При производстве металлоизделий сначала делают заготовки, которым надо придавать заданные свойства. Для этого выполняют металлообработку. Один из её способов – резание. Оно позволяет получать детали с заданными габаритами, формами, фактурой. В этой статье расскажем, что представляет собой механическая обработка резанием: инструменты, применяемые для неё, методики.
Описание и назначение процесса
Обработка металлов резанием – сложный процесс. В основе – взаимодействие, в которое вступает рабочий инструмент и заготовка. Происходит динамический контакт материала с резцом, его острой кромкой. Наблюдаются определённые химические и физические изменения, результат которых – придание необходимых формы, размеров, рельефа или гладкости.
При операции возникают трение, деформации, выделяется тепловая энергия. С поверхности снимается тонкий слой, который разрушается, формирует стружку. Её фракция варьируется от достаточно крупной шихты до мельчайших частиц, образующих мелкодисперсную пыль.
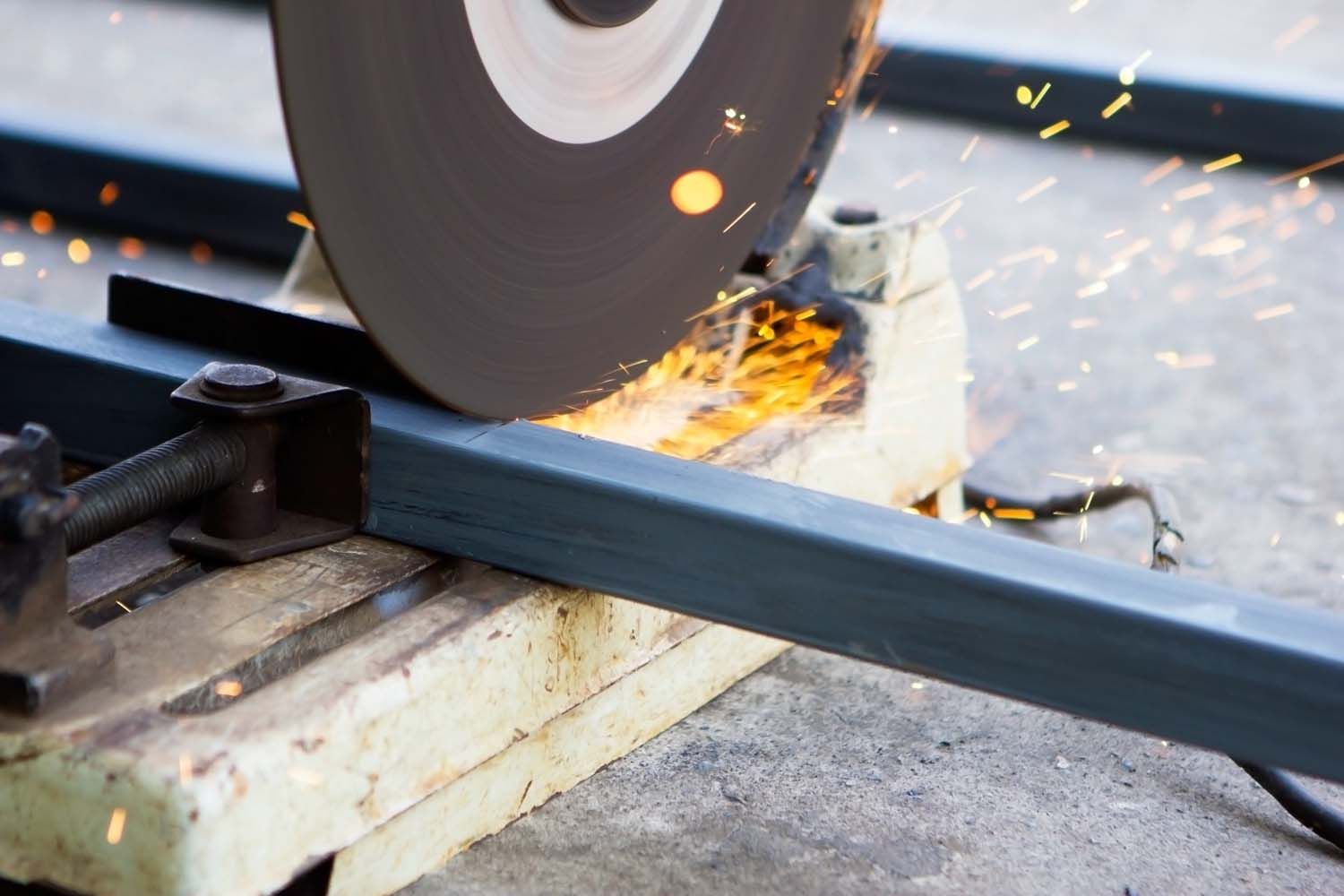
Методы обработки материалов резанием делятся на три группы:
- Лезвийные. Используют ручное и автоматизированное оборудование, которое оснащается имеющими острые кромки свёрлами, резцами, фрезами, плашками, метчиками.
- Абразивные. Применяют абразивы – материалы с зернистой структурой. В их состав входит кремний. Хотя по твёрдости он уступает некоторым другим веществам, но встречается повсеместно, недорого стоит. Оксид кремния имеет формулу SiO2 и является песком, который просто добывать и перерабатывать. При этом твёрдость высокая, что позволяет обрабатывать твёрдые виды сталей.
- Физико-химические. Основной метод – низкотемпературная плазма. Она доводится до температуры около 2000℃, воздействует локально, расплавляет участок, тем самым отрезает необходимый фрагмент. К физико-химическим способам относят также электролитическую, лазерную резку.
При любой технике материал претерпевает разрушение структуры. Оно локальное, в шовной зоне. Около кромок изменяются химические и физические свойства. Чтобы сохранять исходные характеристики, минимизируют количества разрезов.
Металл, который удаляется из шва, образует шихту либо стружку. Она бывает сливной, возникающей при разрезании материалов с высокой пластичностью, надломленной, формирующейся из охрупченных металлов, а также скалывающейся, образующейся из среднетвёрдых веществ и соединений. По стружке можно узнать некоторые параметры резки: её режим, способ, состав заготовки, тип и состояние оборудования, а также квалификацию мастера.
При составлении чертежей необходимо учитывать неизбежный расход материала. В габариты закладываются припуски с учётом удаляемой стружки. Исключение – разрезание гильотиной или ножницами, при котором расходование практически сведено к нулю.
Стружечные отходы – это потери, повышающие себестоимость полезного остатка. Пример: для изготовления одного немецкого танка «Королевский тигр» требовалось около 120 тонн металла. При этом конечная масса машины составляла не более 70 т.
Осуществляются движения:
- Установочные. Это фиксация заготовки, закрепление относительно неё обрабатывающего органа, а также позиционирование инструмента.
- Рабочие. Главным движением является снятие стружки. Также осуществляется подача – перемещение режущего инструмента по шву.
- Вспомогательные. Это корректировка размещения резцов.
Способы обработки металлов резанием
Все способы обработки металлов резанием предполагают нарушение их целостности, но преследуют разные цели. Ниже рассмотрим методы, используемые на производствах.
Точение
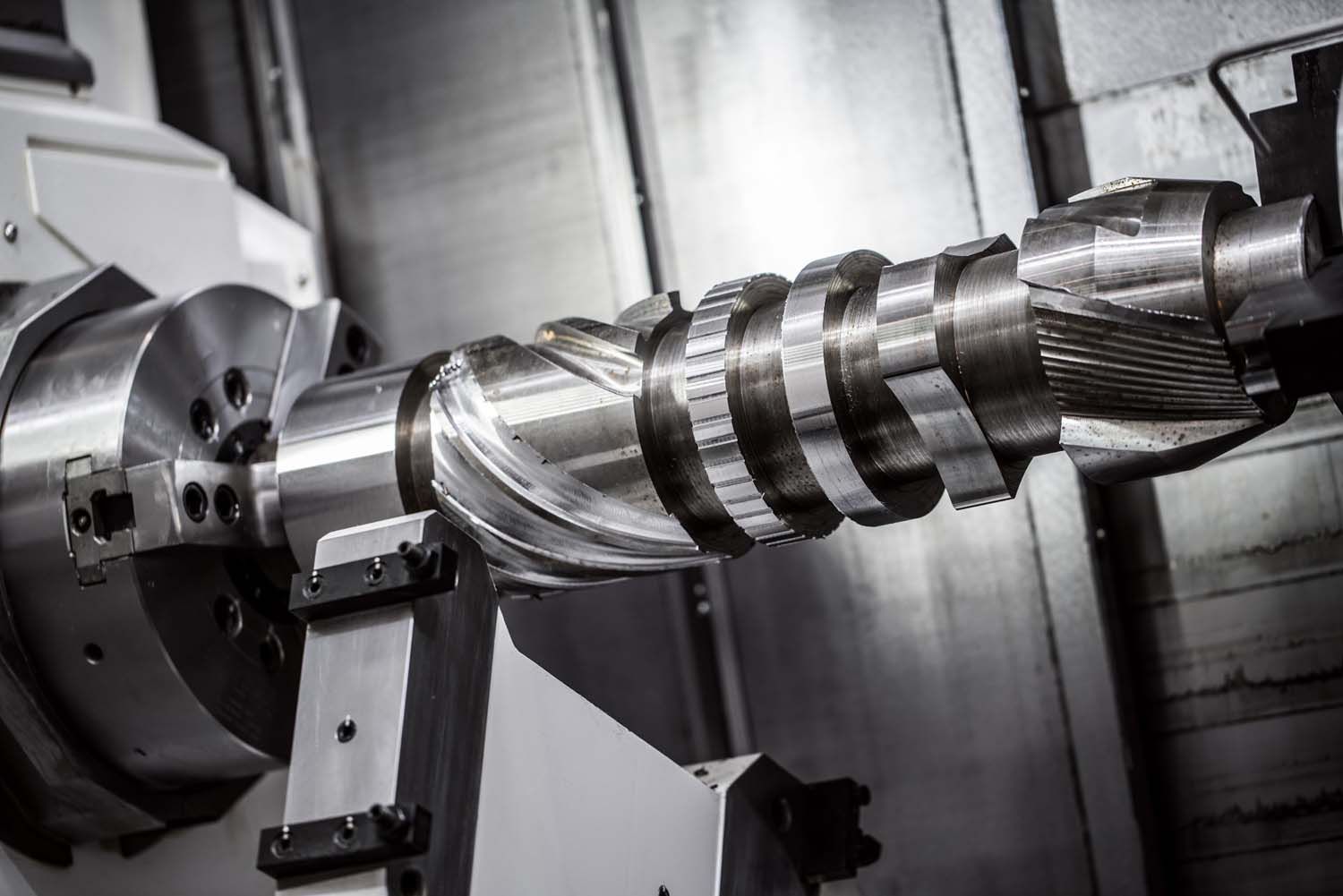
Для этой технологии обработки металлов резанием нужен токарный станок. В нём фиксируют тело вращения, например, втулку, муфту или иную деталь конической либо цилиндрической формы. Она с настроенной скоростью крутится вокруг своей оси, совершая главное движение. Одновременно перемещается резец, осуществляя движение подачи.
Но есть модификации токарных станков, в которых изделие сохраняет исходное положение, а рабочий инструмент вращается вокруг. Результат точения – идеальная торцевая часть, наружная или внутренняя цилиндрическая или коническая поверхность.
Сверление
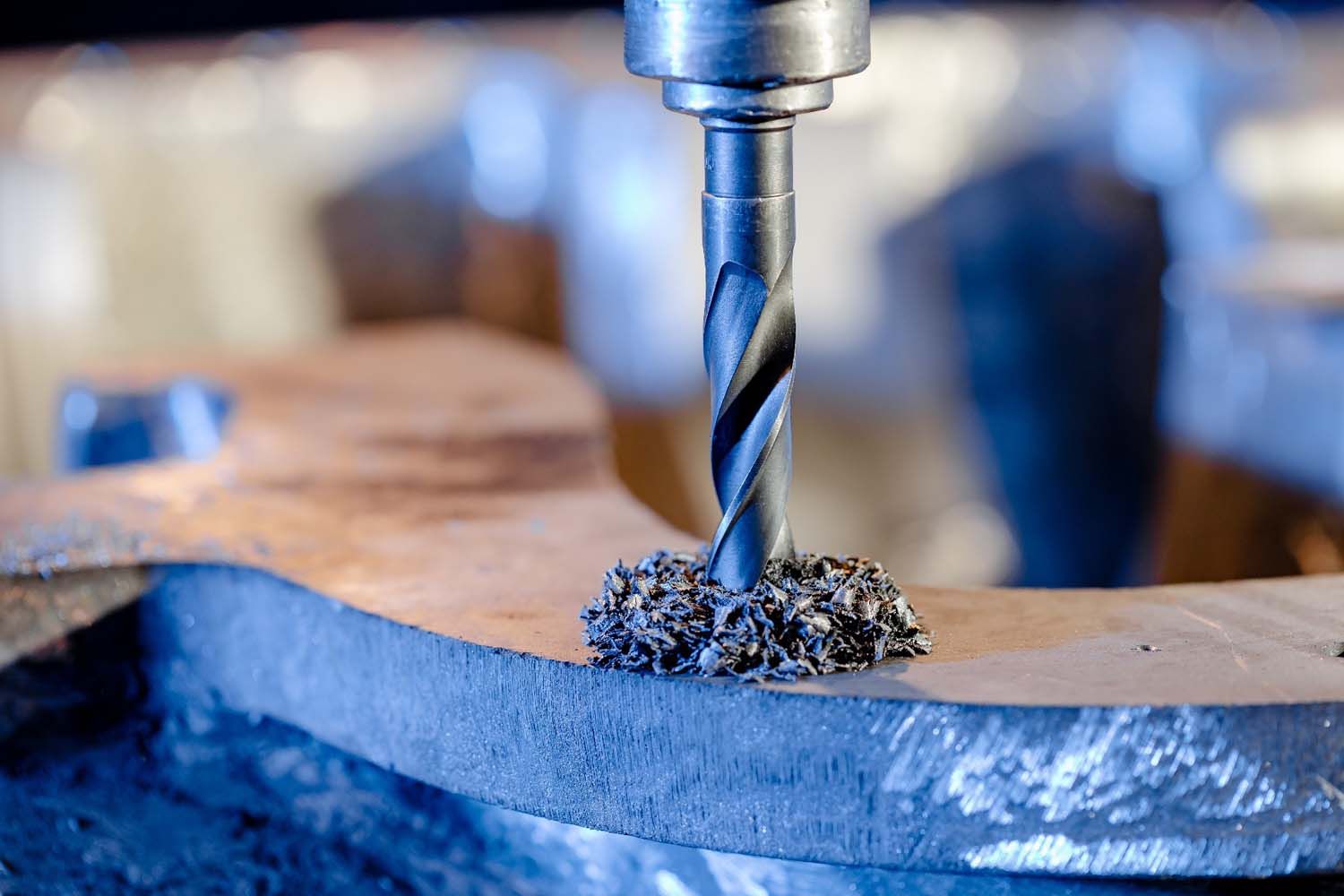
Если выполняется такая обработка резанием, режущий инструмент – сверло, которое устанавливается в сверлильном или многопрофильном токарном станке. Оно может быть перовым, центровочным, спиральным или совместимым с эксцентричными патронами. Но всегда острая кромка сверла находится на его торцевой части.
Задача сверления, которое выполняют мастера Profbau, – сформировать глухое либо сквозное отверстие, имеющее определённые глубину, диаметр, форму (например, цилиндрическую, коническую, треугольную или квадратную).
Фрезерование
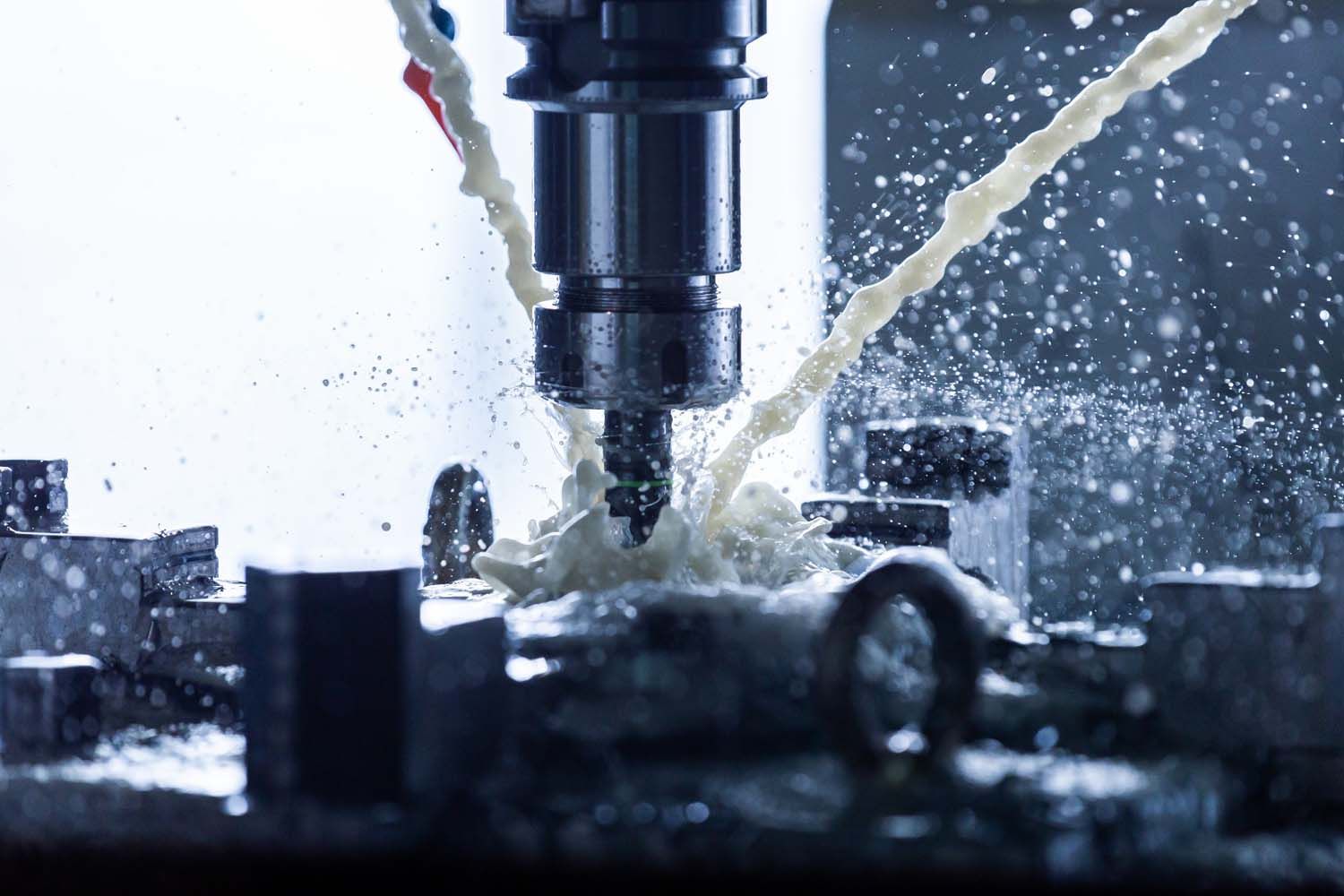
Фрезеровка может быть ручной или станочной. Но высокого качества можно добиться только на станке, так как заготовка должна занимать строгое положение, фиксироваться относительно движущегося инструмента. Это достигается с помощью станины.
Рабочий орган – это фреза, которая движется вращательно. Изделие перемещается продольно. Но на многофункциональном оборудовании фрезерование может реализовываться вертикально, горизонтально, диагонально. Профессиональную фрезерную обработку производит компания Profbau.
Строгание
Такая обработка заготовок и деталей резанием требует использования строгальных станков, которые бывают продольно-строгальными, строгально-долбёжными, поперечно-строгальными. На них изготавливают рамы, штанги, станины. Режущий инструмент – резец. Он бывает:
- Прямым. Использовать его удобно, но обработка может быть не самой точной.
- Изогнутым. Он стоит дёшево, демонстрирует хорошую точность, подходит для серийных производств.
Мы осуществляем строгание с учётом стандартов, требований заказчика.
Долбление
Этот процесс обработки резанием происходит на долбёжном станке, в котором рабочий орган перемещается возвратно-поступательно и прямолинейно, а изделие медленно движется относительно резца перпендикулярно либо по горизонтали. Такой способ позволяет создавать углубления с качественными краями. Другая область применения – производство зубчатых колёс.
Шлифование
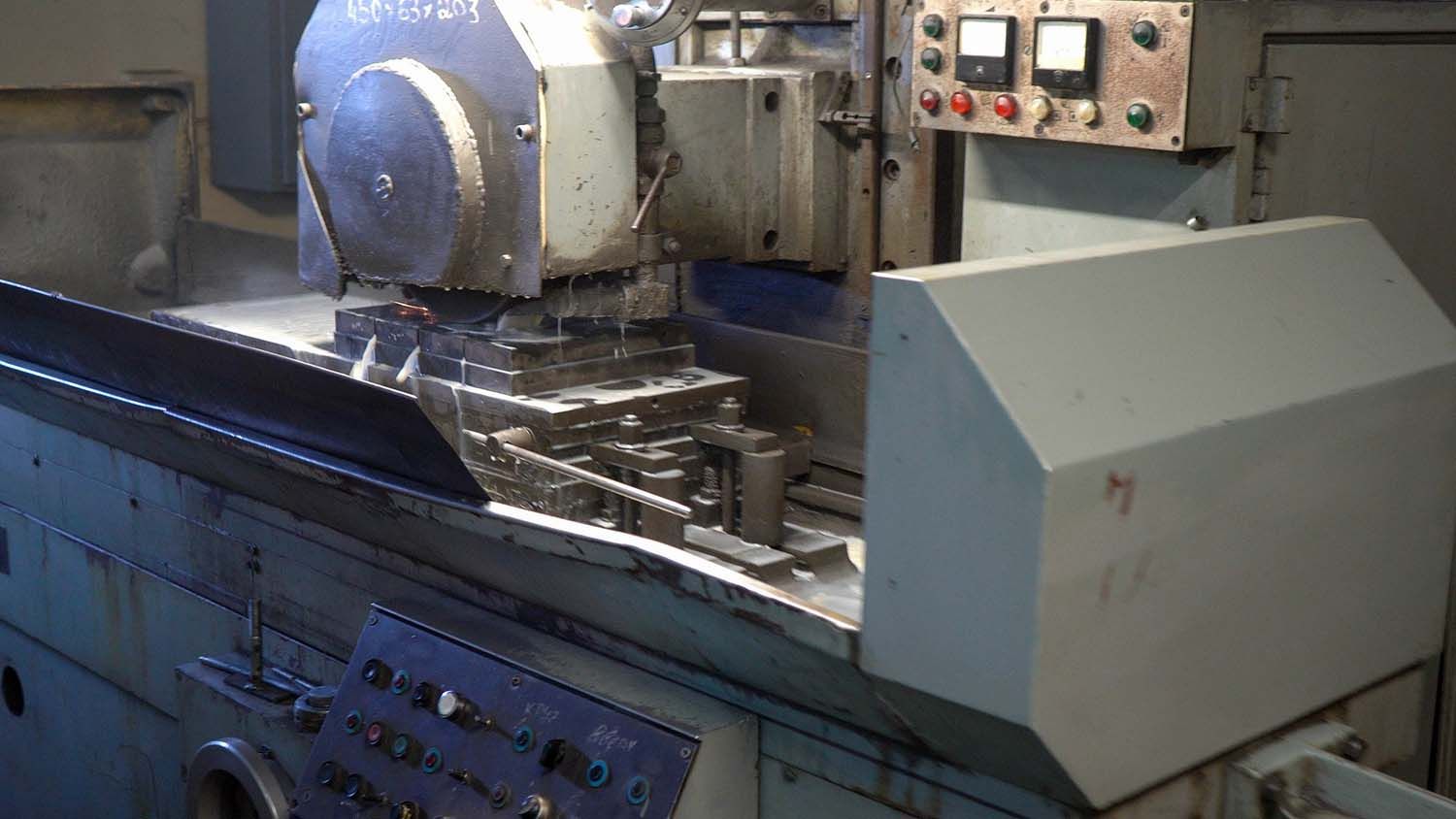
Применяется шлифовальный станок, снабжаемый кругом, который имеет абразивное покрытие и вращается вокруг собственной оси. Изделию задаётся подача продольно, которая иногда совмещается с поперечным ходом. Шлифованием, которое выполняют мастера Profbau, возможно обеспечить нужную степень гладкости, чистоты или шероховатости поверхности с точностью до долей миллиметра.
Но эта технологическая операция сопровождается вибрациями и нагреванием, которые обусловливают повышение расхода материала, требуют увеличения припусков, а в некоторых случаях локально меняют химические и физические свойства.
Лазерная резка
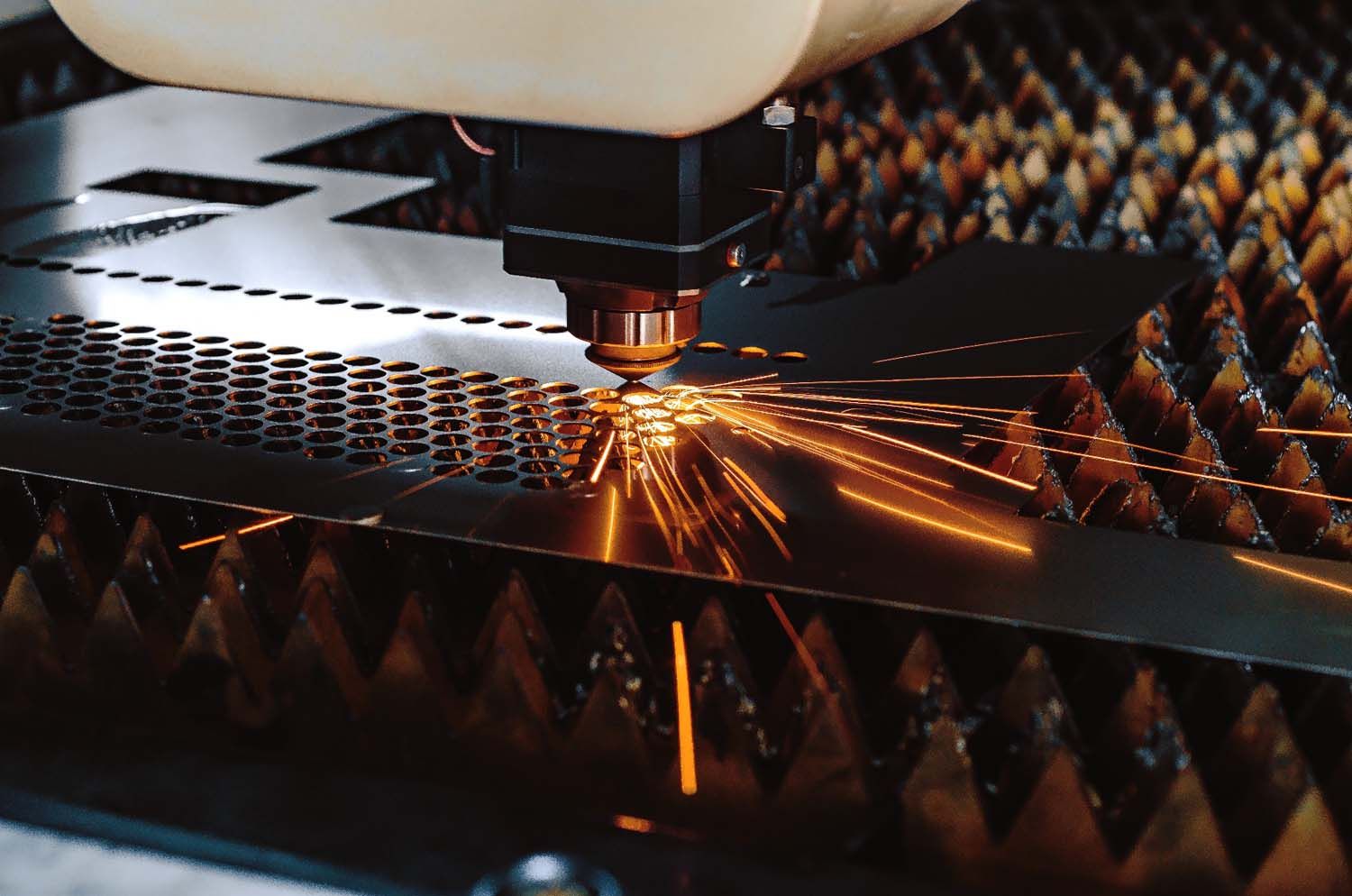
Рассматривая высокотехнологичные виды обработки резанием, стоит упомянуть лазерную технологию, которую мы используем для стали разных марок, бронзы и прочих цветных металлов. Она предполагает не механическое воздействие, а локальное термическое. Его оказывает сфокусированный на небольшой площади мощный луч лазера, синтезирующий энергию высокой плотности. Она разрушает металл, расплавляет его, что вызывает испарение или сгорание.
Лазерная технология высокоточная и производительная, но затратная из-за значительного энергопотребления. Также она подходит только для тонкостенных заготовок. Но существует газолазерная резка с плавлением. При ней в обрабатываемую область подаются газы, например, азот, кислород. Это уменьшает расход электричества, повышает скорость работ, а также увеличивает допустимую толщину изделий.
Плазменный метод
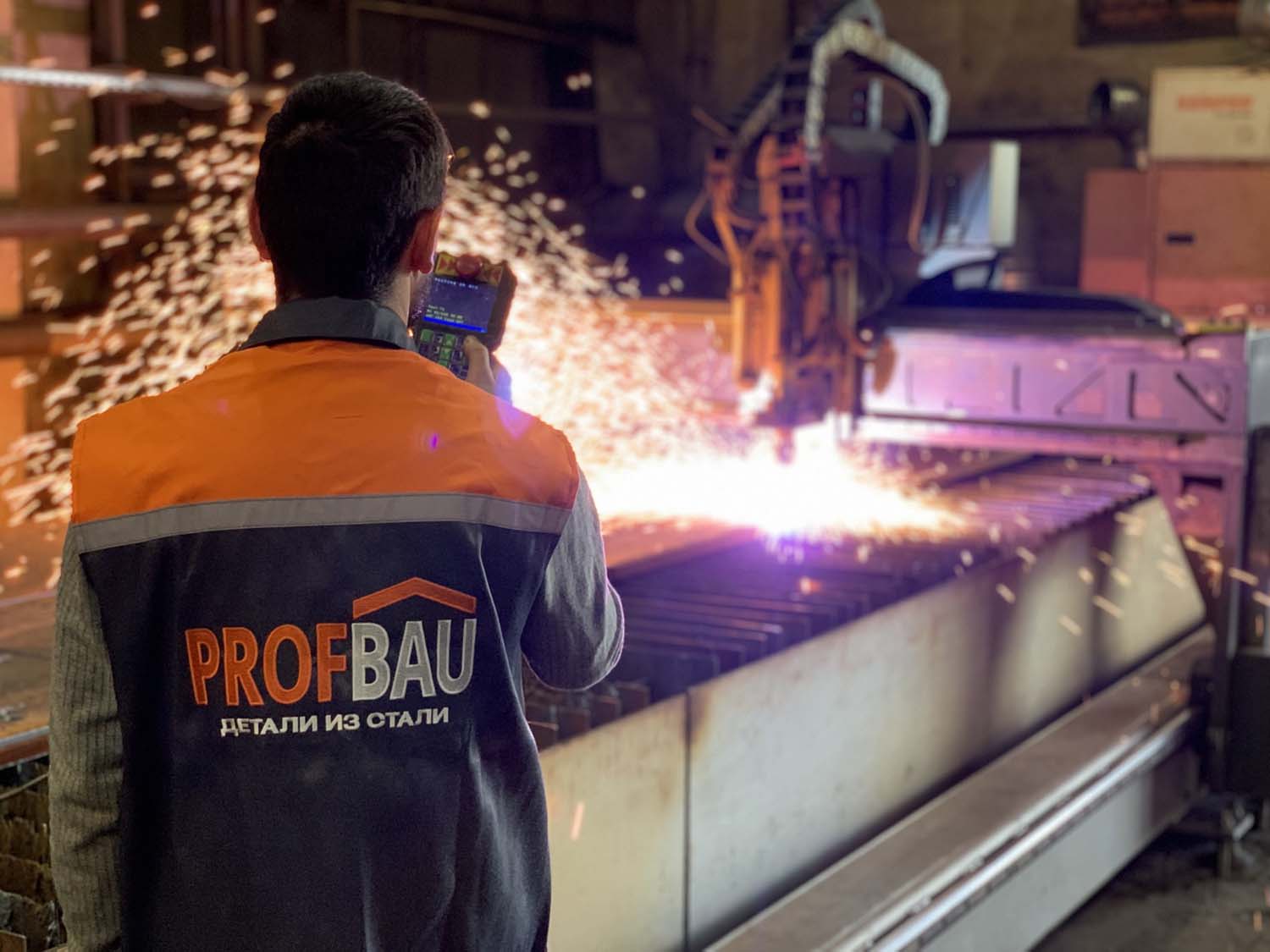
Плазменный способ совместим с чёрными и цветными металлами: чугуном, алюминием, медью, легированными и конструкционными сталями. Разрезание обеспечивает плазма – струя ионизированного газа.
Есть два метода:
- Плазменно-дуговой. Подходит для материалов с электропроводностью. Дуга плазмы с прямым действием образуется при прохождении электрического тока по электроду к заготовке. Металл расплавляется, быстро испаряется. Методика подходит для металлопроката не более 5 см в толщине. Срезы получаются точными, особенно на оборудовании с ЧПУ.
- С плазменной струёй. Этот вариант подходит для материалов, которые не проводят ток. Используется дуга косвенного действия, формирующаяся между соплом и катодом. То есть разрезаемое изделие не включается в электрическую цепь.
Электроэрозионный способ
Разрезание осуществляется путём горения электрической дуги, которая формируется между заготовкой и рабочим органом. Меняя окружающую среду, продолжительность импульсов и полярность заготовки, можно настраивать, контролировать разрушение. Электроэрозионным методом можно просверливать отверстия, разрезать металлопрокат проволокой, выполнять тонкое шлифование. Плюсы – отсутствие деформаций, высокая точность.
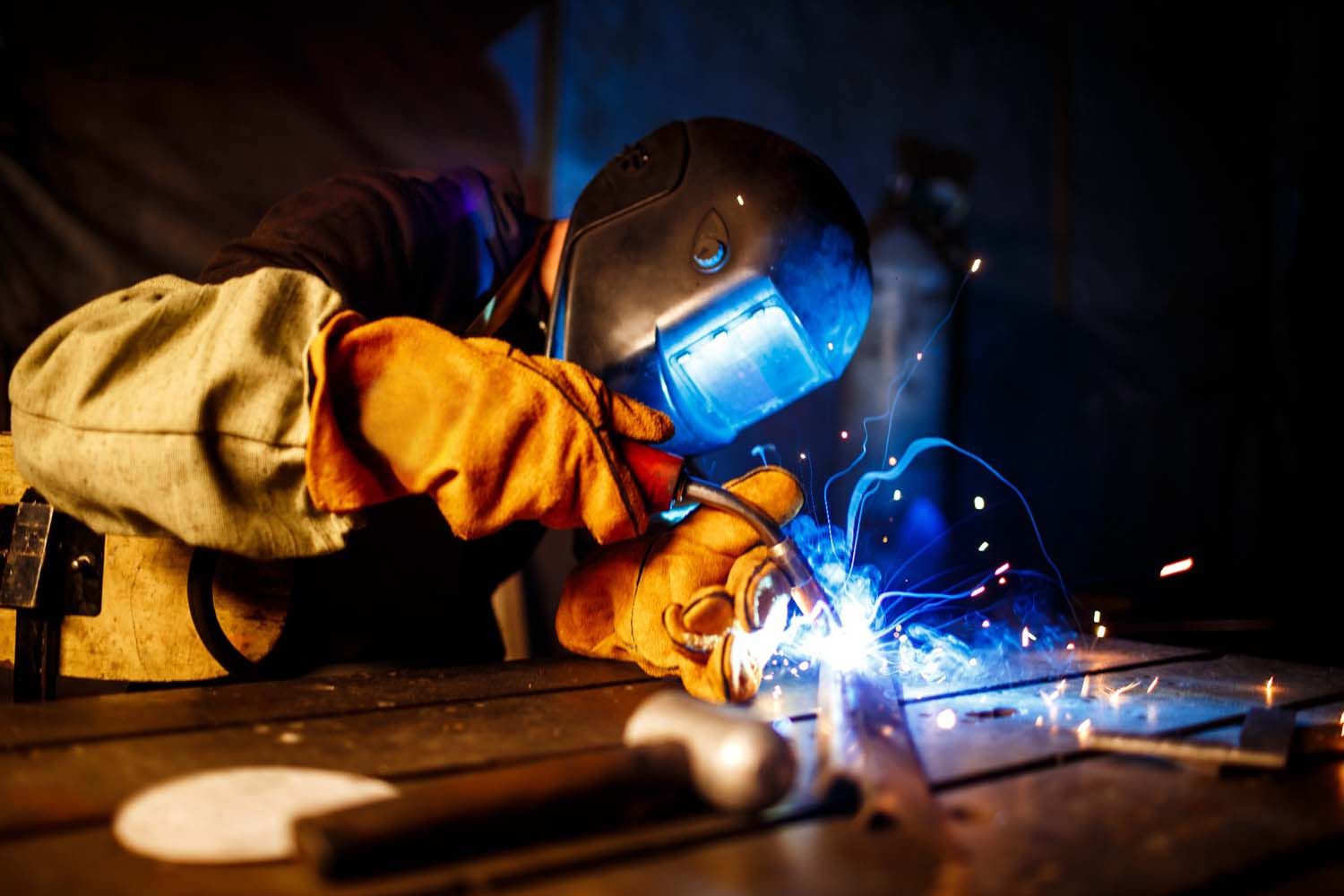
Необходимые инструменты
Применяются разнообразные инструменты, например, плашки, метчики, развёртки, свёрла, долбёжки, резцы, фасонные элементы. Подбор зависит от выполняемых работ, от характеристик заготовок, ожидаемых результатов. Есть универсальные инструменты, подходящие для широкого спектра операций, а также узкоспециализированные.
Технические характеристики режущих элементов влияют на качество и точность получаемых изделий, на сроки их службы, на производительность труда. Рабочая поверхность должна быть износостойкой, прочной, а также поддающейся периодическому затачиванию, выдерживающей нагревание.
Чаще применяют резцы. Их задняя и передняя поверхности пересекаются с формированием главного лезвия и вспомогательного. В точке пересечения последних находится вершина режущей зоны. Поперечное сечение лезвия клиновидное.
Для производства рабочих инструментов применяют металлы с высокой прочностью, термостойкостью, устойчивостью к деформациям и механическому износу, с повышенной твёрдостью. Обычно это быстрорежущие стали, а также другие составы типа керметов, минералокерамических сплавов, металлокерамики, синтетических алмазов. Для увеличения прочности используют покрытия из нитрида, борида, ниобия, карбида титана.
Оборудование
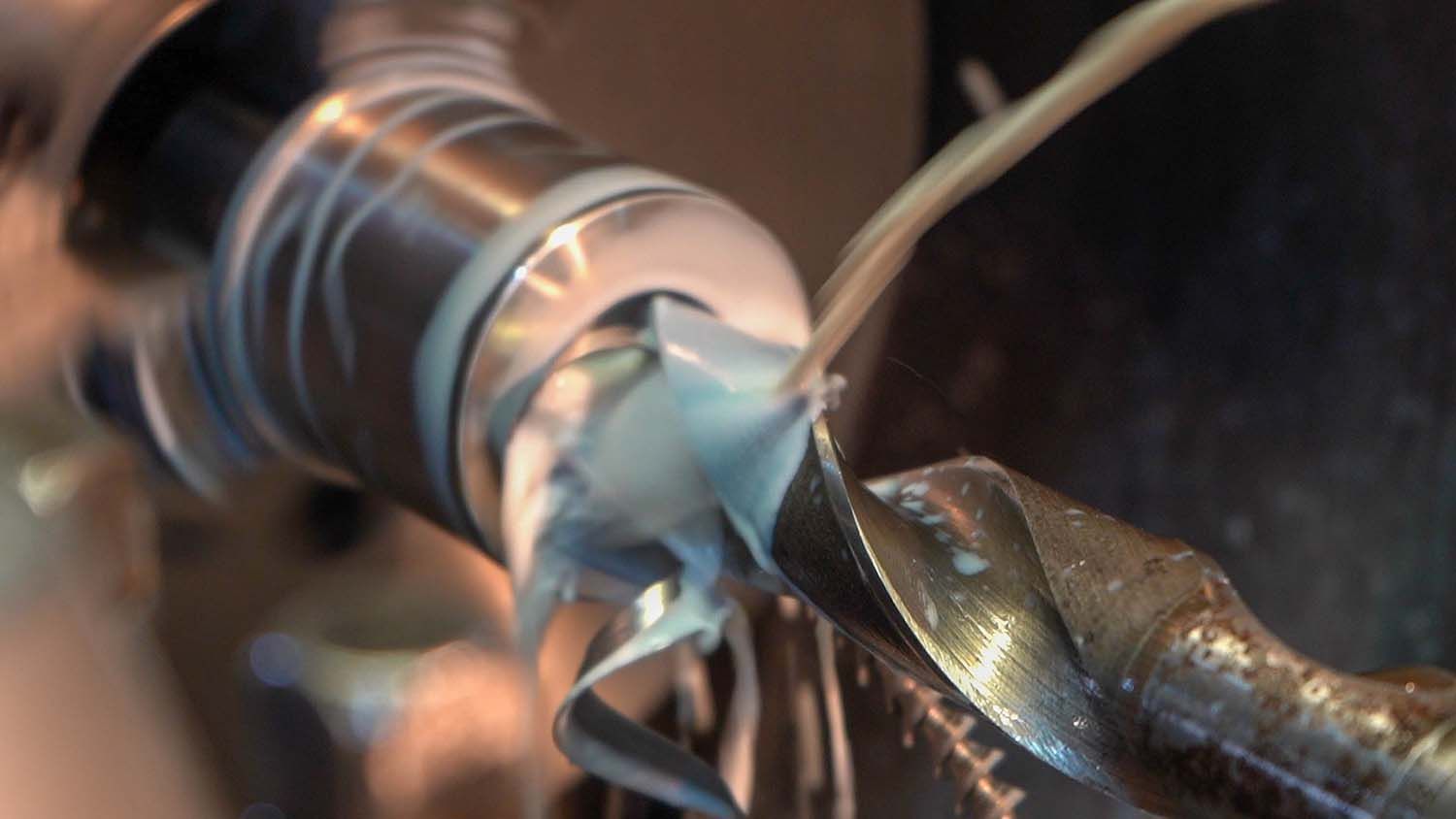
Обработка резанием стали или других материалов выполняется на разных станках. Рассмотрим их виды:
- Токарные. Они применимы для конических, цилиндрических, сферических, фасонных заготовок. Последние крепятся на патроне, который находится на шпинделе. Одновременно с вращением изделия инструмент движется поступательно в поперечном и продольном направлениях.
- Сверлильные. Они оснащаются зенкерами, свёрлами, развёртками. Такие рабочие органы быстро вращаются и продвигаются в зафиксированную заготовку, формируя в ней отверстие или углубление. Также на сверлильных станках можно выполнять зенкерование, цекование, зенкование, нарезание резьбы, развёртывание, рассверливание.
- Фрезерные. На них создают канавки, выступы, зубцы, пазы, резьбы внутри или снаружи. Также возможно обтачивание. Станки этого типа бывают вертикально-, продольно- и горизонтально-фрезерными. Закреплённая в шпинделе фреза движется вращательно и поступательно, воздействуя на материал, а также частично, локально удаляя его.
- Точильные. На них осуществляется точение путём поступательно-вращательного движения рабочего органа.
- Шлифовальные. В них устанавливаются специальные абразивные круги, которые, крутясь и контактируя с заготовкой, снимают её поверхностные тонкие слои.
- Строгальные. Строгальная головка поверхностно, линейно удаляет материал для достижения ровности, гладкости.
- Долбёжные. Такие станки применяют для обработки труднодоступных наружных и внутренних поверхностей, прямых, наклонных участков. Они создают канавки, углубления, фасонные поверхности, пазы различных профилей.
Режимы для обработки металлов резанием
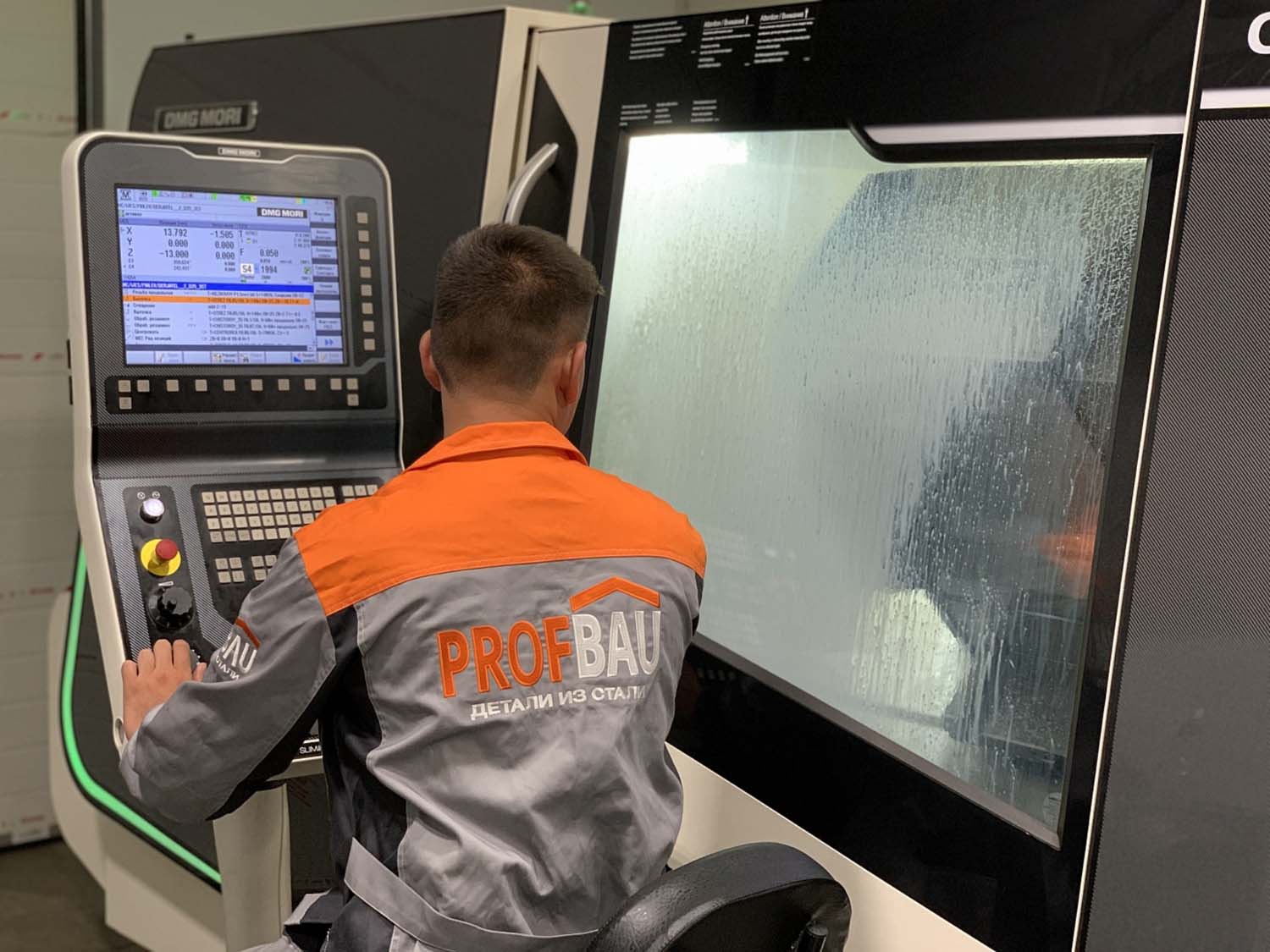
Режимы обработки резанием – это настройки, задающие конечные параметры. От их выбора зависит итоговое качество изделия, его соответствие чертежу, ГОСТ, требованиям. Режим представляет собой комплексное решение, которое разрабатывается с учётом следующих факторов:
- состояние, исправность оснастки;
- производительность агрегата;
- тип заготовки;
- состав, структура, свойства материала.
Предусмотрены усилия двух видов. Первое – вращение заготовки. Второе – движение (главное и подачи) рабочего органа. От таких усилий зависят технологические показателя станка, а именно совершаемые шпинделем обороты, глубина реза (толщина удаляемого слоя), скорость обработки.
Зачастую при металлообработке возможно минимизировать затраты, сокращая количество времени и объём образующейся стружки. Экономичность технологических процессов зависит во многом от режима. Он влияет на:
- производительность станка: среднюю и общую;
- износ;
- качественные производственные показатели;
- стойкость инструмента;
- себестоимость обрабатываемых изделий, их конечную цену;
- технику безопасности, соблюдаемую на производстве.
Некорректно подобранный режим может ускорить износ инструментов и главных узлов, спровоцировать поломки, повысить расход материала, вызвать разбалансировку вала и приводов, привести к появлению сколов и трещин на деталях.
Основные параметры при обработке
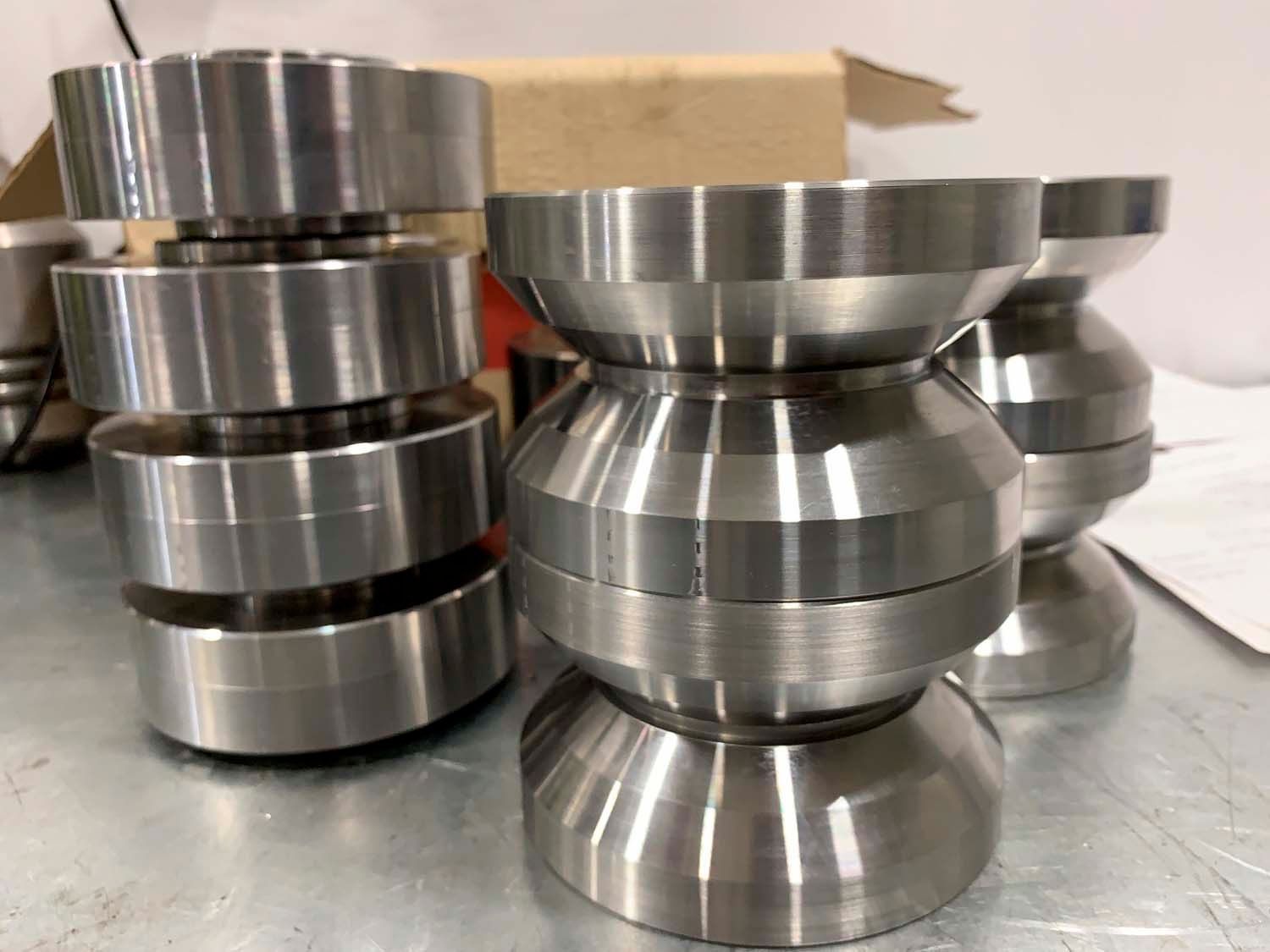
Технология обработки резанием предполагает настройку и соблюдение определённых параметров, задающих тип, направление и скорость движения резцов, от которых зависят конечные характеристики заготовки. Затронем главные моменты.
Глубина резания
Глубиной является срезаемый слой материала. Часто удаление производится послойно, в несколько проходов. При этом на каждом этапе снимается слой строго заданной толщины. Она в профессиональной механообработке имеет обозначение t. Именно это – глубина резания, которая составляет ½ разности диаметров до обработки и после её завершения. Расчёт выполняется по формуле: t = (D – d)/2, где латинская t – это искомая величина, D – начальный диаметр изделия, а d – диаметр, который нужно получить.
Подача при обработке резанием
Подача представляет собой скорость, с которой движется рабочий инструмент относительно детали. Это путь, который резец или фреза проделывает за оборот шпинделя. Для измерения используются специальные единицы – мм/об (то есть миллиметры за оборот).
Скорость подачи определяется по специализированным справочникам. На неё влияют износ подшипников, точность передачи, мощность силового узла агрегата, свойства материала. Для расчёта обычно применяют формулу: S = (0,05…0,25)*t. Здесь t – это упомянутая выше глубина.
Чем больше подача, тем выше производительность. Но при этом ускоряется износ. Кроме того, снижается качество. Обычно максимальная подача выбирается для черновой металлообработки.
Скорость резания
Скорость резания при обработке представляет собой суммарный путь кромки инструмента за определённый временной промежуток. Такой показатель является комплексным, потому что в данном случае учитывается глубина резания.
Единицы измерения – м/мин, то есть метры в минуту. Обозначение – буква v. Для вычисления проводятся последовательные расчёты. Сначала выясняется t, далее с помощью справочной информации подбирается S. Потом в таблицах ищут значение vт, находят vут с учётом корректировочных коэффициентов, а затем выбирают фактический параметр vф, беря во внимание скорость, с которой крутится главный вал.
Значение v определяет производительность агрегата, а также допустимые эксплуатационные режимы, интенсивность износа, конечное качество заготовок.
Выбор способа и режима при резании
При подборе способа следует учитывать:
- возможность получения чистых срезов без деформаций, без остаточных следов;
- оптимальное соотношение скорости и конечного качества;
- параметры резки: фигурная, со сложным профилем, простая;
- экономия при раскрое;
- простота управления процессом, настроек;
- возможность работы с разными толщинами, а также с загрязнёнными поверхностями;
- допустимость комплексной металлообработки – совмещения с другими операциями, такими как снятие фаски.
Режим подбирается либо технологическим отделом металлообрабатывающего завода, либо отдельным специалистом – главным технологом. Он подготавливает операционную карту с рекомендациями, последовательностью работ, указанием подходящих инструментов и режимов. По такому документу подбирается оснастка. Но возможны проблемы из-за непредвиденных отклонений исходных габаритов заготовок, несоответствия свойств материала расчетным параметрам, из-за сильного износа станков. В таких случаях вносятся корректировки с промежуточным контролем качества.
При подборе режима могут выполняться контрольные проходы. Но такой подход не оправдан при обработке бракованных, уникальных изделий, а также выполненных из малоизвестных материалов.
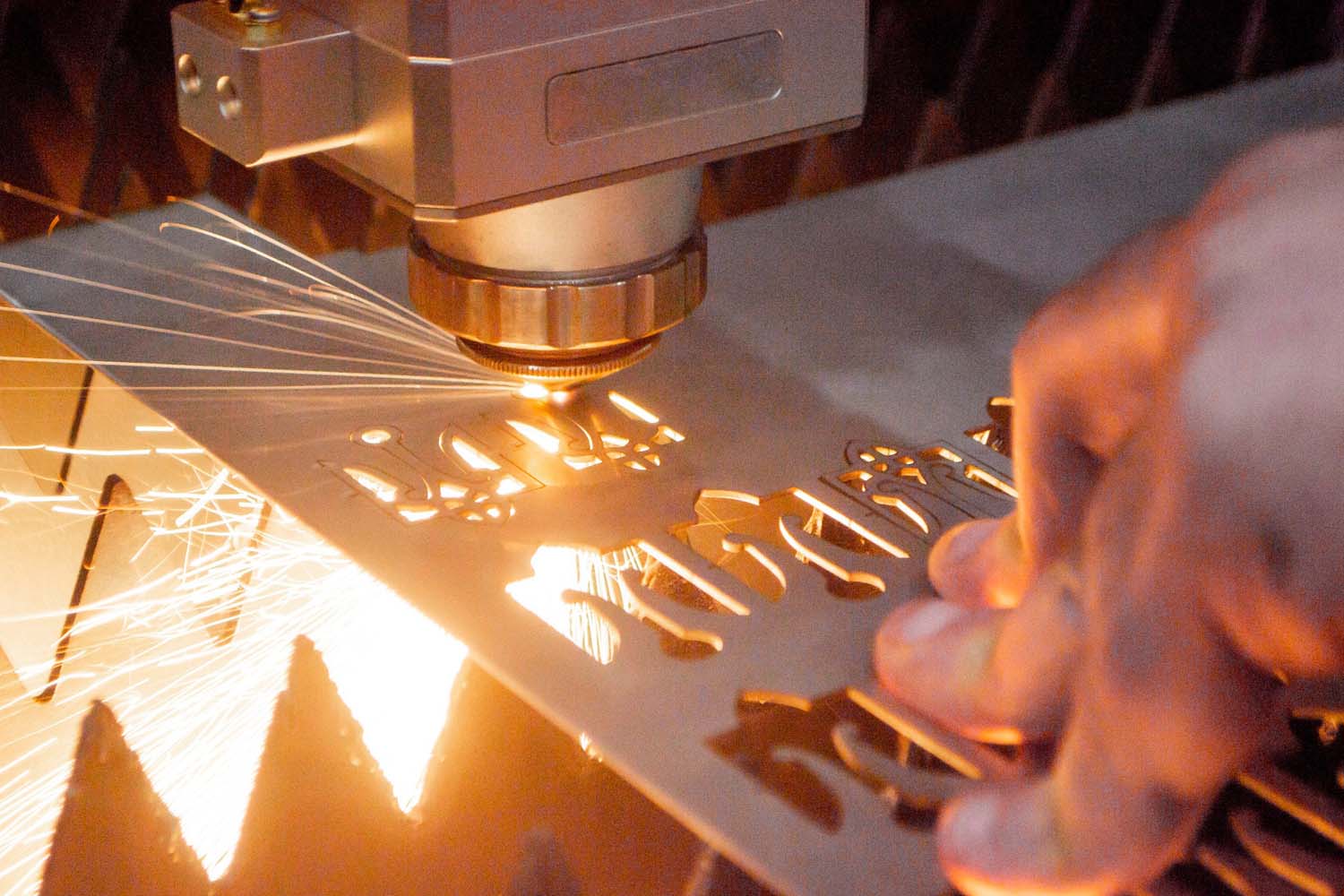
Заключение
Компания Profbau применяет разные технологии обработки металлов резанием, использует современное оборудование и работает в соответствии с действующими стандартами, чертежами и требованиями клиентов. Это позволяет резать различные металлы точно и оперативно, добиваться высокой точности геометрии и габаритов изделий, а также минимизации отходов.
Обратитесь к нам по электронной почте zakaz@profbau.ru, по телефону +7 (495) 138-25-25, в мессенджере или онлайн-чате. Также можно оставить заявку на сайте.