Азотирование металла — многоэтапный технологический процесс, предназначение которого заключается в обогащении поверхностного слоя детали молекулами азота. Масштабное применение способа в разных сферах деятельности признали актуальным не так давно. Технология была создана и предложена на рассмотрение в начале XX века известным академиком, опытным химиком и по совместительству талантливым металлургом Н.П. Чижевским. Разработки русского ученого способствовали улучшению технических и физических характеристик готовых изделий, выполненных на основе стальных сплавов.
При насыщении азотом не исключают факта проведения дополнительного ряда сопутствующих мероприятий. Будущий продукт подвергают процедуре предварительного закаливания, выравнивают при помощи шлифовки, выполняют термическую обработку, шлифуют. Реализация жизненного цикла не нуждается в крупных вложениях и привлечении большого количества рабочей силы. Благодаря этому процедура востребована на производственных мощностях крупного, среднего и малого бизнеса.
Особенности насыщения металла азотом
Азотирование — это поэтапное преобразование поверхностного слоя, основанное на принципах термохимического взаимодействия. Предназначение метода заключается в повышении прочности, износостойкости, долговечности и устойчивости сплавов к коррозии. Ближайшим аналогом азотации является процесс цементации, который уступает ей по качеству готового продукта.
Суть технологии заключается в нагреве металлических поверхностей в контролируемой среде с высоким содержанием аммиака. Так материал приобретает новые полезные свойства, в перечень которых входят:
Для выполнения работ на должном уровне необходимо учесть ряд обязательных условий перед началом их проведения. Для этого используют определенные типы и марки сплавов, свойства и особенности которых перечислены ниже. От используемого материала зависит подбор надлежащего способа, а также состава рабочей среды.
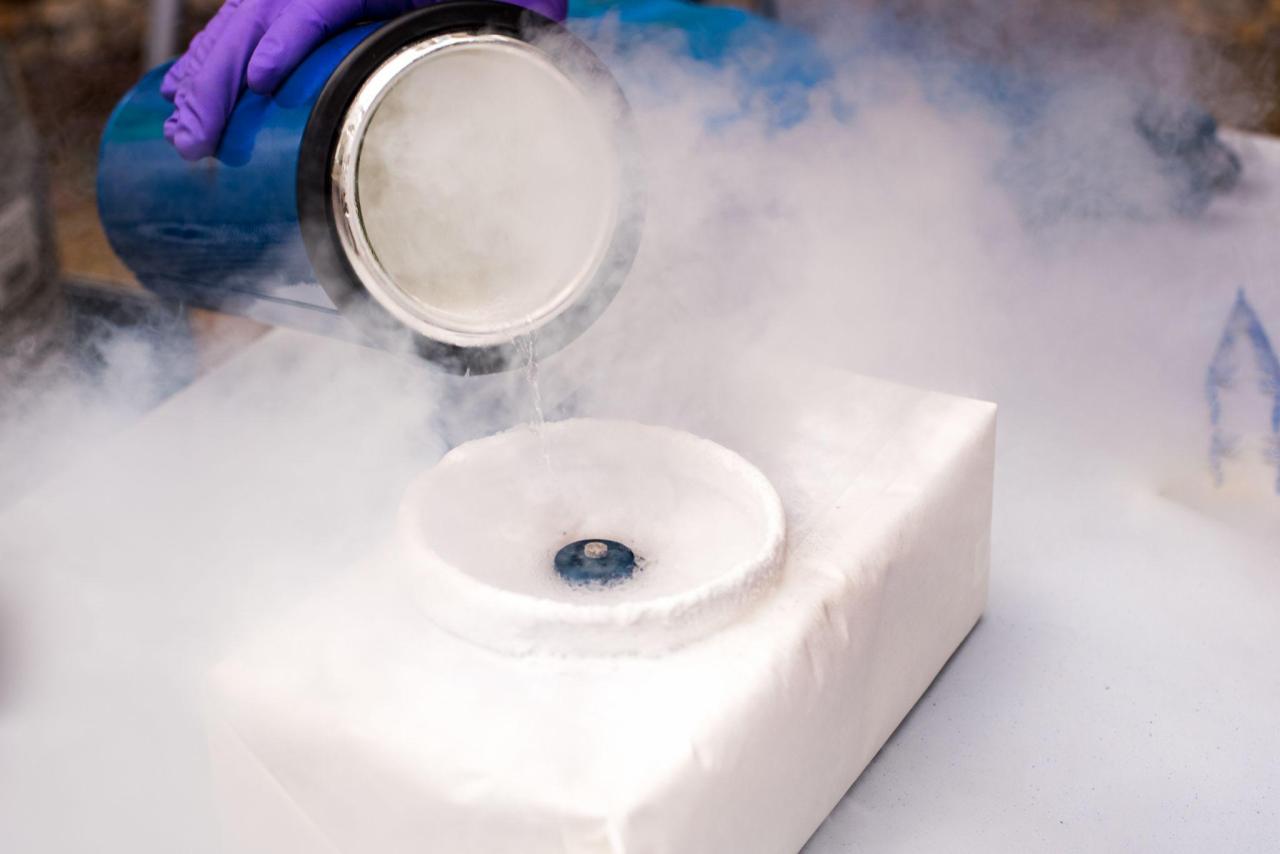
Виды азотирования
Для реализации не требуется поддержание чрезмерно высоких температур. За счет этого сокращаются риски возможной деформации, продукт сохраняет приобретенную форму, размерную точность, требуемую конфигурацию. Это свойство считают особенно полезным в ситуациях, когда насыщение азотом выполняют после финишной подгонки методом шлифовки. По окончании работ достаточно выполнить стандартную полировку деталей.
К недостаткам термохимической методики относят высокую стоимость ее реализации. Также стоит учесть время, которое требуется для выполнения полного цикла мероприятий. В некоторых случаях на это требуется от двух до трех суток. Наличие современного технологичного оборудования — обязательное требование, без которого готовый продукт теряет надлежащее качество и функционал. Разновидности и ключевая специфика каждого способа азотации перечислены ниже.
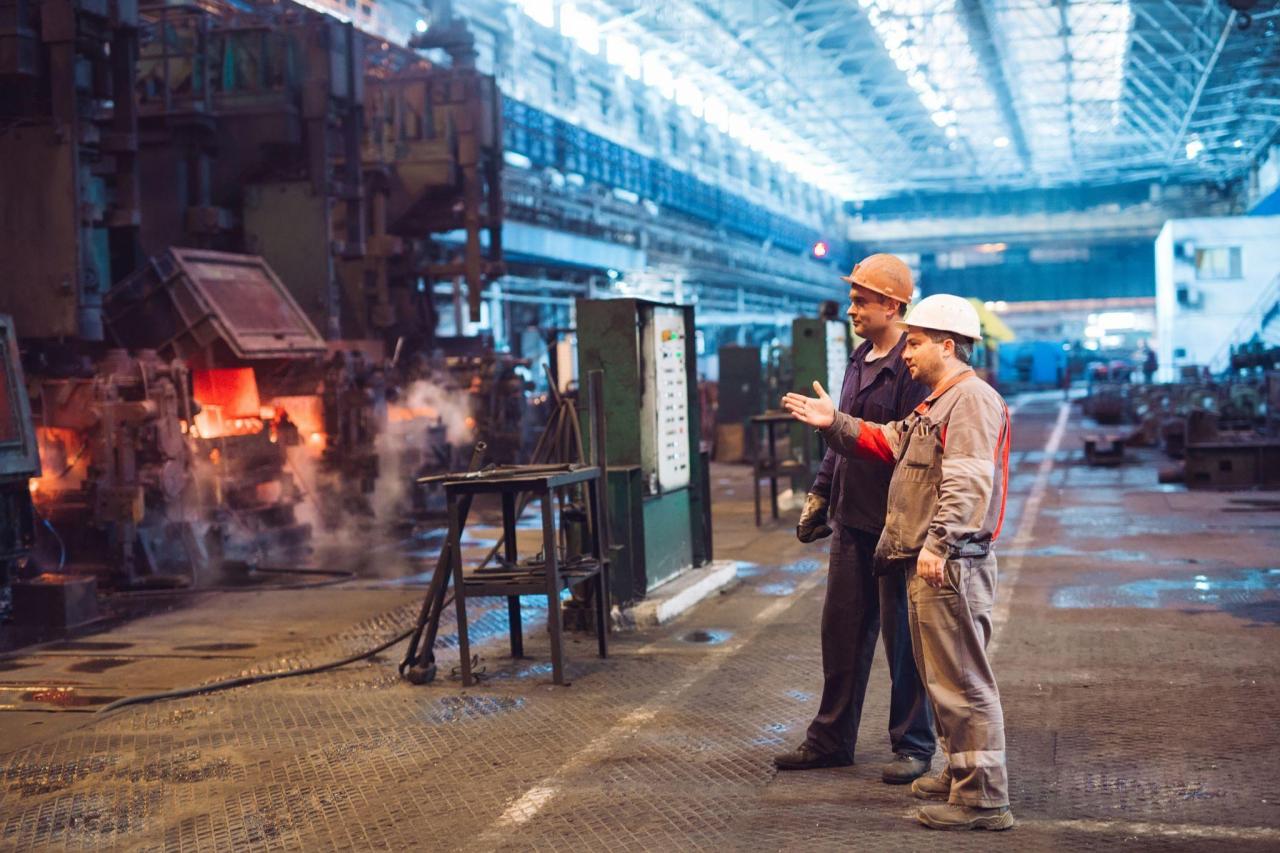
Газовая азотизация
Представляет собой классический способ насыщения металла атомами N (Nitrogenium). Принцип основан на использовании определенного типа газовой смеси, основу которой составляют пропан и аммиак в равных пропорциях. При необходимости первый компонент заменяют газом, задающем обратное направление окислительной реакции. Температура рабочей среды при этом не превышает + 579°С. Проникновение атомов азота в кристаллическую решетку длится в течение трех часов. Время проникновения активного вещества между молекулами корректируют с учетом сложившихся обстоятельств. На обрабатываемой плоскости образуется тонкое защитное покрытие достаточной жесткости и твердости. Ускорить процесс диффузии можно путем жидкостного азотирования при Т +570°С. В качестве контролируемой среды используют расплав солей цианистоводородной (синильной) кислоты.
Развитие и усовершенствование методики в сфере металлургической промышленности допускает использование ионно-плазменной азотации стали или ее обработку при тлеющем разряде. Для реализации поставленной задачи к герметичной камере подводят соответствующее напряжение. В роли анода выступает резервуар, роль катода выполняет сам металл. Направленный поток ионов способствует образованию достаточного количества плазмы, цель которой заключается в равномерном нагреве обрабатываемой поверхности. Следствием такого взаимодействия является диффузионное насыщение заготовки азотом с последующим образованием плотного защитного ряда.
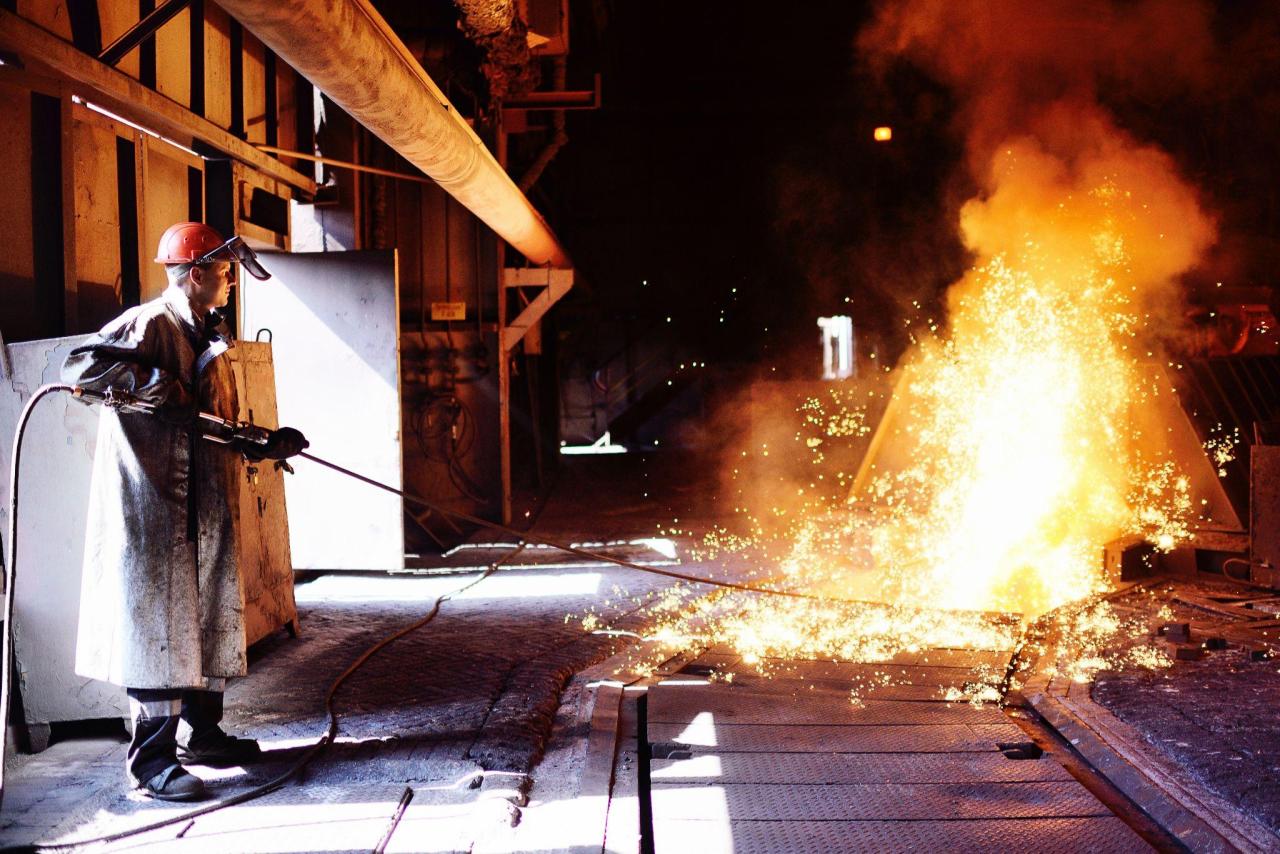
Термохимический процесс
Принцип действия заключается в применении муфеля (реторты), внутрь которого помещают металлические заготовки. Наполненную плотно закрытую емкость помещают в специальные печи. К аппарату для воспроизведения реакций подводят аммиак, поступающий под давлением. При нагревании атомы проникают в поверхностные слои материала, образуя тем самым твердое равномерное покрытие. Использование аммиака аргументировано его полезными свойствами. При обеспечении благоприятных условий вещество освобождает содержащийся в его составе азот. Повышение твердости и увеличение степени защиты от коррозии обеспечивается вследствие образования нитритов, появление которых вызвано диффузным преобразованием физических характеристик стали. Для предупреждения риска окисления печь постепенно охлаждают, готовый продукт извлекают после полного остывания муфеля. При соблюдении технологии максимальная толщина защиты составляет до 0,6 мм включительно. На получение качественного результата влияют следующие факторы:
Для ускорения процесса диффузии достаточно повысить температуру нагрева. Существенное отклонение от нормированных термических показателей может привести к сгущению либо свертыванию нитридов, а также снижению твердости образуемого защитного слоя.
Технология азотирования
В ее основу входит термообработка разноформатной продукции при непрерывном поступлении аммиака внутрь рабочего резервуара. Для практической реализации используют специализированное печное оборудование. Цель метода — приобретение новых полезных свойств без утраты исходных технических характеристик.
Уникальностью технического решения является сохранение геометрических параметров объекта. Возможные риски, связанные с деформацией заготовок, приближены к нулевой отметке. Причина этому — отсутствие экстремальных температур. Еще одно преимущество метода заключается в стабильном поддержании приобретенных качеств при разной интенсивности применения готового продукта с учетом воздействующих на него нагрузок. Эксплуатационные качества материала также поднимаются на новый уровень. Долговечность, износостойкость, устойчивость к коррозии, высокая прочность материала вдвое выше, чем у аналогичных материалов без дополнительной подготовки.
Типы азотируемых сталей
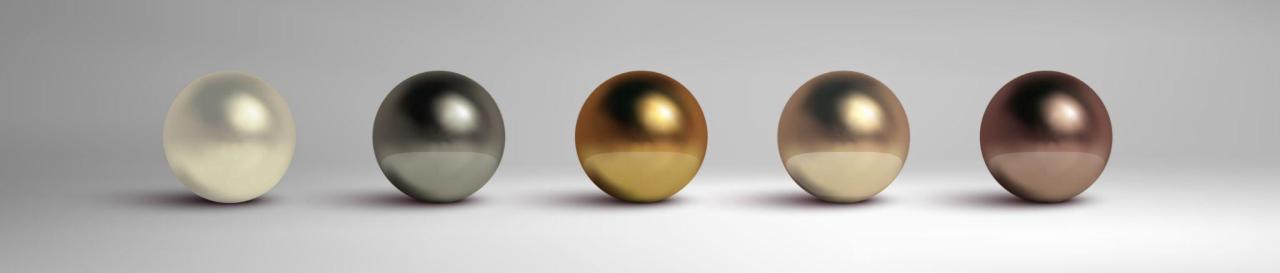
Техника укрепления поверхности при помощи атомов азота подходит для усовершенствования технических параметров стали разных марок. К ним относятся углеродистые и легированные составы, содержащие молекулы углерода в концентрации 0,3-0,5% включительно. Положительный эффект от применения получают при обстоятельствах, когда в состав вещества входят легирующие компоненты. Именно они отвечают за образование твердых и термостойких нитридов. Распространенные наименования активных элементов:
По логическому окончанию технологических мероприятий поверхность приобретает твердость, числовые параметры которой отражены в таблице ниже::
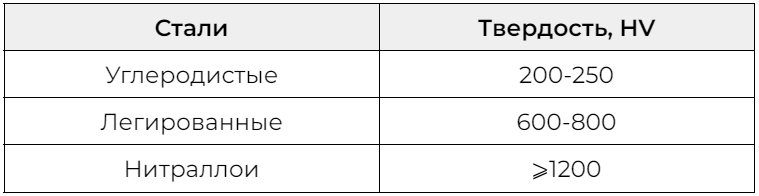
Легирующие элементы в составе повышают твердость образующегося азотированного слоя, уменьшая при этом толщину его покрытия. Особенно это касается сплавов с преобладанием в составе вольфрама, хрома, никеля и молибдена.
Подбор марки стали выполняют с учетом сложности конфигурации, предназначения и сферы применения готового изделия, условий его эксплуатации. В соответствии с ключевыми требованиями технического задания эксперты в металлургической области рекомендуют азотировать стальные сплавы, перечисленные ниже.
Основные технические параметры представлены в таблице:
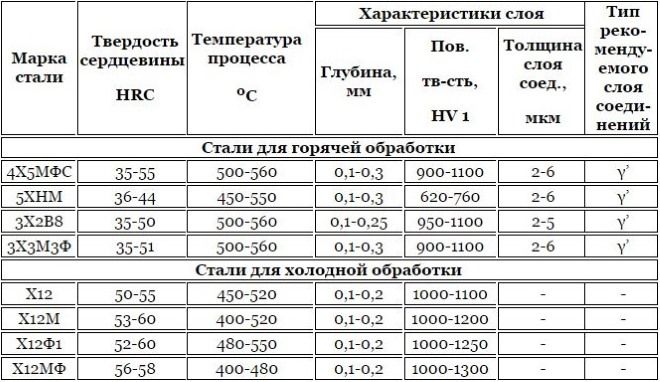
Этапы азотного насыщения
Для получения качественного результата необходимо соблюдать поэтапный регламент проведения работ. Делится на 4 стадии, каждая из которых имеет свое ключевое значение. Рассмотрим их более подробней.
Подготовительная термическая обработка
Перед непосредственной процедурой деталь необходимо подготовить. Для этого ее поверхность подвергают закаливанию при температуре от + 940 °С и выше (предельный показатель зависит от сорта материала). Для охлаждения предметы, подвергнутые закалке, помещают в воду или масло. Далее к ним применяют метод термической обработки в диапазоне + 600...+ 700 °С. Его проводят с целью достижения улучшенных показателей пластичности, а также снижения общей хрупкости. При этом показатель исходной прочности остается без изменений.
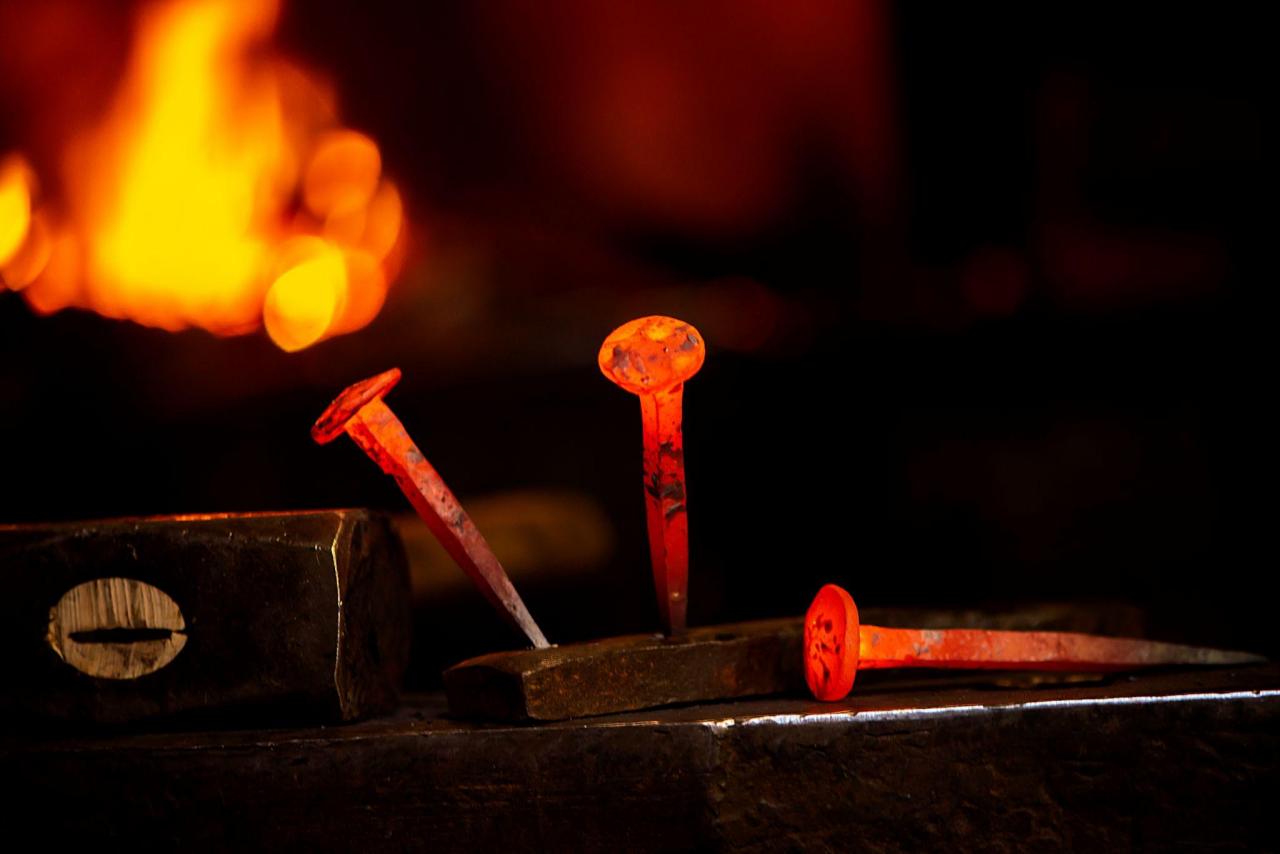
Механическая обработка
Для придания изделию надлежащего вида его шлифуют. Таким образом происходит зачистка поверхностного уровня от заусенцев и других дефектов, способных оказать негативное влияние на качество готового продукта. Параллельно со шлифовкой производят тонкую подгонку линейных размеров и геометрических параметров детали. Важность этого этапа обусловлена тем, что от соответствия конфигурации изделий и точности их габаритов утвержденному проекту зависят их эксплуатационные характеристики. Для защиты участков поверхности не требующих усиления, наносят плотное оловянное покрытие или жидкое стекло. Перекрытые таким образом участки невосприимчивы к проникновению атомов азота, за счет чего строение кристаллической решетки металла в соответствующих местах остается неизменной.
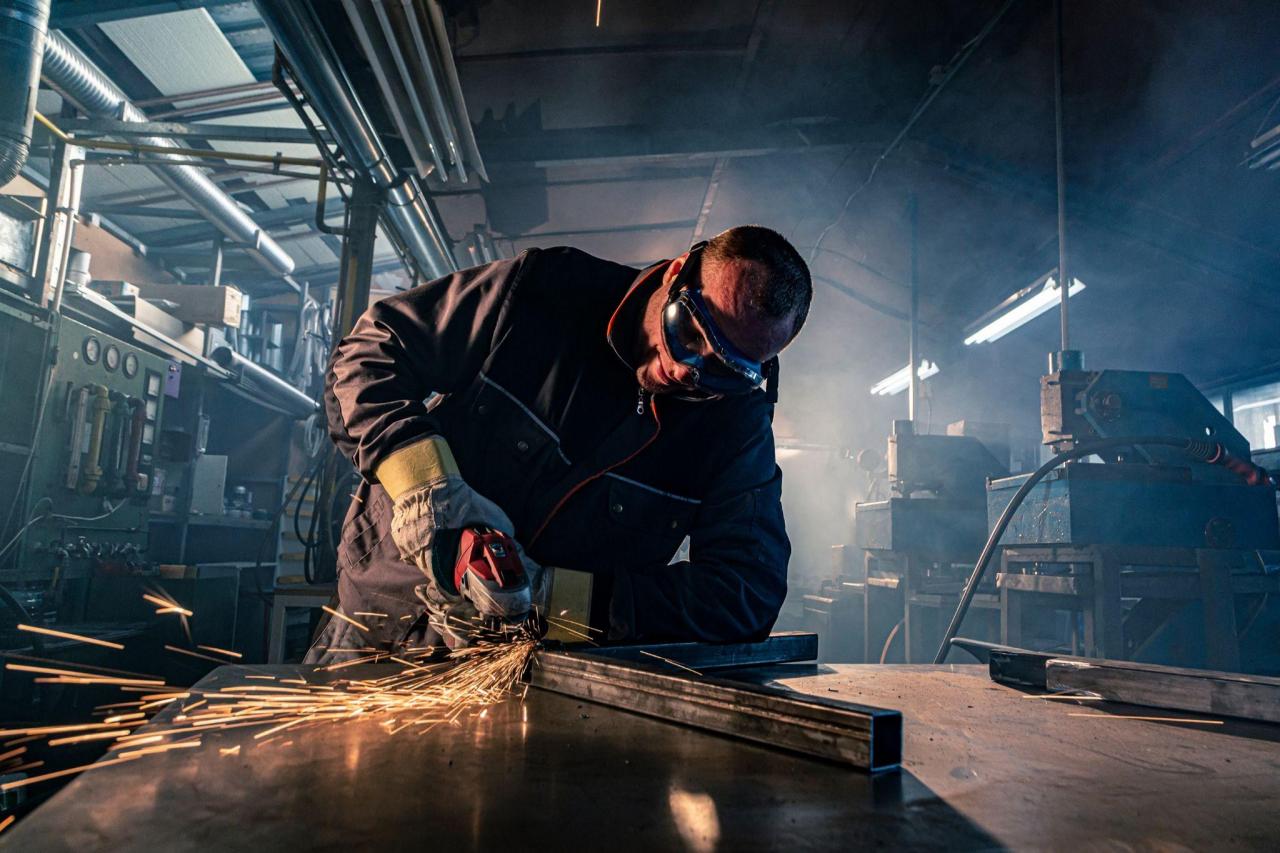
Азотация
Здесь важно соблюдать температурный режим, установленный действующими нормами и требованиями к качеству готовых изделий. Температура нагрева рабочей среды зависит от конкретной марки стали. Металлический сплав подвергается температурной выдержке внутри камеры или резервуара в течение определенного времени. Для получения равномерного поверхностного слоя требуемой толщины с заданной степенью твердости необходимо строгое соблюдение обоих перечисленных параметров.
Финишная обработка
На заключительной стадии технологического процесса выполняют тонкую шлифовку и полировку поверхности с целью достижения требуемой геометрии. Пренебрегать заключительным этапом не стоит. Технология азотирования металла происходит при относительно высоких температурах, что может привести к незначительным изменениям габаритов. Даже несущественные отклонения от нормы могут стать причиной производственного брака.
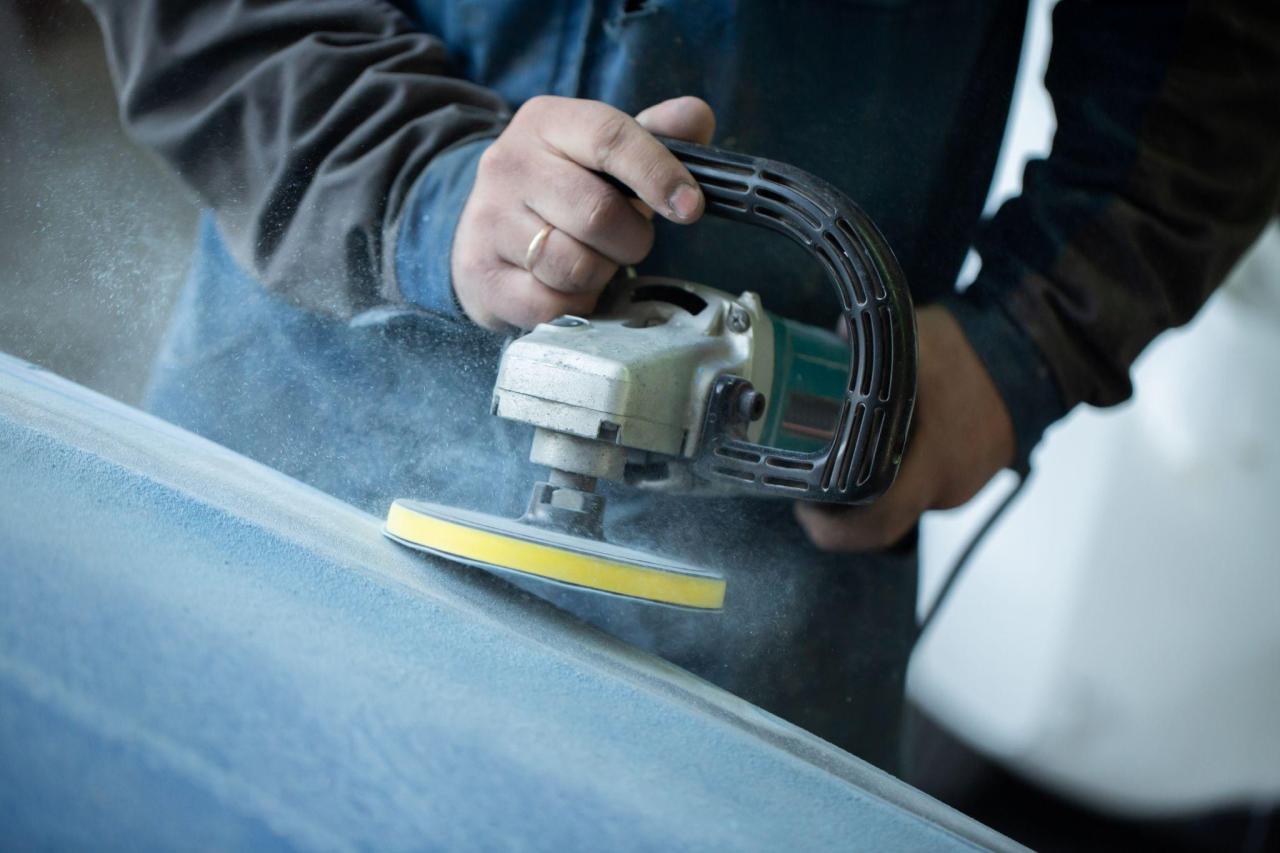
Заключение
Азотирование стали можно заказать в компании Profbau. Сотрудничество с представителями нашей компании — гарантия ожидаемого результата вне зависимости от сложности поставленных перед нами задач. Мы оказываем разносторонние услуги азотирования металлических заготовок, деталей, изделий и конструкций с участием ведущих экспертов в данной области. В процессе всех видов работ используем только профессиональное оборудование высокой точности и производительности, соблюдаем сроки исполнения договорных обязательств. Работаем со всеми категориями клиентов, взаимодействуем с заказчиками при личных встречах, по телефону или онлайн.
Преимущества компании Profbau:
Для получения предварительных расчетов оставьте заявку на сайте или по телефону: +7 (495) 138-25-25. Будем рады помочь!