Сварка используется для создания цельных изделий из отдельных элементов с формированием неразъёмных соединений. Этот технологическийпроцессприменяется в разных отраслях промышленности, для различныхпроизводств. С помощью сварных швов изготавливают каркасы строительных конструкций, самолёты, водные суда, различное оборудование, транспорт. В этой статье рассмотрим принцип технологии, виды сварки, их особенности.
Суть
Есть разные способы сварки, каждый имеет свою специфику работ и принцип создания соединений. Но суть заключается в создании прочных связей между свариваемыми элементами. Они устанавливаются на атомарном уровне за счёт воздействия внешнего источника энергии, который выделяет локальное тепло или провоцирует пластическую деформацию.
Обычно сваривание осуществляется под высокими температурами, при которых происходит расплавление материалов, их локальное смешение, слияние в единое целое. Реже используются механические воздействия (давление, ультразвуковые колебания, трение), при которых объединяются электронные оболочки. При некоторых технологиях комбинируются разные источники энергии.
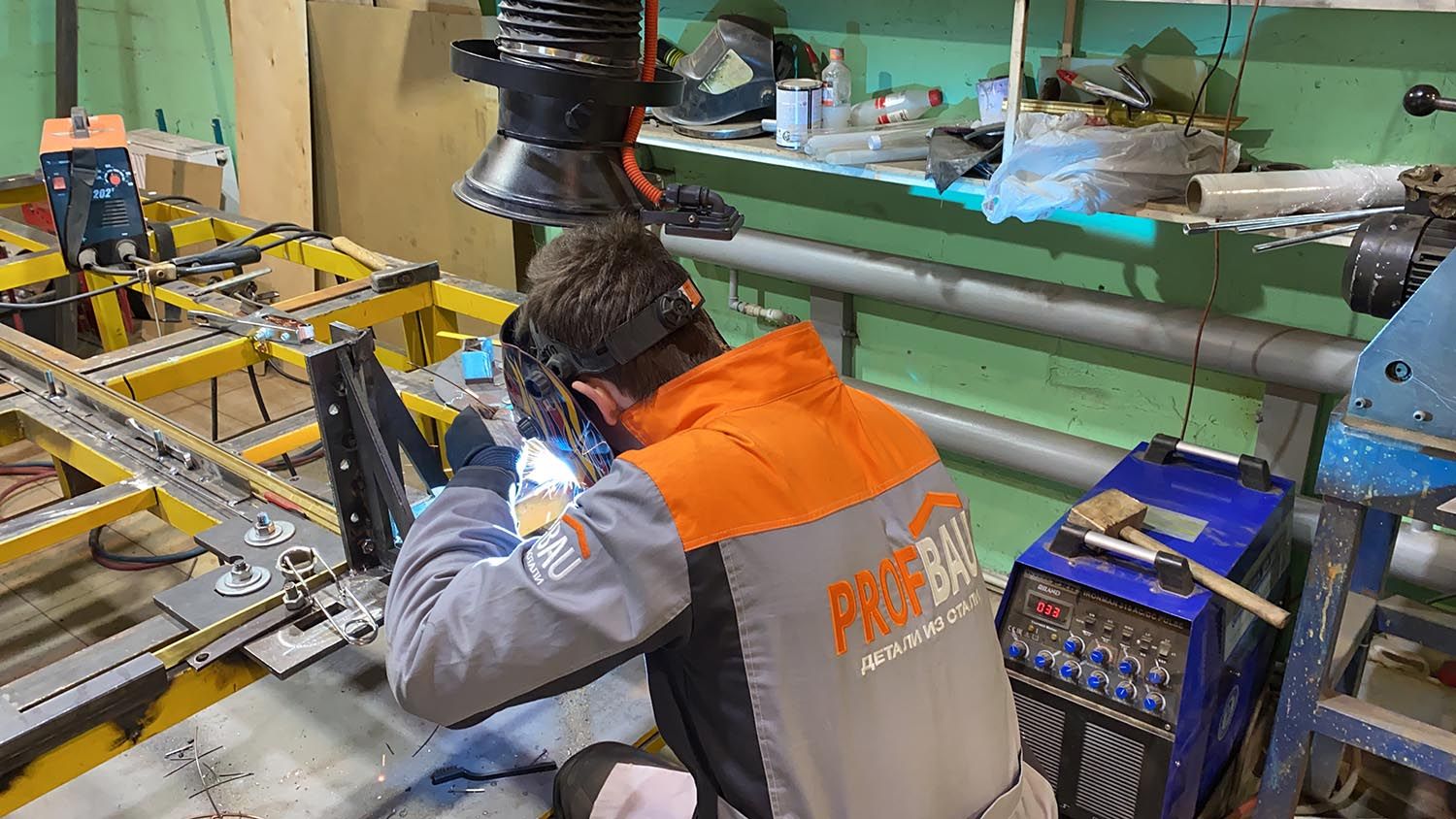
Принципы классификации
Единая классификация сварочных технологий невозможна из-за большого количества способов соединения материалов. Сегодня их существует больше 100. Можно классифицировать методы по разным критериям, но наиболее правильно выделить три признака, рассмотренных ниже.
Оказываемое воздействие
По типу воздействия, создающего неразъёмные соединения, сварку классифицируют на такие группы:
- Термическая. Сюда относятся процессы, предполагающие влияние тепловой энергии, провоцирующей плавление. Самые популярные – газовая и дуговая сварки. Их применяют для сборки металлоконструкций, для ремонта металлических изделий.
- Механическая. Это небольшой, но интересный класс. Его особенность – экономия за счёт отсутствия необходимости использования мощного источника энергии. Но для нужных результатов требуется создавать специальные условия, что не всегда возможно. В группу входят сварка трением, ультразвуком, давлением, взрывом. Область применения из-за специфичности технологий невелика.
- Термомеханическая. Тут объединяется два вида воздействия: нагревание до высоких температур и оказание давления. Пример – контактный способ, при котором электроды прогревают детали, одновременно прижимают их. Другие варианты – дугопрессовой, кузнечный, диффузионный.
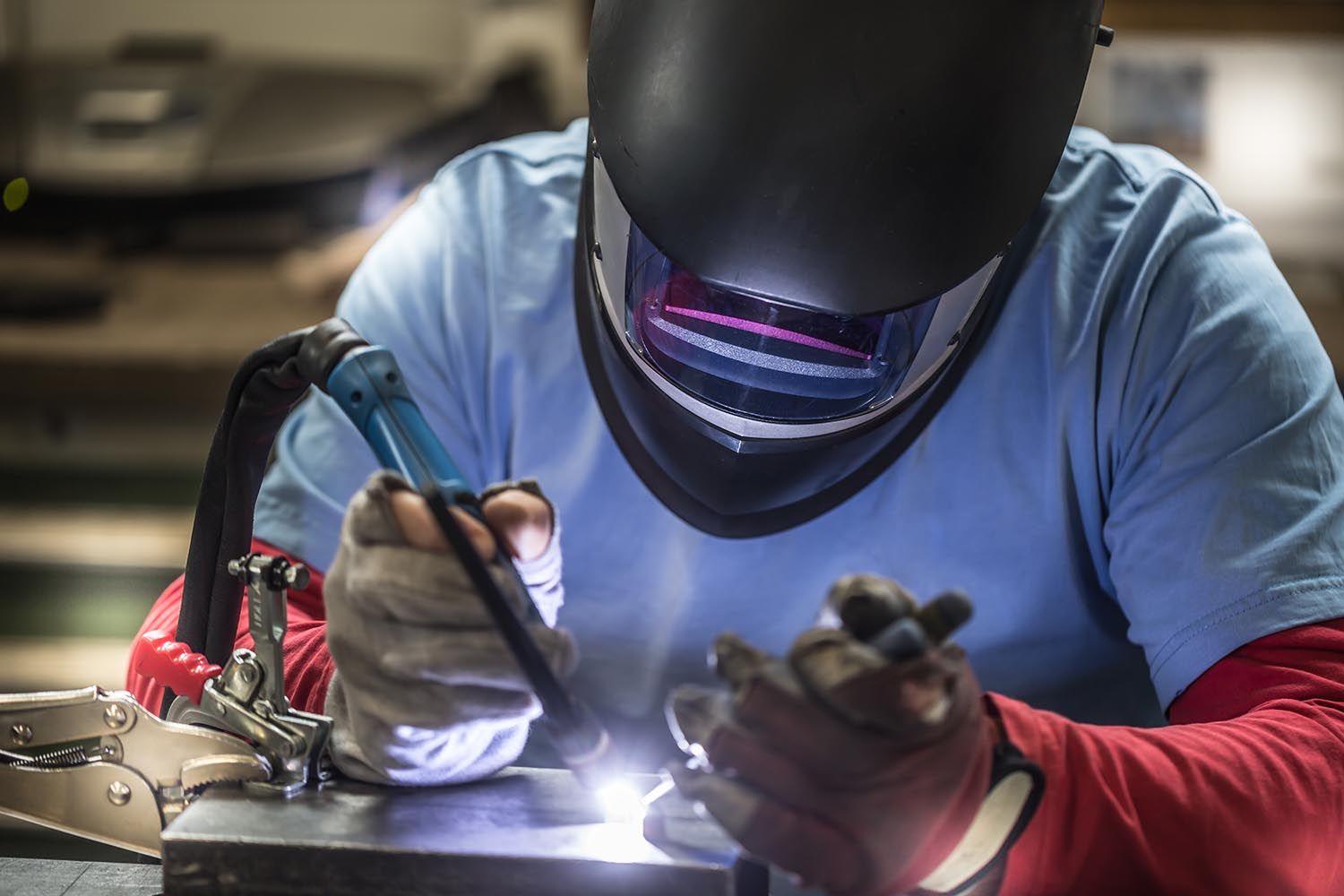
Технические признаки
Основа этой классификации – технические характеристики процесса. Это:
- Принцип предотвращения окисления. От степени защиты от окислительных реакций напрямую зависит качество создаваемых швов. Чаще всего для предупреждения окисления применяют среду, формируемую специальными защитными газами. Также используют пены, флюсы.
- Непрерывность протекания процесса. По такому критерию выделяют два вида: непрерывная сварка, при которой процедура проводится без остановок, и прерывистая, при которой необходимы периодические промежутки.
- Уровень автоматизации, механизации. Сварка бывает примитивной ручной, автоматизированной с упрощением некоторых операций, механизированной и самой совершенной автоматической с точными настройками, с минимальным участием сварщика.
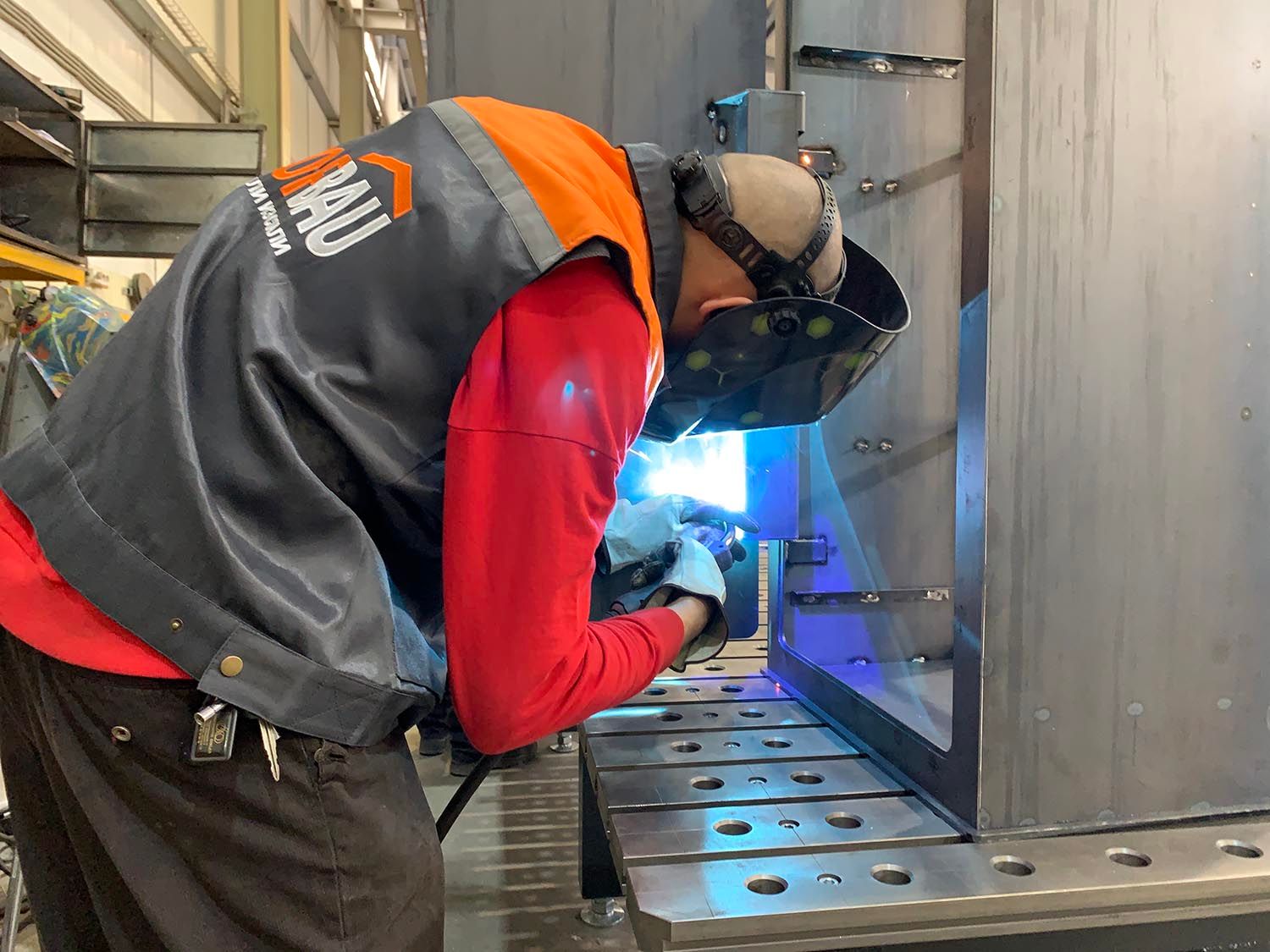
Классификация по технологическим принципам
Деление по технологическим принципам довольно противоречиво и непостоянно, ведь технологии постоянно совершенствуются, появляются новые способы. Если взять дуговую сварку, которая считается наиболее распространённой, то для неё выделяют несколько подвидов: TIG, MMA, MIG/MAG.
Виды сварки
Типы различаются по источнику энергии, по используемому оборудованию, по режимам, по условиям сваривания, по расходным материалам, сферам применения. Ниже рассмотрим методы, которые используются в разных областях.
Термическая
Технология охватывает несколько видов, а её принцип заключается в термическом, то есть тепловом воздействии. Источник тепла, роль которого может играть поток плазмы, электрическая дуга или пламя газа, формирует сварочную ванну. Данная зона состоит из расплавленного и перешедшего в жидкое состояние металла свариваемых деталей, а также из присадочного материала или электрода. При критически высоких температурах стыковые участки локально расплавляются, скрепляются и кристаллизуются, формируя единую прочную структуру.
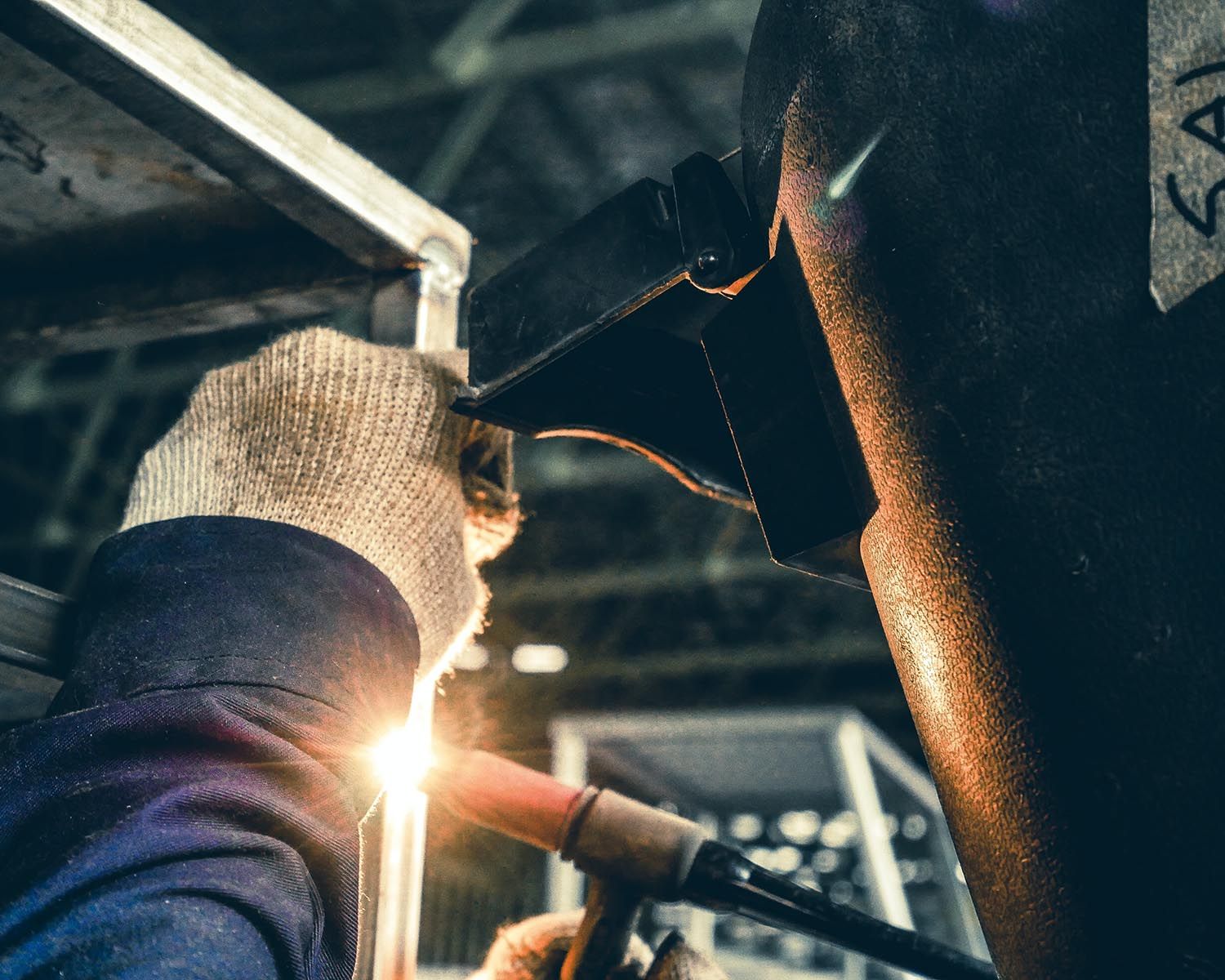
Дуговая
Самый распространённый, универсальный вид, при котором плавление металла активируется теплом, образующимся при горении дуги, возникающей под действием тока между соединяемыми заготовками и электродом, который выполняет функцию проводника. Для разжигания дуги требуется контакт электрода с поверхностью металла. Далее проводник тока нужно удалить на расстояние от 2 до 5 мм. Чем дуга короче, тем выше температура нагревания.
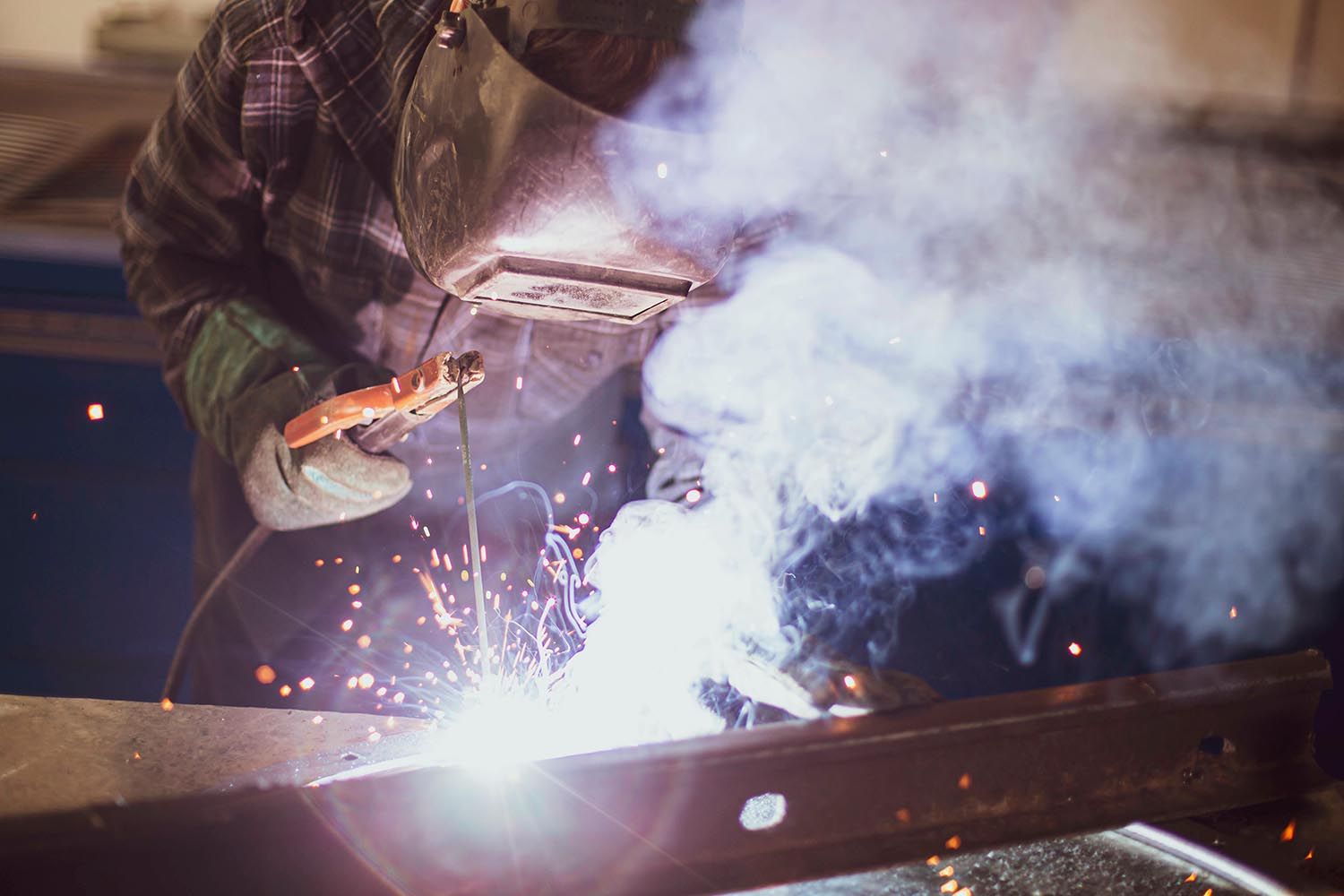
Электродуговая
Электродуговая сварка – это дуговая технология, ведь дуга не образуется без электричества. Соединяемые поверхности нагреваются, расплавляются благодаря разряду. Он возникает между свариваемым изделием и концом электрода за счёт прохождения тока. Энергия электричества переходит в дугу, вызывает значительный нагрев, который провоцирует локальное расплавление с формированием сварочной ванны. Когда жидкий металл остывает, идёт кристаллизация. Создаётся шов, который по составу, структуре и прочности аналогичен свариваемым материалам.
Электродуговая сварка делится на несколько подвидов:
- Ручная, она же MMA. Для неё применяют штучные электроды, покрытые специальной обмазкой. Операции проводятся с использованием постоянного тока (DC) либо переменного (AC). Электродное покрытие расплавляется, создаёт газовое облако. Оно сохраняет стабильность электрической дуги, доставляет в сварочную ванну необходимые химические добавки для улучшения свойств металла, а также исключает проникновение воздуха, окисление. Манипуляции осуществляются вручную с использованием специальных аппаратов – сварочных выпрямителей, трансформаторов, инверторов. Метод, если правильно подбирать электроды, применим почти ко всем цветным и чёрным металлам, включая легированные. Варить можно даже в труднодоступных зонах. Ручная сварка подойдёт опытному мастеру и новичку. Её применяют в строительстве, в изготовлении металлоизделий, в тяжёлой промышленности, при слесарных работах.
- Аргоновая сварка, имеющая название TIG. Процесс протекает с использованием неплавящегося электрода в среде из аргона, являющегося инертным газом. Электроды бывают графитовыми, угольными, вольфрамовыми. В сварном шве присутствуют только металлы свариваемых изделий, так как электрод не плавится. Могут вводиться присадки из металлических полос или прутьев. Инертный газ исключает проникновение в ванну воздуха, провоцирующего пузырение и окисление. Ток может быть как постоянным, так и переменным. Процесс трудоёмкий, требует специальных навыков, его производительность не очень высокая, зато швы качественные, без примесей. Способ подходит для листового металла, тонкостенных заготовок из меди, магния, титана, сталей (углеродистых, нержавеющих, легированных).
- Полуавтоматическая, осуществляемая непрерывным плавящимся электродом. В зависимости от защитной среды, выделяют две разновидности: с инертным газом MIG или с активным MAG. В зону сваривания в автоматическом режиме направляется проволока, являющаяся электродным материалом. Также через горелку подаётся защитный газ. Сварка проводится только с постоянным электрическим током. Производительность высокая, но формирование ровных швов требует большого опыта из-за рисков разбрызгивания жидкого металла. Зато полуавтоматическая сварка позволяет соединять различные материалы (никель, чугун, марганец, алюминий, стали и другие сплавы), в том числе разнородные.
- Под флюсом. Особенность – применение флюсового порошка, который создаёт защитный слой в сварной ванне и участках остывающих швов. Под влиянием высоких температур частицы флюса разрушаются, выделяют газ. Обычно эта технология максимально автоматизирована. Она широко применяется в промышленности. Выбирая определённые виды флюсов, можно улучшать, корректировать свойства материалов в участках стыков.
Газовая сварка
В качестве источника энергии применяют газ. Нет зависимости от электросети, что делает оборудование мобильным, относительно простым. Можно не только сваривать металлы, но и разрезать их. Список соединяемых материалов широкий. Но есть недостатки. Зона нагрева очень большая. Скорость процесса невысокая из-за медленного повышения температур. Газ расходуется в значительных объёмах, что увеличивает стоимость работы. Операции ручные, требуют профессионализма мастера.
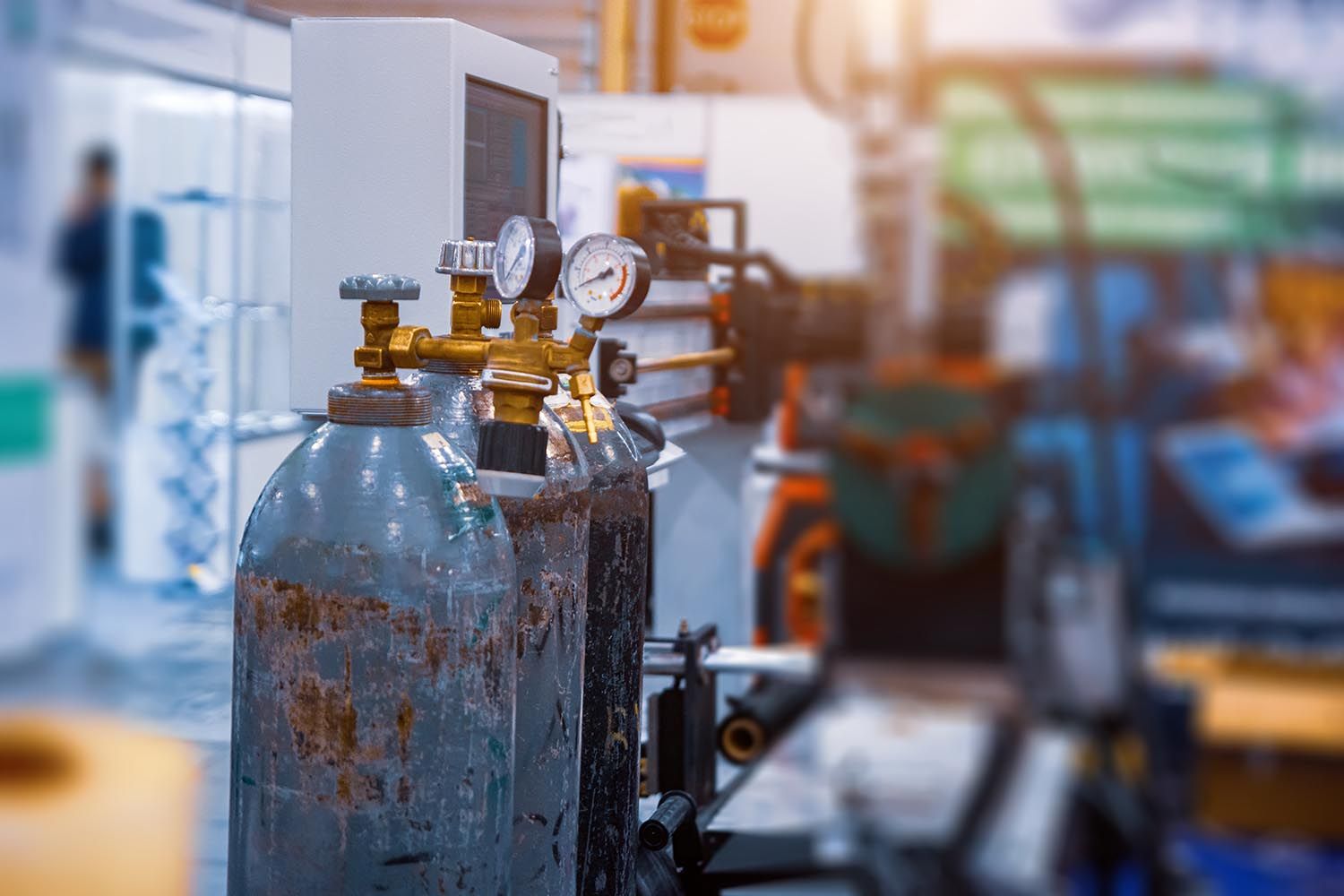
Лучевая
Тепло создаёт луч. Так как он тонкий и точно направленный, технология применяется в радиоэлектронике, где необходимо скреплять детали маленьких размеров. Участки, прилегающие к стыкам, лучом не нагреваются, поэтому риски деформаций даже листовых тонких материалов минимальны.
Выделяют два вида лучевой сварки:
- Лазерная. Она довольно популярна, может осуществляться как на сложных автоматизированных установках, так и на мобильных станках, в том числе с ЧПУ. Существует несколько типов лазеров, например, газовые, полупроводниковые, твердотельные, жидкостные.
- Электронно-лучевая. Источником выступает электронный луч – пучок электронов. Работы проводятся в вакуумной специальной камере. Способ довольно редкий, оборудование сложное, дорогостоящее.
Термитная
Сущность метода – использование термита. Это порошковая смесь магния, алюминия и окислов железа. Когда порошок горит, активно вырабатывается тепло, расплавляющее края стыкуемых элементов. Термит также расплавляется и внедряется в материал, кристаллизуя шов, упрочняя его.
Электрошлаковая
Кромки расплавляются при нагревании шлака флюсом, который плавится под действием электротока. Флюсовый порошок засыпается в образованный между соединяемыми деталями проём. Мастер использует проволоку либо присадочный пруток.
Электрошлаковый способ широко применяется в промышленности, подходит для чугуна, сталей, некоторых цветных металлов. Технология применима к толстостенным изделиям и крупногабаритным, например, опорам, валам, турбинам.
Термомеханическая
Эта методика комбинированная, объединяющая термическое воздействие (нагрев) и механическое (прессование, давление, прижимание). В этот класс входят газопрессовая сварка, стыковая контактная, диффузионная. При локальном или общем нагреве деталей разогретые кромки стыкуются и дополнительно сдавливаются для наиболее надёжного соединения. Швы получаются прочными, непрерывными, сплошными.
Контактная сварка
Относится к термомеханической группе, предполагает нагрев металла током, проходящим через зону соприкосновения кромок изделий. Далее детали осаживают или прижимают друг к другу. Такой вариант используют в машиностроении, он допускает автоматизацию операций, а оборудование можно внедрять в производственные роботизированные линии.
Диффузионная сварка
Ещё один подвид термомеханической технологии, предполагающий взаимное проникновение металлов при значительном сжатии заготовок (такое проникновение называется диффузией). Нагрев увеличивает скорость обмена материалов частицами. Для работ необходима среда из инертного газа или вакуумная камера. Кромки под током нагреваются до состояния, близкого к плавлению. Изделия на время фиксируются в стабильном положении, при этом подача электричества не прекращается. Усилие сжатия – не менее 20 МПа.
Кузнечная сварка
Выполняется нагревание изделий в горне. Далее нагретые заготовки размещаются одна на другой и путём сильных ударов молотом фиксируются в зоне стыковки. Поверхности для надёжных соединений должны быть чистыми. Метод не самый распространенный, подходит для пластичных металлов. Он требует мастерства, квалификации кузнеца.
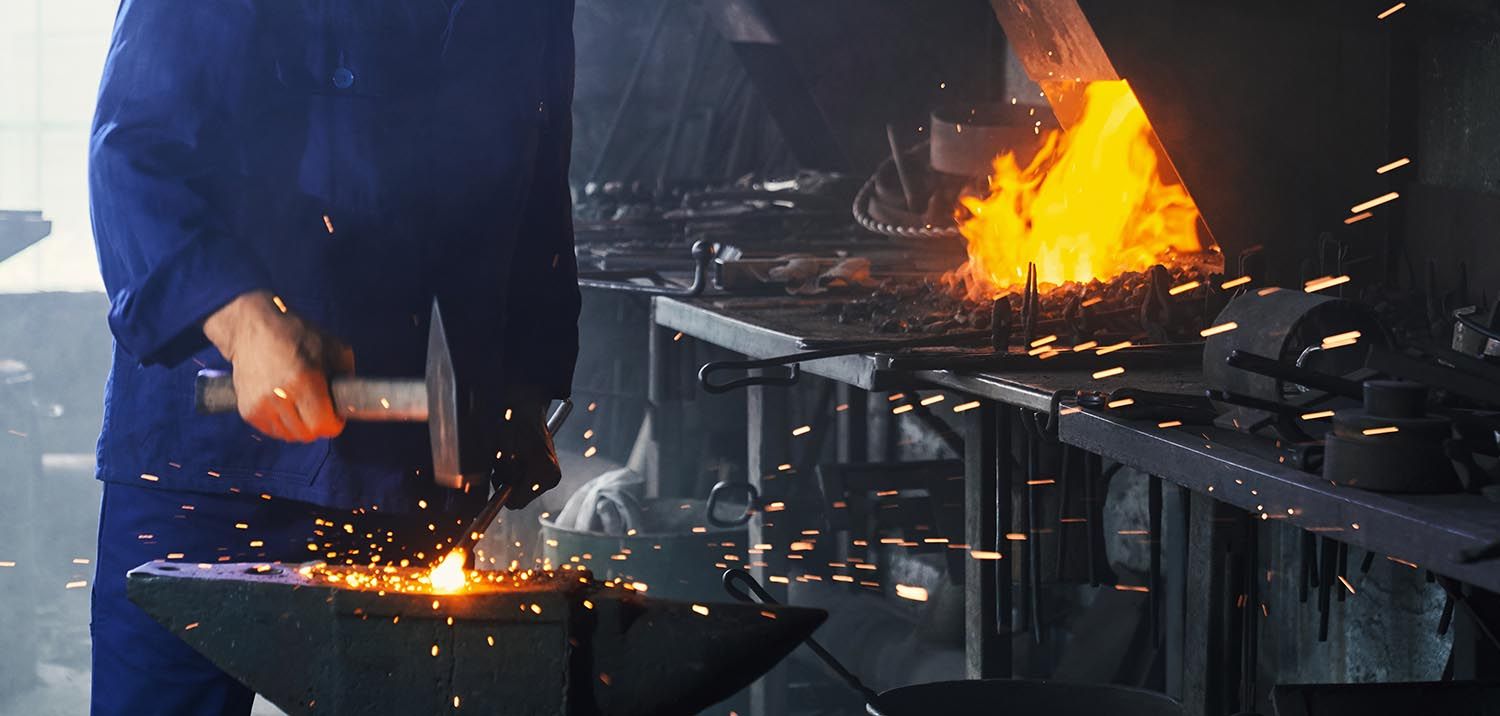
Механическая
Это группа методов, для реализации которых используется диффузия (взаимное проникновение) или энергия, возникающая при механических воздействиях. Ниже рассмотрим отдельные виды.
Сварка трением
Перспективная разработка. Сущность заключается в фиксации одной из заготовок в неподвижном положении, прижатии и активном вращении второй заготовки. Есть несколько возможных вариантов:
- Перемешивание. В специальном оборудовании предусмотрен рабочий инструмент вращения с основанием, называемым буртом, и наконечником – пином. Детали соединяются выдавливанием с дальнейшим перемешиванием.
- Линейная сварка. Вращения нет. Соединяемые элементы трутся до момента плавления стыкуемых поверхностей. После этого увеличивают силу сдавливания.
- Радиальный способ. Между соединяемыми торцами труб размещают вращающееся кольцо.
- Штифтовая методика. Она эффективно убирает незначительные сквозные повреждения. В зоне дефекта просверливается отверстие округлой формы, в котором размещается крутящийся штифт, изготовленный из того же материала, что и ремонтируемое изделие.
- Инерционная сварка. Движение заготовок запускается энергией, которая предварительно создалась и аккумулировалась в раскрученном маховике.
Сварка взрывом
Для этой технологии используются взрывчатые смеси, которые соединяют пластины без плавления, с максимальным сохранением исходных свойств. Сварка взрывом подходит для плохо сочетающихся материалов, имеющих разные температуры плавления и другие свойства. Возможно применение в судостроении, авиационной отрасли, автомобилестроении. Взрывчатый материал помещается между пластинчатыми заготовками, поджигается. Взрыв создаёт ударную волну, которая сталкивает, буквально склеивает пластины.
Ультразвуковая
Операции проводятся с помощью оборудования, преобразующего волны ультразвука в высокочастотные колебания, которые дополняются давлением. Сначала металл очищается от оксидной плёнки сухим трением. Далее за счёт колебаний материал получает энергию и нагревается, а одновременное сдавливание обеспечивает надёжные соединения.
Холодная
Заготовки с усилием, равным от 1 до 3 ГПа сжимаются друг с другом. Для точечной холодной сварки применяют стержни, а для шовной – ролики. Работы могут выполняться только со сжатием или с дополнительным сдвиганием заготовок после их прессования.
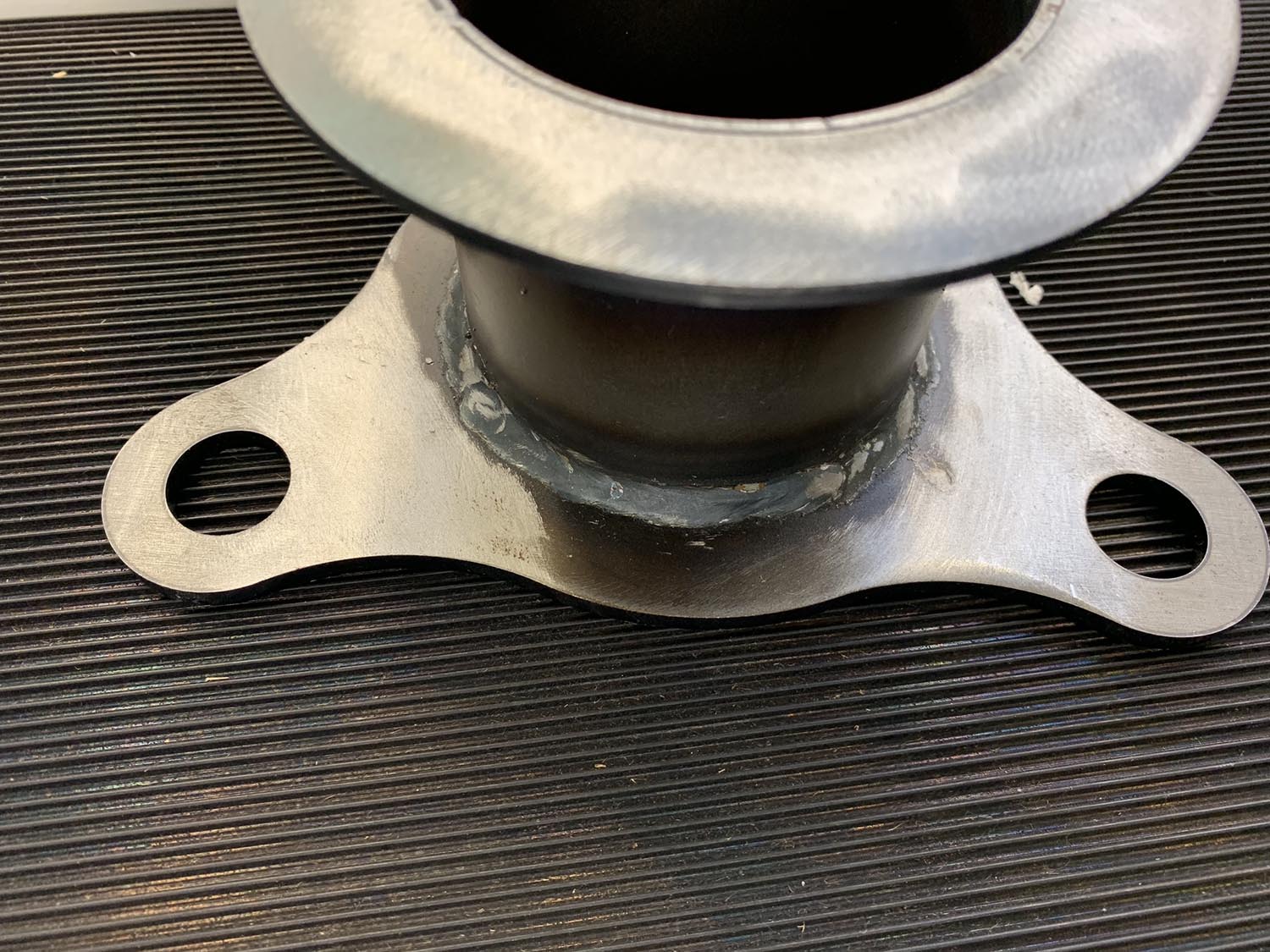
Плазменная
Энергия – плазма, которая создаётся оборудованием, включающим плазмотрон, источник постоянного тока и заполненный аргоном баллон. Также может предусматриваться система охлаждения.
Подаваемый в плазмотрон газ доводится до высокой температуры электрической дугой, расширяется в 100 раз. В таком состоянии газовое вещество становится жидки, выходит из сопла, подаётся в зону соединения. Температура при этом достигает 30 тысяч градусов Цельсия. Плазма также подходит для резания.
Особенности сварки для разных металлов
Выбор технологии, режима, расходников и оборудования зависит от того, какойматериал обрабатывается. Рассмотрим основные нюансы:
- Для углеродистых сталей высоки риски растрескивания из-за закалки шва. Такую проблему можно решить предварительным нагреванием до +100-+300℃, использованием покрытых электродов, созданием многослойных швов, а также отпуском до 300 градусов после завершения сварки.
- У ферритовых сталей при охлаждении могут выпадать зёрна карбидов хрома, снижающие прочность и вызывающие коррозию. Для предупреждения таких последствий можно использовать ток малой силы и увеличить скорость охлаждения.
- Медь лучше сваривать газовым способом, так как она содержит свинец, водород и кислород, вызывающие сложности при других технологиях.
- Чугунные заготовки сваривают с электродами из этого же материала диаметром от 8 мм до 25. Детали предварительно нагреваются.
- Оксидная плёнка, которая может образовываться на алюминии, убирается флюсами.
От выбора вида сварки и соблюдения её технологии зависят качество швов и надёжность конструкции. Компания Profbau выполняет сварочные работы любой сложности. Мы используем разные способы, применяем современные технологии, автоматизированное оборудование. Это, а также квалификация наших мастеров позволяет добиваться отличных результатов, высокой точности, соответствия стандартам и требованиям. Выполняем заказы любой сложности. Уточнить подробности можно по электронной почте, по телефону или заявкой на сайте.