
Такой метод предполагает повышение гладкости и применим для элементов механизмов с точными соединениями. Абразивные инструменты изготавливают из разных искусственных и природных материалов: кварца, корунда, натурального или синтетического алмаза, эльбора, электрокорунда. Воздействие осуществляется маленькими частицами (кристаллами), работающими, как резцы, которые снимают тонкие слои. Чтобы добиться нужных параметров, следует точно рассчитать величину абразивов.
В качестве обрабатывающих приспособлений используют листы, круги, сегменты с разной зернистостью: крупная подходит для грубого чернового воздействия, а мелкая – для финишного.
Этапы:
Гидроабразивный метод
Предполагается воздействие на поверхность направляемого под большим давлением водного потока с содержащимися в нём абразивными частицами. Текстура получается матовой, ровной, без рисок и других дефектов. Для ускорения процесса в воду добавляются специальные химические вещества.
Преимущества механической обработки
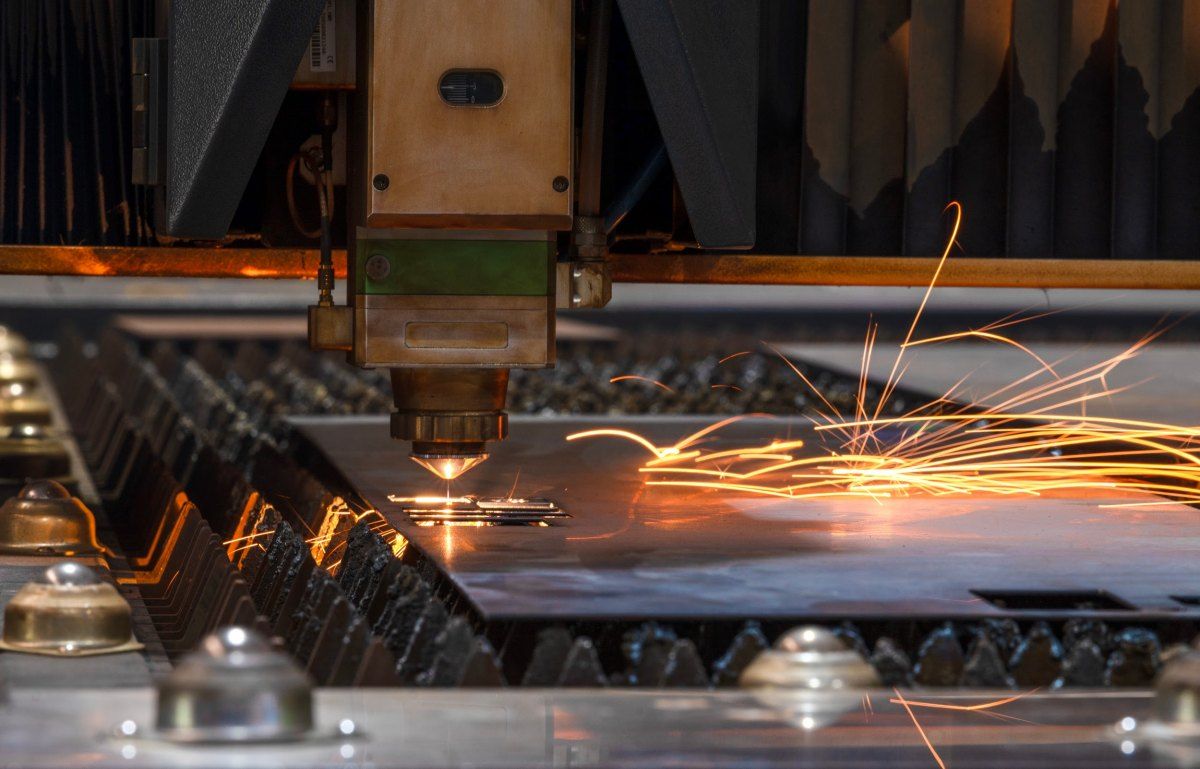
Плюсы:
Заключение
Механическую обработку стоит доверять только профессионалам. Компания Profbau выполняет работы качественно, оперативно, со строгим соблюдением стандартов, требований и пожеланий заказчиков.
Мы изготавливаем крупные, средние и мелкие партии, а также единичные образцы. Используем все существующие технологии, выполняем металлообработку на современном оборудовании. Узнать детали можно по телефону, в мессенджере, по электронной почте или с помощью формы обратной связи.