Резьба в отверстии обеспечивает надёжное соединение двух деталей или элементов металлоконструкции. Такое крепление часто используют в машиностроении, при производстве мебели, бытовой техники и других изделий. В статье расскажем, как правильно делать резьбу, что для этого нужно.
Важные параметры резьбы
Резьба, сформированная в отверстии, считается внутренней. Она представляет собой чередование впадин и выступов, которые располагаются по винтовой линии. Формируется такая поверхность при перемещении плоского профиля по коническому элементу или цилиндрическому. Это главная составляющая каждого резьбового соединения, а также часть зубчато-винтовых и винтовых передач. Крепления бывают шпилечными и болтовыми. Шпильки дополняются шайбами и гайками.
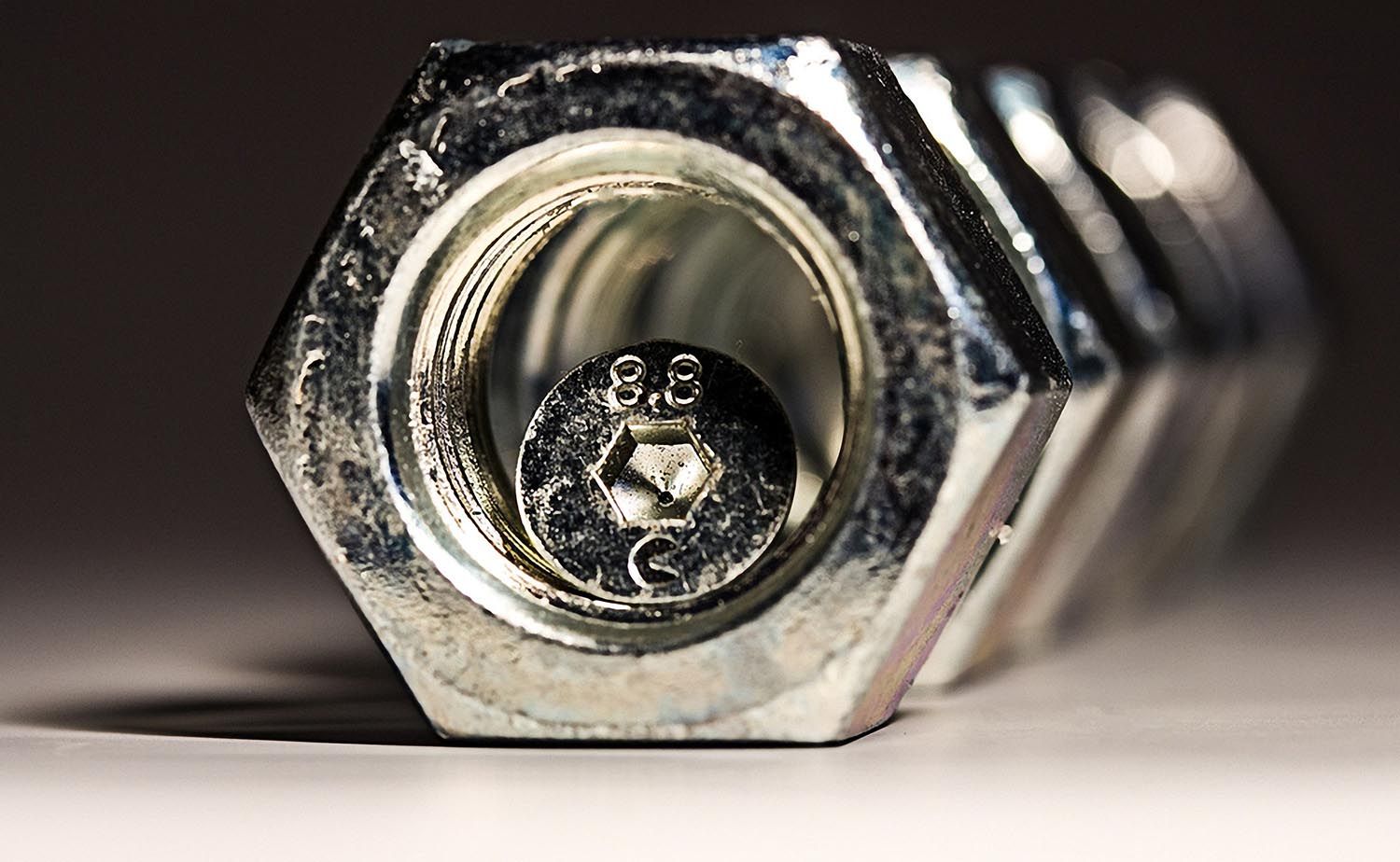
Все резьбы различаются по нескольким параметрам:
- Назначение. По нему выделяют крепёжные резьбы, ходовые и крепёжно-уплотнительные. Первые скрепляют между собой детали. Им свойственно самостоятельное торможение, которое не даёт соединениям ослабляться под действием нагрузок. Крепёжно-уплотнительные не только фиксируют, но и герметизируют участки соединений, например, в запорных арматурах и трубопроводах, чтобы газы и жидкости не могли просачиваться. Ходовые резьбы передают движение.
- Профиль. Он является контуром сечения в плоскости, которая проходит через осевую часть имеющей резьбу заготовки. Профиль имеет определённый угол наклона сторон, выступ и впадину, которая бывает с закруглением и плоско срезанной. По этому параметру резьбы делятся на трапецеидальные, треугольные, упорные, прямоугольные, нестандартные специальные. Для метрических цилиндрических резьб, которые по диаметру меньше 600 миллиметров, действуют ГОСТ, регламентирующие номинальный единый профиль.
- Диаметр: внутренний, средний, наружный. Внутренний характеризует воображаемый цилиндр, по границам совпадающий с резьбовыми вершинами, то есть выступающими частями. Наружный показывает размер цилиндрической фигуры, описывающий впадины, то есть углубления. А диаметр средний относится к вымышленному цилиндру, в поверхности пересекающему резьбовые витки так, что по ширине они аналогичны впадинам.
- Единица измерения, действующая для определения диаметра. Метрические резьбы измеряются в привычных для многих миллиметрах, для дюймовых действуют дюймы. Также есть модульная разновидность, которую мерят в модулях. Если умножить их на число Пи, то можно перевести диаметр в миллиметры. Существуют и питчевые резьбы. Один питч можно перевести в дюйм, разделив на него число Пи. Последние два вида характерны для червяков, применяемых в червячных передачах.
- Шаг. Это длина проложенного вдоль резьбовой оси отрезка между смежными двумя витками.
- Направление проложенной винтовой линии. Оно может быть левым или правым.
- Образующая: коническая либо цилиндрическая, в зависимости от конфигурации отверстия (цилиндр, конус).
- Количество заходов. Есть резьбы однозаходные и многозаходные. В последних заходов несколько – два, три, четыре или больше.
- Ход. Это расстояние отрезка линии, проходящей параллельно оси, между точкой исходной и второй, находящейся в участке завершения поворота на 360 градусов.
- Рабочая высота одного витка – наибольшая и наименьшая высоты соприкосновения.
- Глубина. Она является высотой каждого выступа – расстоянием между основанием и вершиной. Глубина определяется с учётом размера фаски, глубины, на которую осуществляется вкручивание, недореза, а также запаса внешней резьбовой поверхности шпильки либо болта. Недорезы, величины фасок, запасы – всё это рассматривается в справочниках и обучающих пособиях. А глубина ввинчивания рассчитывается по коэффициентам, различающимся для разных металлов и сплавов. Так, для ковкого и серого чугуна это 1,25, для латуни, титана, стали, бронзы – 1, а для сплавов из категории лёгких – 2.
Важно! Резьба отверстия должна соответствовать параметрам вкручиваемого элемента, чтобы все впадины и выступы совпали. Любые неточности влияют на надёжность, качество соединения.
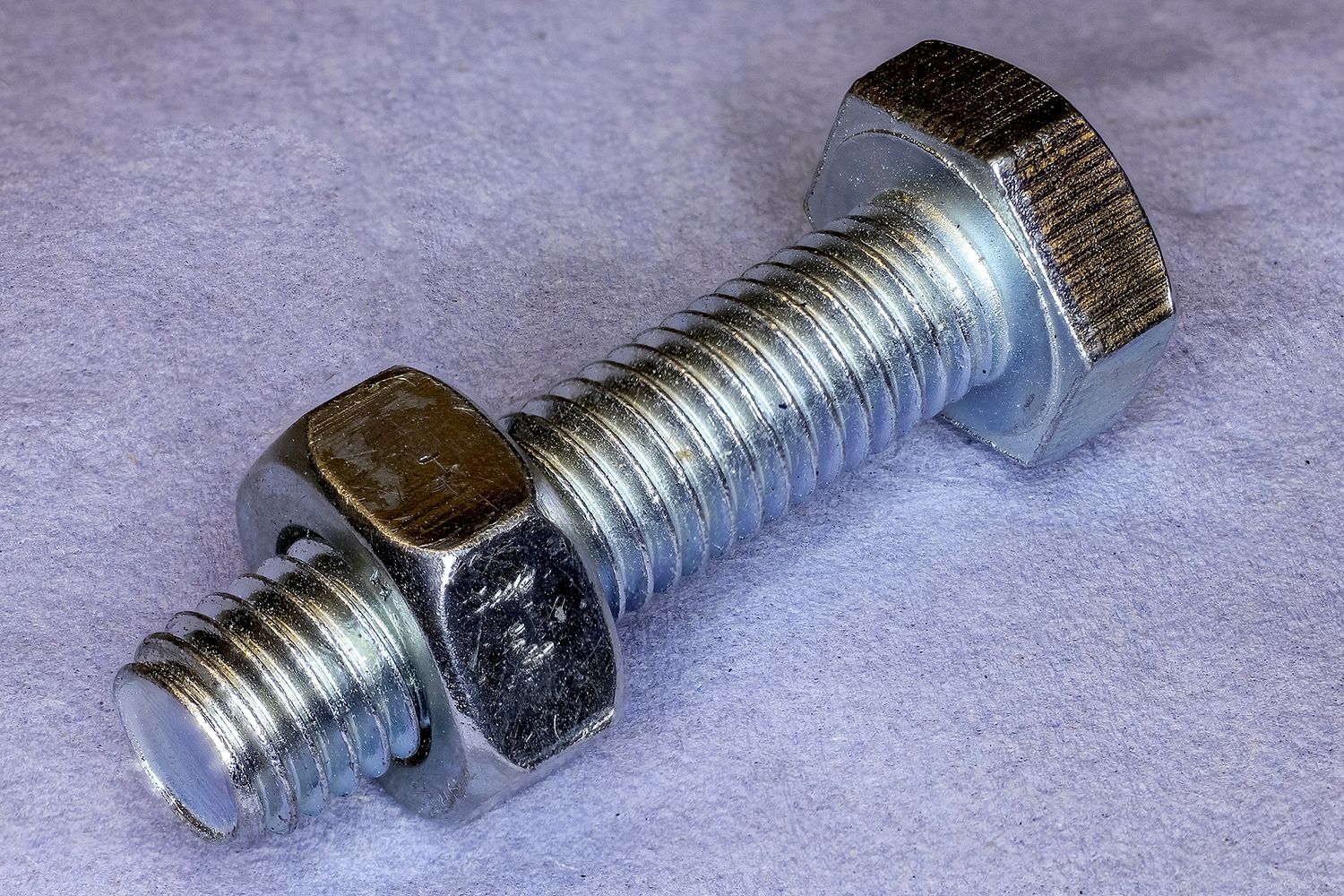
Основные способы нарезки
Для нарезания применяют следующие методы:
- Токарная обработка. Используются токарные станки, оснащаемые гребёнками, резцами.
- Резьбофрезерование. Оно осуществляется с помощью фрезерных станков, в которых устанавливаются нужные фрезы или резьбонарезные вихревые рабочие головки.
- Ручная нарезка. Для неё подходят специализированные инструменты – метчики, плашки.
- Накатывание. Выполняется с помощью накатных головок, плашек и гребёнок, раскатников, роликов.
- Шлифование. Для него созданы специальные круги.
Важно! Применяются и другие способы: штамповка, прессование, выдавливание, литьё. Но они не относятся к нарезке, то есть не предполагают снятие слоя металла.
Инструмент для нарезания резьбы
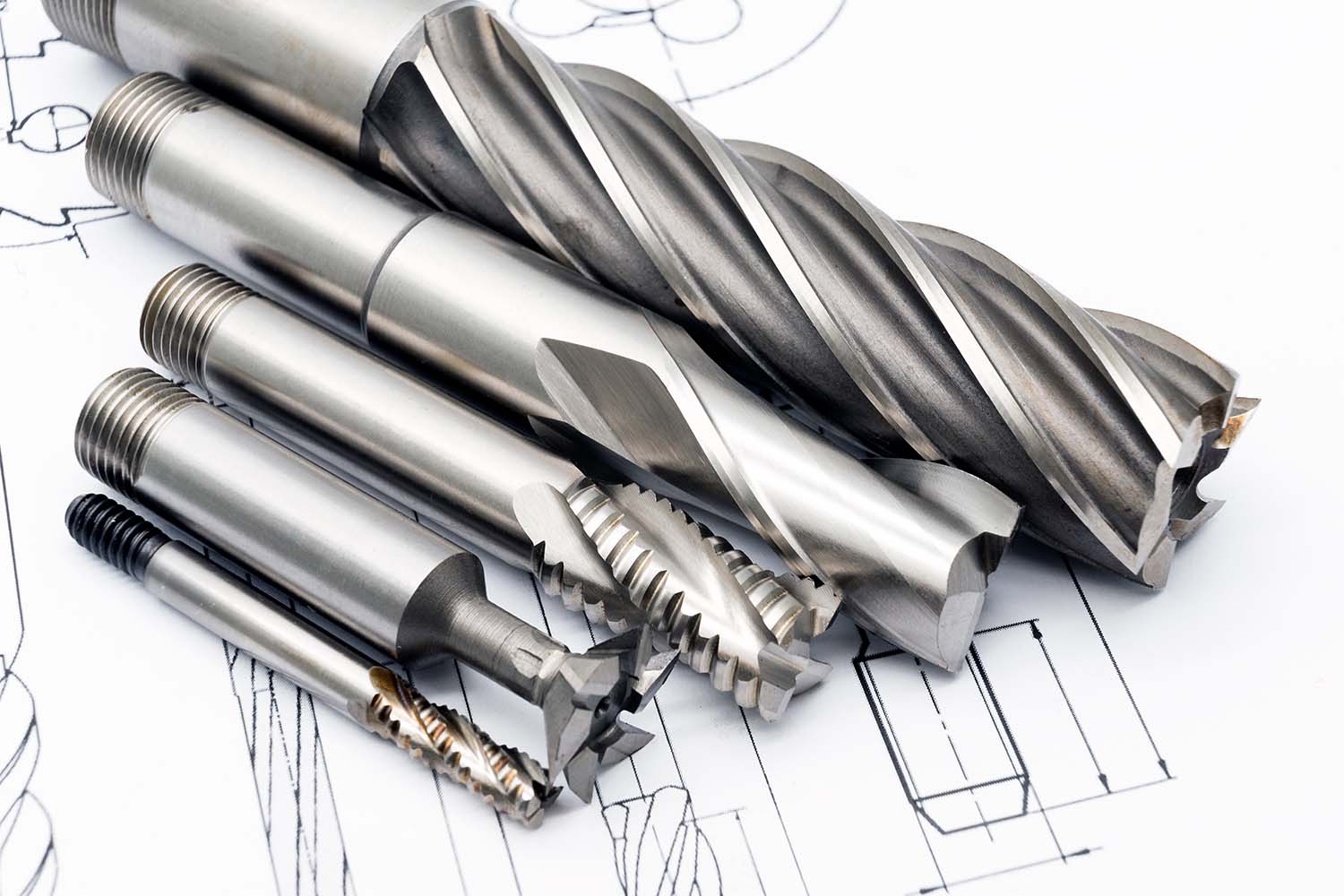
Список необходимых материалов и оборудования:
- Метчик. Это инструмент, представляющий собой винт с прорезанными в рабочей части винтовыми либо прямыми канавками, которые образуют заострённые кромки. Функция метчика – это нарезание резьб внутреннего типа в металлических заготовках. Данные инструменты, используемые для формирования новых резьбовых поверхностей вручную, обычно продаются комплектами. Черновой метчик снимает порядка 60% удаляемого слоя металла, средний убирает около 30% и повышает точность, а чистовой применяется для финишной нарезки с калибровкой. Для мелкой метрической или трубной резьбы достаточно двух инструментов. Метчики бывают ручными и машинными. У первых хвостовик длиннее.
- Оборудование для сверления. Для толстого металла подойдёт сверлильный станок, в котором предусмотрена функция регулировки количества оборотов. Если заготовка не очень толстая и относительно мягкая, то достаточно электрической дрели со сверлом. При этом электродрель должна работать с минимальной скоростью.
- Тиски. Они позволяют надёжно фиксировать детали для предотвращения их смещений.
- Дополнительные приспособления. Это кернер, который поможет сделать метки (насечки), молоток.
- Расходные материалы. К ним относятся смазка, предупреждающая перегревание заготовок и вращающихся рабочих насадок инструментов, а также ветошь для удаления масла, смазочной жидкости.
Важно! Плашка не понадобится, так как она создаёт только внешние резьбы.
Выбор сверла
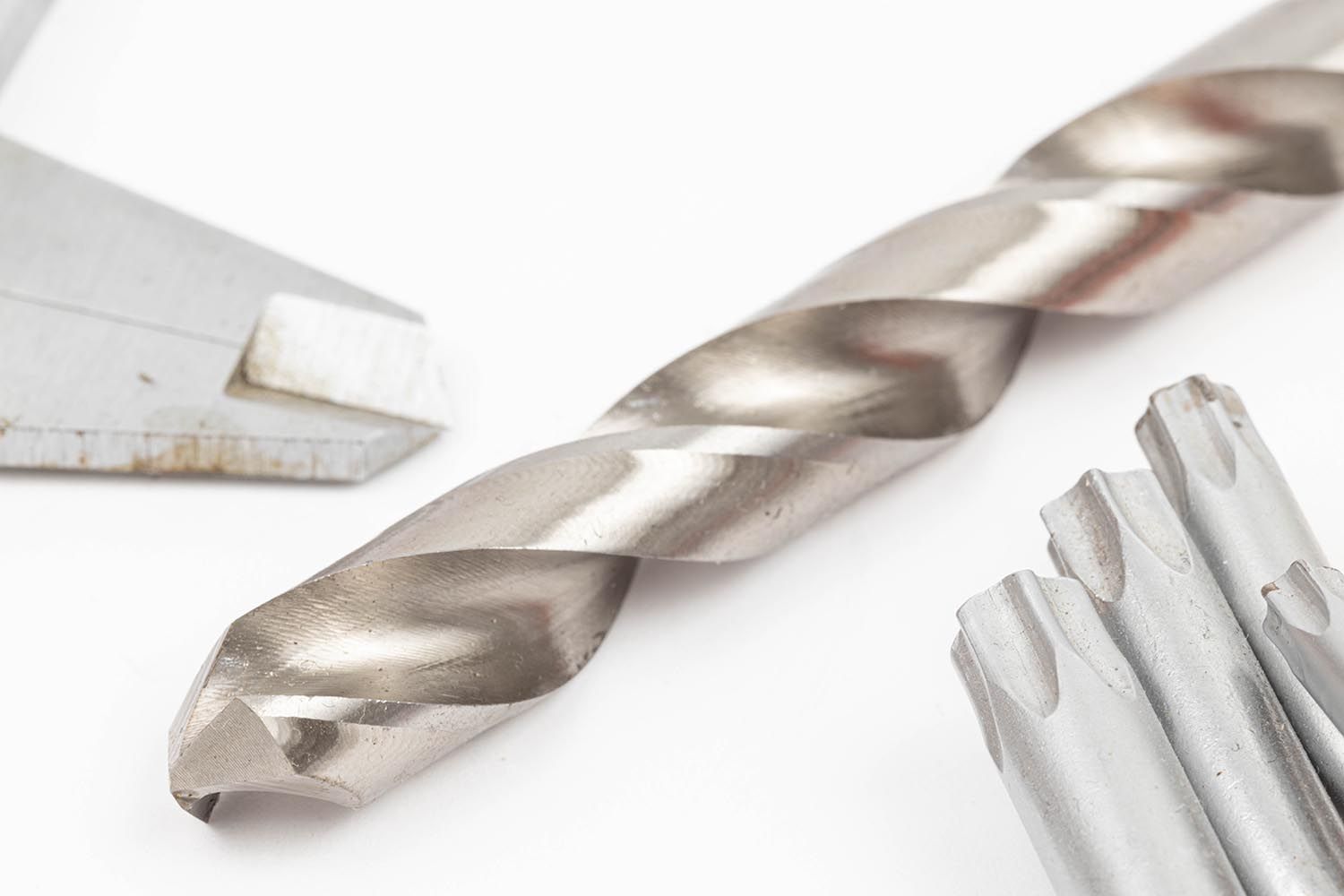
Чтобы сверлить отверстие без повреждений материала и поломок инструмента, важно подобрать правильное сверло. При его выборе учитывайте несколько важных моментов:
- Берите во внимание характеристики металла. Обычно применяют свёрла из быстрорежущих сталей с содержанием кобальта, но если материал очень твёрдый и плохо поддающийся обработке, то лучше использовать инструмент из сплава повышенной твёрдости.
- Мягкость металла влияет на диаметр сверла. Резьбу М10 в мягких сплавах следует создавать инструментом диаметра 9,3 мм, а в твёрдых – на 1 миллиметр больше.
- Под хрупкие металлы подбираются свёрла на 1 миллиметр меньше, чем для металлов обычных, например, сталей.
- Угол заточки сверла определяется по твёрдости материала, но не превышает 140 градусов. Например, для чугуна, сталей, твёрдой бронзы оптимальное значение – от 116 градусов до 118, для красной меди – 125, для алюминия – максимальные 140.
- Даже если шаг идентичный, диаметры свёрл различаются для метчиков стандартных и раскатников.
- Для получения качественной резьбы и сохранения целостности метчика нужно использовать справочную литературу и сверяться с государственными стандартами.
- По диаметру сверло должно соответствовать величине создаваемого отверстия.
Как правильно определить диаметр отверстия
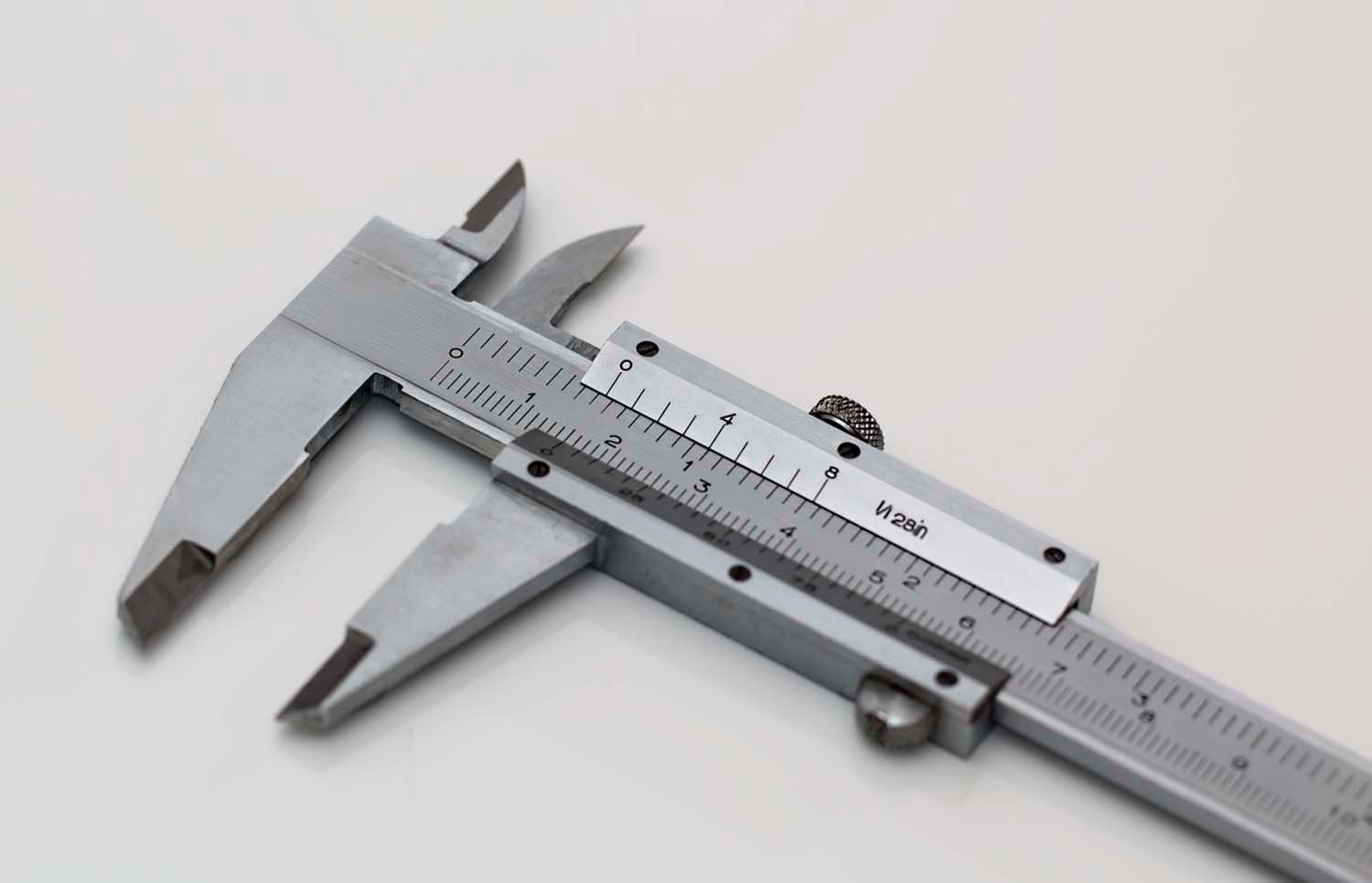
На первых этапах работ нужно просверлить правильно и точно отверстие под резьбу. Если его диаметр окажется больше нужного, то соединение со шпилькой или болтом лишится прочности. При уменьшении параметра возрастёт вероятность поломки детали при вкручивании или даже повреждения инструмента, применяемого для ввинчивания.
Если нужно сделать стандартную резьбу, например, М8, М6 или М12, то найти её диаметр с учётом шага можно в таблицах профильных справочников. Если требуется нестандартный вариант, то поможет расчёт по несложной формуле:
ДО = НД – Ш, где ДО – искомый размер отверстия, НД – номинальный диаметр шпилечной или болтовой детали, совмещаемой с нарезаемой резьбой, а Ш – шаг. Полученное число – это диаметр отверстия, а также используемого сверла.
Как нарезать резьбу
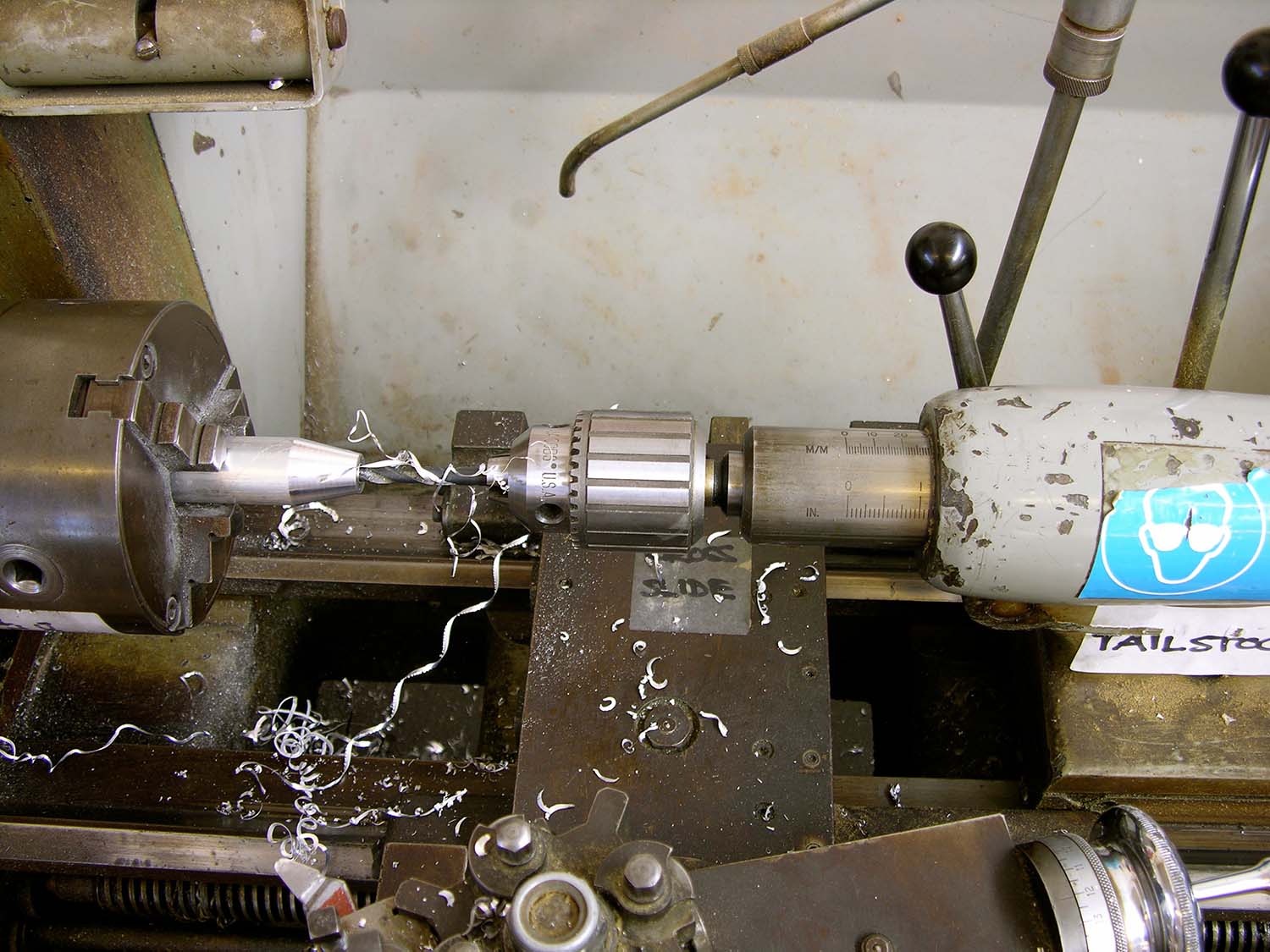
Процесс несложный, но требует внимательности и точности движений, соответствия действующим стандартам. Чтобы добиться ожидаемых результатов, нужно строго соблюдать технологию, а также использовать подходящие инструменты. Ниже рассмотрим все этапы и нюансы.
Подготовка к нарезке резьбы
При подготовке нужно:
- Определить перечень инструментов, а также выяснить диаметр сверла. Для этого нужно изучить информацию из справочника.
- Подготовить всё необходимое. Оно должно быть в зоне доступа. Лучше разложить инструменты на ровную поверхность, например, на рабочий стол.
- Зафиксировать изделие. Если оно небольшое, для крепления подойдут тиски. А крупногабаритную заготовку можно разместить на горизонтальной ровной поверхности и обездвижить подручными средствами, к примеру, резиновой прокладкой для исключения скольжения или же грузами.
- Наметить точку старта сверления в металле кернером. Если он автоматический, то разместите его в нужной зоне и приведите в действие. Ручной кернер расположите в точке, зафиксируйте и с усилием, достаточно резко ударьте по основанию молотком.
- Определить режим сверления – скорость вращения сверла. Она зависит от диаметра инструмента. Если он менее 5 мм, оптимальное число оборотов в минуту – от 1300 до 2000. Для диаметра от 6 до 10 мм подойдёт скорость от 700 об/мин до 1300, для 11-15 – от 400 до 700, а для 16-20 – от 300 и не больше 400.
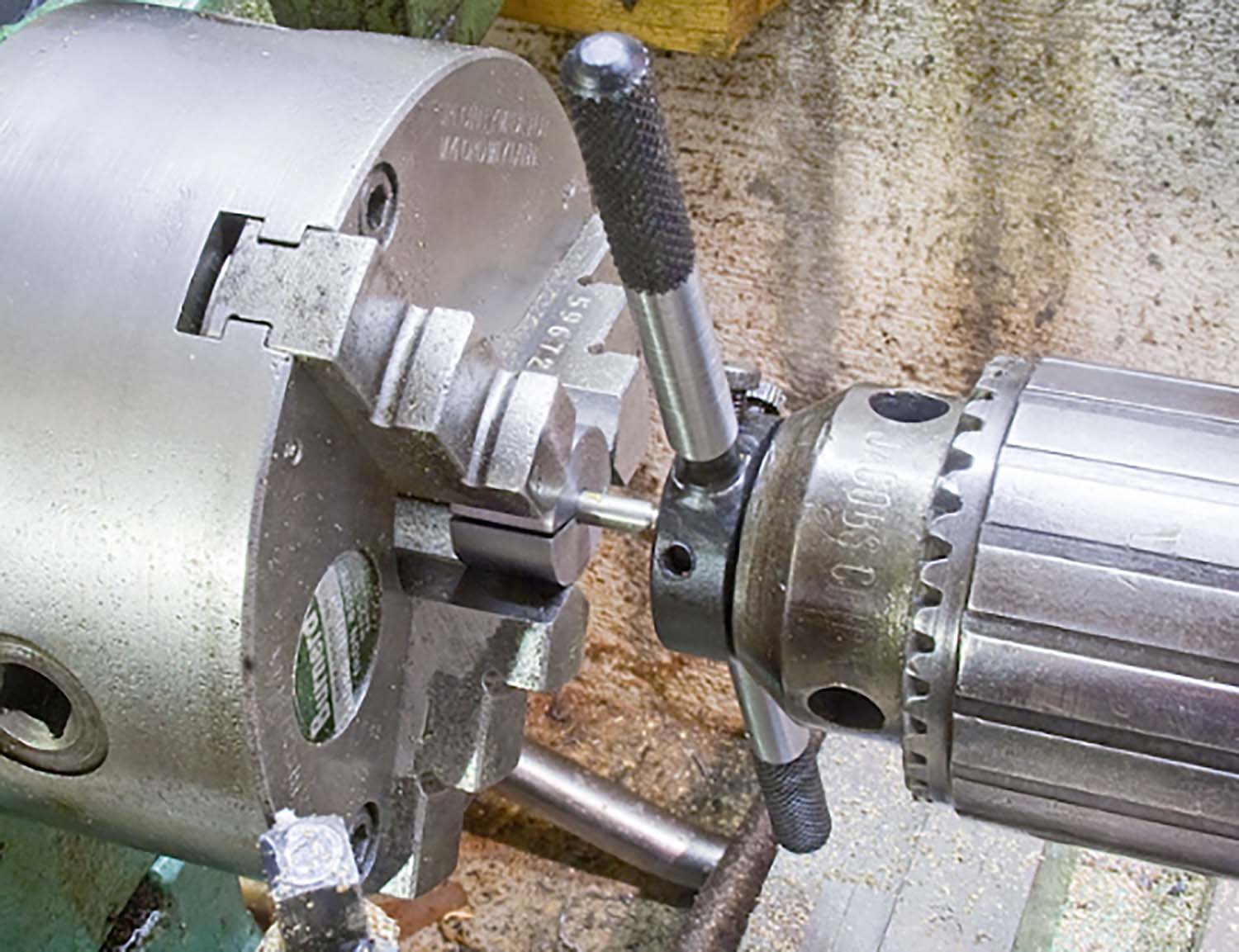
Порядок выполнения работ
Работать следует по такому алгоритму:
- Разместите сверло в сделанной кернером насечке.
- Крепко удерживайте дрель в руках, располагайте её строго вертикально по отношению к поверхности заготовки. Включайте инструмент, без больших усилий надавливайте на него, чтобы углубиться в материал. По мере продвижения внутрь давление ослабляйте. Отслеживайте отведение стружки. Если произошло заклинивание, смените направление вращения и выньте сверло. Очистите его и отверстие от образовавшейся стружки. Продолжайте до завершения.
- Заводите метчик в готовое отверстие, контролируя совпадение осей. Начинайте медленное поворачивание.
- Когда возникнет сопротивление, выкрутите метчик, поворачивая его в противоположном направлении. Из канавок извлеките скопившуюся там стружку.
- Ввинчивайте метчик до достижения заданных параметров. Если отверстие сквозное, то конец инструмента должен выйти снизу детали. Если оно глухое, то проворачивайте инструмент, пока он не упрётся в дно.
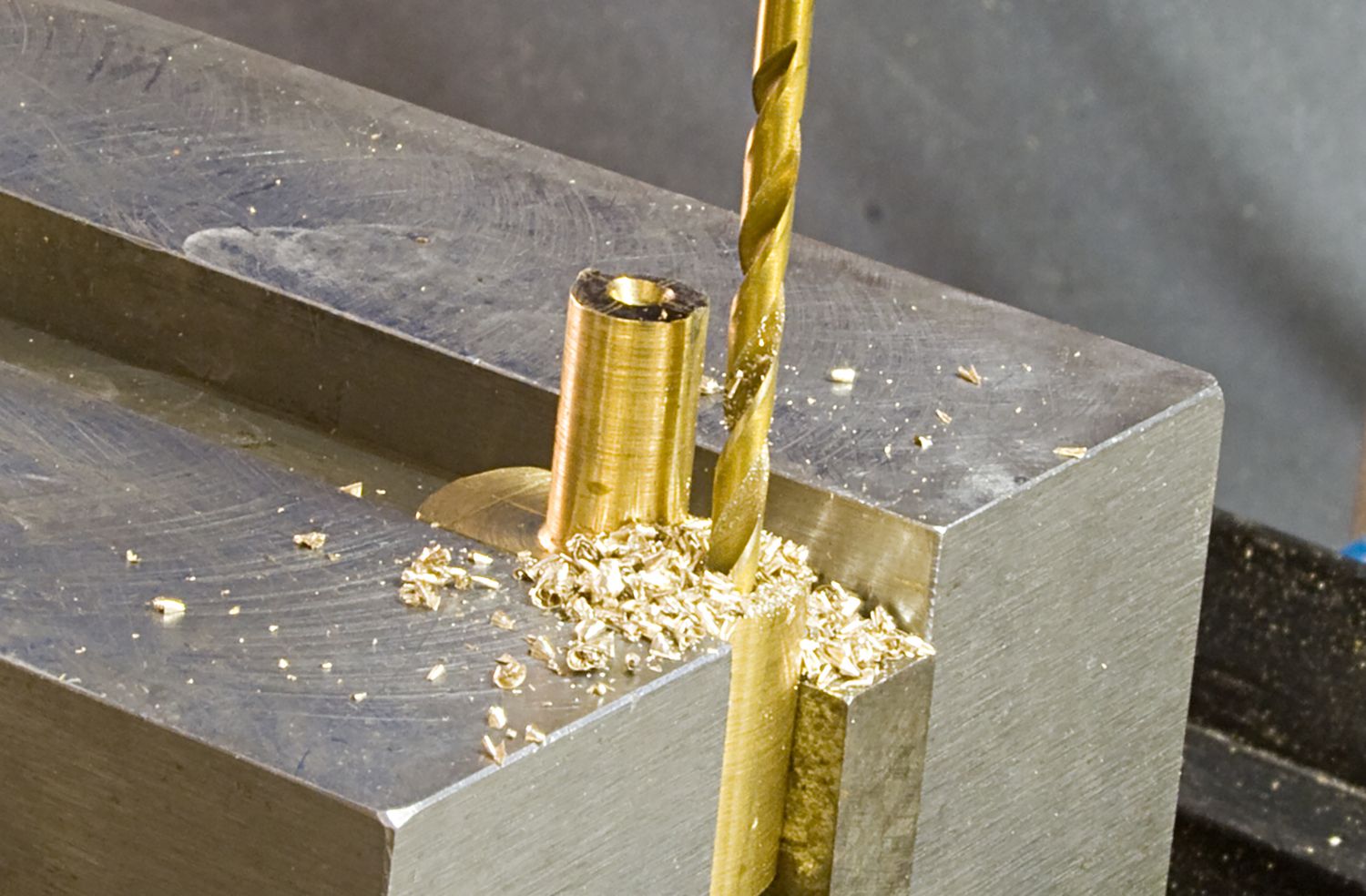
Если резьба создаётся в глухом отверстии, то для свободного конца метчика нужно предусмотреть свободное пространство. Для этого сверление осуществляется на глубину больше зоны ввинчивания. Если сделать это невозможно из-за размера или формы детали, тогда можно просто срезать передний свободный участок метчика.
Совет! Чтобы метчик шёл легче, можно смазывать рабочую зону. Для сталей подходит олифа, для алюминия – керосин, скипидар, спирт. Если ничего из перечисленного нет, подойдёт машинное масло, но эффект смазывания будет хуже.
Заключение
Создать резьбу возможно своими руками, но, во-первых, это потребует наличия специальных инструментов, которые должны тщательно подбираться с учётом величины отверстия, свойств металла. Во-вторых, необходимо владеть навыками эксплуатации дрели и метчика, а также достаточной силой для сверления твёрдого материала. В-третьих, малейший просчёт или неаккуратное движение чревато дефектами, несоответствием диаметра. Это снизит качество соединения, ослабит его или приведёт в полную негодность. Даже если болт или шпилька зафиксируется, в будущем конструкция может не выдержать нагрузок из-за допущенных ошибок.
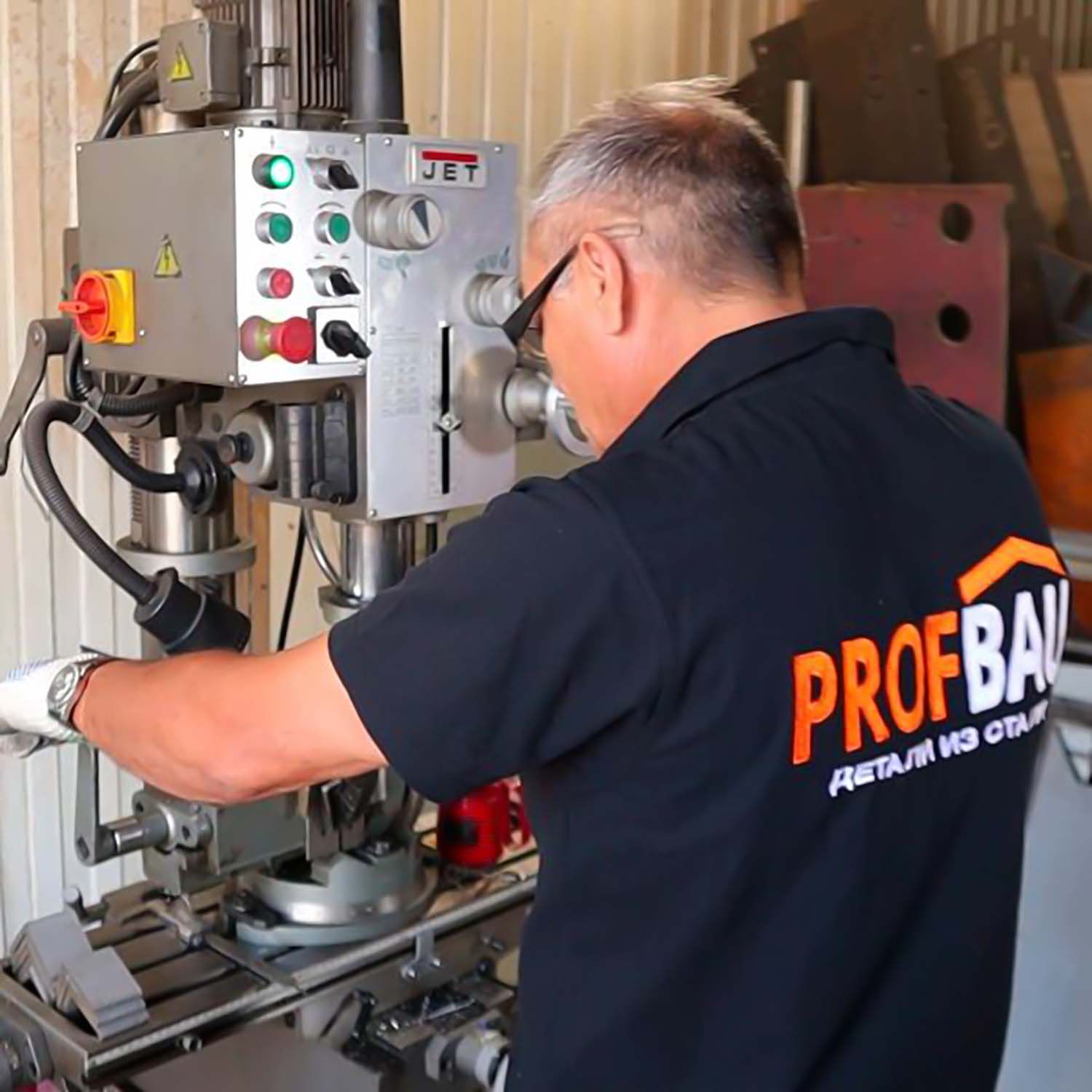
Чтобы получить качественное резьбовое отверстие, лучше доверить его создание профессионалам. Обратитесь в компанию Profbau, которая имеет большой опыт металлообработки. Наши квалифицированные специалисты постоянно совершенствуют свои навыки и знания. Мы строго соблюдаем стандарты, технологии и требования заказчиков. Автоматизированное современное оборудование сводит к минимуму риски ошибок и брака. Мы создаём резьбовые отверстия любых размеров, в любом металле, по любому техническому заданию, в том числе нестандартному. Свяжитесь с нами по телефону, по электронной почте или путём заявки с сайта.