Раскрой металла – это важная технологическая операция, один из первых этапов производства заготовок для последующего получения конечных изделий. От того, насколько грамотно специалист раскраивает материал, зависят стоимость и качество продукции. Узнайте, как проводят раскрой деталей, какими способами его осуществляют, какие расчёты выполняют.
Что это такое
Раскройка металла представляет собой формирование заготовок из исходных полуфабрикатов. Процесс начинается с нанесения контуров на металлопрокат, например, профильный, сортовой, листовой, фасонный, трубный.
Большой лист или другое изделие разделяется на более мелкие части – заготовки, которые должны иметь определённые геометрические формы, размеры. Обычно такой процесс идёт за первичным производством – литьём, прокатом. Он позволяет снижать себестоимость конечной продукции и добиваться её высокого качества, соответствия чертежам, действующим стандартам, предъявляемым требованиям.
Для чего это нужно
Главная цель – изготовление деталей требуемого качества, оптимальной стоимости и с рациональным расходованием материала, то есть с минимальными объёмами отходов. Последние могут полностью отсутствовать, если изделия имеют геометрически правильные формы. Но обычно контуры сложные, криволинейные. И площадь металлического полуфабриката должна быть заполнена максимально.
При предварительной разметке, осуществляемой по технологической карте, чертежам и прочим документам, учитываются требуемые габариты и конфигурация. Это помогает создавать точные контуры для дальнейшей металлообработки, например, резания или воздействия лазера. Так получаются изделия необходимого качества, соответствующие нормативам.
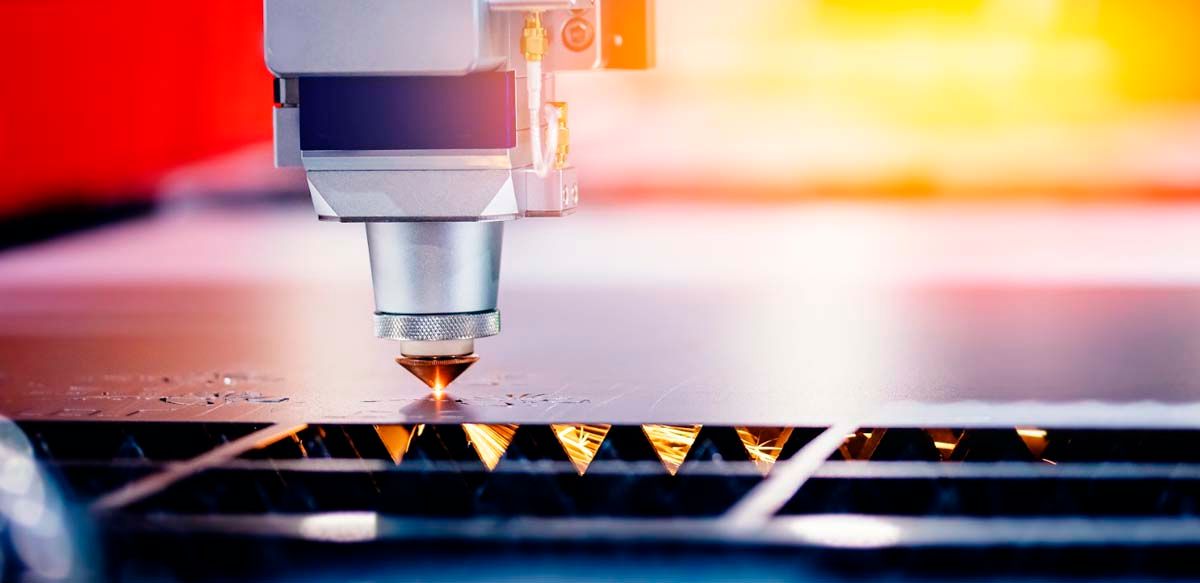
От раскроя зависит себестоимость, на которую влияют объёмы отходов, затраты на первичную обработку (разделение проката на фрагменты), а также трудоёмкость и скорость производства.
Технология
Раскройка является заготовительным производственным этапом, с которого стартует создание конечных изделий или многокомпонентных конструкций. Эта стадия определяет дальнейшие предстоящие работы. От того, как детали обозначены и распределены на полуфабрикате, зависит то, сколько сырья будет израсходовано, сколько его останется.
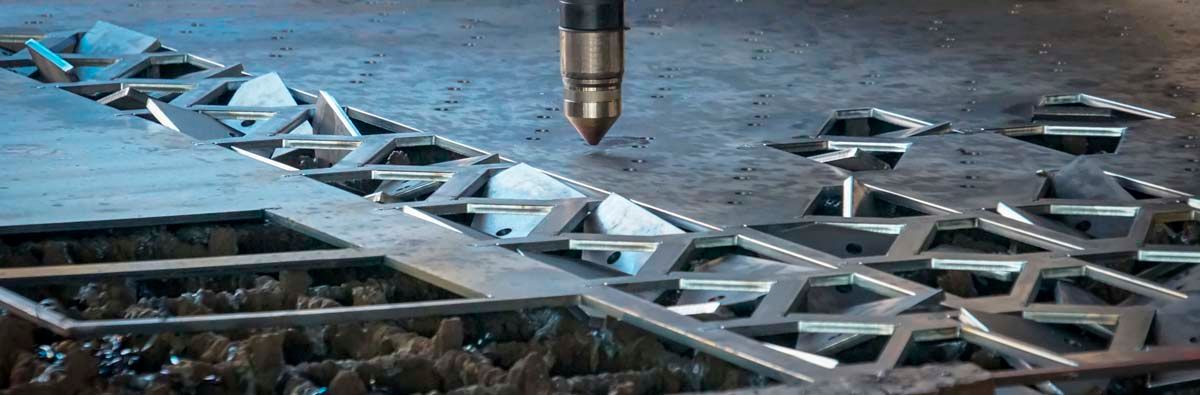
Важная операция – разметка. Это основа карты раскройки, в которую входят схемы расположения будущих заготовок на поверхности проката. При мелкосерийном производстве или создании единичных образцов карты составляются вручную. Но при потоковом изготовлении это проблематично, менее точно и более трудоёмко, поэтому в данном случае применяют специализированные программы. Для раскроя используются станки: ими оснащаются практически все цеха, заводы, металлообрабатывающие предприятия.
Отходы бывают безвозвратными и возвратными. Первые к дальнейшей переработке непригодны, поэтому они утилизируются. А вторые можно использовать повторно, например, расплавлять для отливки.
Технология включает два основных этапа. Первый – разметка, то есть перенос очертаний будущих изделий. За основу берётся чертёж, который дублируется на полуфабрикате с необходимым масштабом, со строгим соблюдением размерности, геометрии.
Второй этап – непосредственно создание отдельных фрагментов. Для этого применяют силовые, то есть механические или иные методы, позволяющие разделять металл на части. Источником энергии может быть лазер, плазма, смесь кислорода с газом.
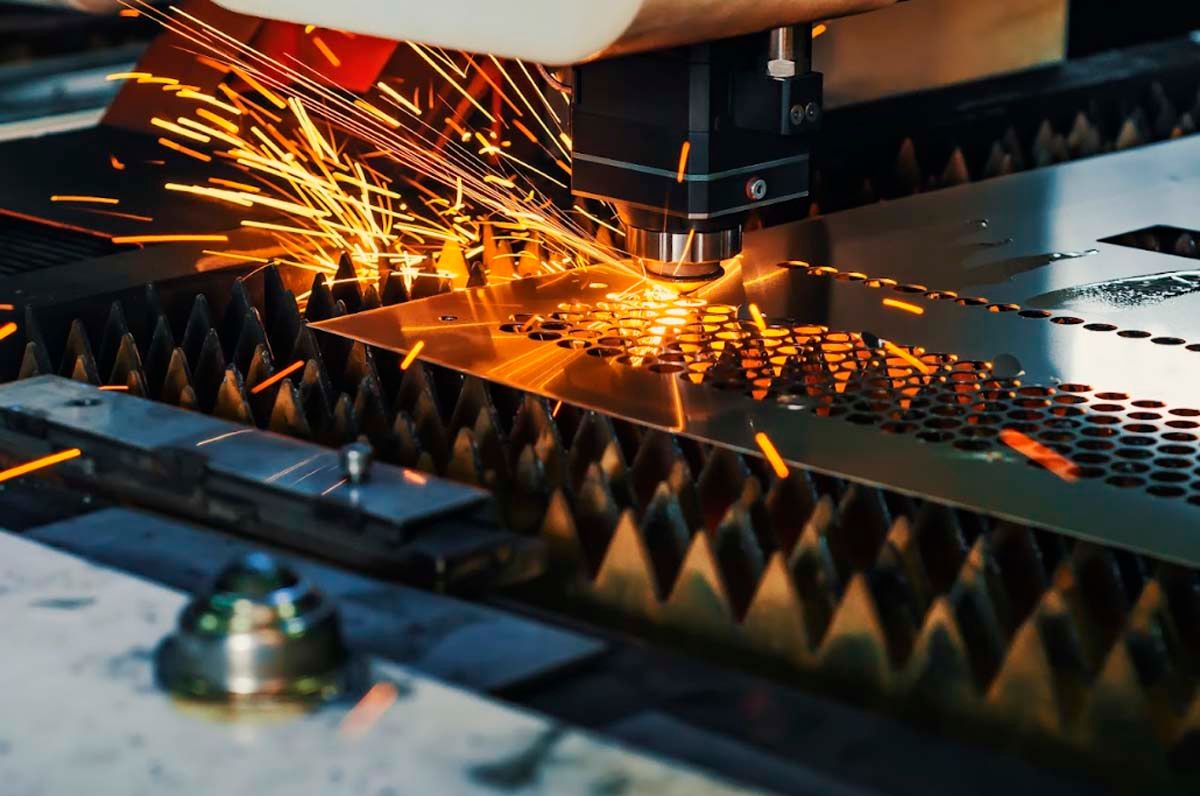
При раскройке обязательно учитываются:
- Качество кромок. Это отсутствие натяжения (внутреннего или поверхностного), ровность реза, минимизация объёмов отходов.
- Расчёт образующихся отходов. Чтобы понять, сколько их будет, берут во внимание технологические неизбежные потери (частичное испарение материала при интенсивном нагревании, его оплавления, возникающая при резании стружка), а также формы заготовок и свободные пространства, которые остаются между ними.
- Скорость операции. На неё влияет используемый метод.
- Карта раскроя. Она определяет способ, скорость, точность, количество отходов.
- Предъявляемые требования. Они описываются в нормативной документации, в государственных российских стандартах (ГОСТ) или международных (ISO). Одно из требований – допускаемые погрешности размеров.
Способы раскроя
Есть различные способы раскройки. Они по типу воздействия делятся на две большие группы: механические и термические. Первая предполагает разделение металла механически, то есть с помощью оборудования с рабочими инструментами, по прочности превосходящими обрабатываемый металл. Термические методы – это влияние тепловой энергии, которая может создаваться, например, лазером, потоком плазмы, струёй смеси сжатых газов.
Все способы различаются по скорости проведения операций, качеству кромок, отклонениям размеров, объёмам отходов, затратам. Любой метод имеет достоинства и недостатки. При выборе учитывается несколько факторов:
- формы создаваемых изделий и их размеры;
- вид проката: листы, трубы, балки, швеллеры, уголки, полосы или что-то другое;
- толщина материала;
- состав металла или сплава, его физические и химические свойства, такие как пластичность, твёрдость, температура плавления;
- необходимая скорость операций.
Раскраивать металл можно как одним из имеющихся способов, так и несколькими. При комбинированной обработке обычно сначала первичные контуры формируются механически (резкой), а доводка до конечных габаритов и геометрии, а также обработка кромок и устранение дефектов осуществляются с термическим воздействием. Ниже рассмотрим все виды раскройки подробно.
Механические
Такие способы актуальны при простых формах заготовок, например, круглых, прямоугольных, треугольных, квадратных. Механический раскрой имеет несколько плюсов:
- небольшие затраты: оборудование обычно относительно простое, недорогое, не требующее сложного обслуживания;
- возможность раскроя под разными углами, например, строго перпендикулярно заготовке или под наклоном с определённым углом;
- высокая эффективность при работах с изделиями простых геометрических форм;
- высокая скорость;
- использование технологии не только на профильных предприятиях, но и в бытовых условиях: есть мобильные и компактные станки, которые можно устанавливать дома или в гараже и применять для самостоятельной резки.
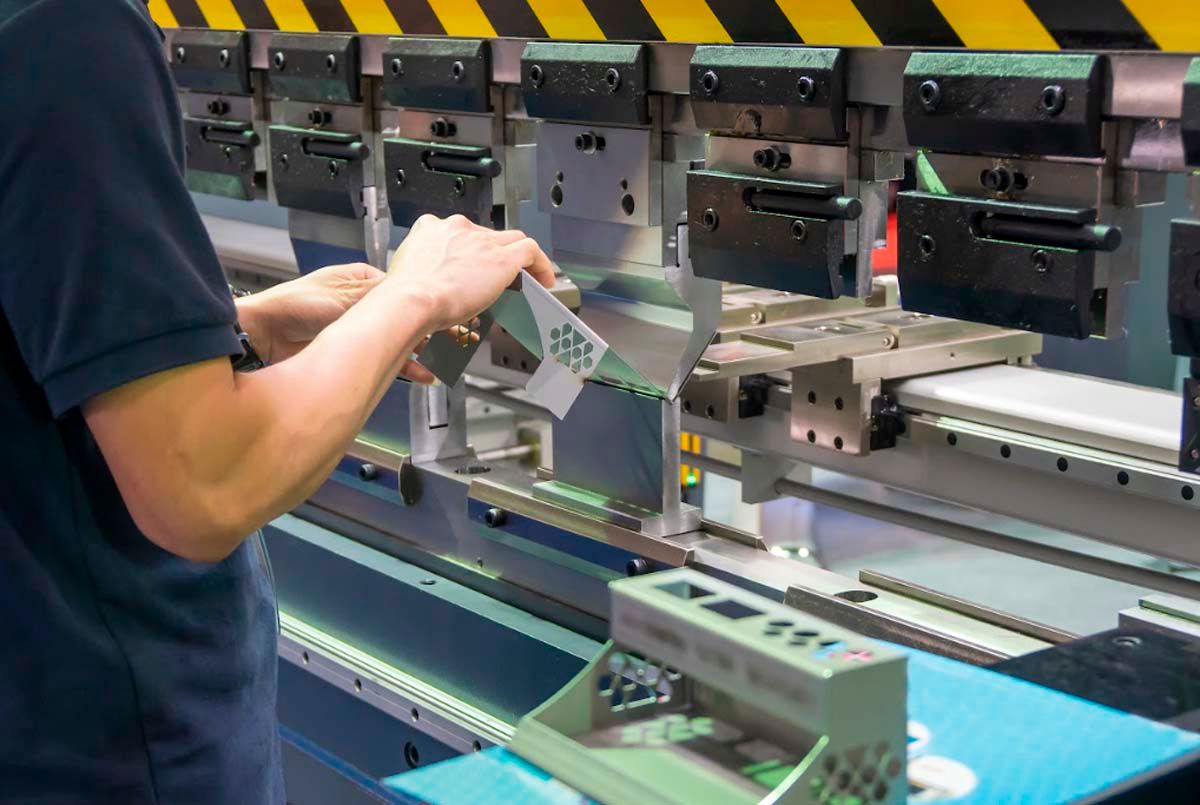
К механическим относится несколько методик, которые рассматриваются отдельно ниже.
Гильотина
По конструкции гильотина – это устройство с рабочим столом и подвижным ножом, который перемещается строго в одной плоскости, при этом угол его наклона менять невозможно. Листовой или полосовой полуфабрикат надёжно закрепляется на основании. На него резким движением с ускорением опускается рабочий инструмент. Он разрезает первичную заготовку поперёк или вдоль, по прямой линии.
Гильотина, которую также называют гильотинными ножницами, может быть:
- Механической (ручной). Она оснащается длинным рычагом, приводимым в действие физическим усилием. Воздействие передаётся с помощью передаточного механизма. Вручную возможно резать относительно мягкие металлы и сплавы небольшой толщины – от 0,45 мм до 2,5.
- Пневматической. Ножницы приводятся в действие компрессором, создающим значительное давление сжатого воздуха или газа.
- Гидравлической. В таком станке функцию силового агрегата выполняет гидросистема, рабочая среда которой – вода или иная жидкость.
- Электрической. Привод в такой гильотине – электродвигатель. Мотор должен обладать достаточной мощностью. А чтобы повысить усилие реза, в конструкцию внедряют редуктор.
Пневматические, электрические и гидравлические гильотинные ножницы способны развивать значительное усилие, позволяющее быстро и эффективно разрезать материалы толщиной до 20 мм.
Преимущества: отличная скорость, отсутствие термического воздействия, высокое качество при получении заготовок простой геометрии, небольшая стоимость работ, незначительные потери (стружки при разрезании нет), чистые резы, ровные кромки. Недостатки: невозможность создания криволинейных контуров, ограничения по толщине, вероятность погрешностей.
Гильотинную резку применяют в строительстве, прочих отраслях промышленности для раскройки полосового и листового проката из некоторых марок сталей, из цветных металлов (алюминия, меди) и их сплавов. Метод используется при изготовлении сливов, металлочерепицы, профлистов, откосов, разных доборных элементов.
Пилы
Распил осуществляется с помощью ленточных пил и дисковых. В первых рабочий пильный инструмент имеет вид замкнутой ленты, снабжённой многочисленными острыми зубьями, располагающимися на одном краю. Ленточный элемент фиксируется на двух шкивах, которые вращаются благодаря усилию электрического мотора. Рабочий орган дисковой пилы – это имеющий режущие зубцы диск. Он также приводится в действие двигателем: быстро крутится, погружается в металл и разрезает его.
Пилы бывают мобильными и стационарными. Пример первого вида – это обычная «болгарка», то есть углошлифовальная машинка. К ручным электроинструментам относят циркулярные пилы, лобзики. Стационарные пильные станки более точны и производительны, поэтому их используют на производствах. В быту можно применять и ручные инструменты.
При распиливании заготовка фиксируется на станине. Лента или пила осуществляет прямолинейный рез. Таким способом можно раскраивать стальные и другие металлические полуфабрикаты толщиной не больше 8 миллиметров.
Резать пилами можно под разными углами, скорость обработки довольно высокая, оборудование недорогое и зачастую не очень большое. Но получать криволинейные контуры невозможно, как и автоматизировать процесс разрезания. Из-за вероятности значительных отклонений технология часто становится вспомогательной, внедряемой на первых этапах производств и требующей доработки более точными способами.
Просечной пресс
Такие прессы, которые также называют пробивочными, подходят для формирования в листах отверстий, выемок. К раскройке этот способ можно отнести косвенно. Размеры создаваемых деталей из-за особенностей конструкции станков небольшие, а их формы обычно ограничиваются простыми геометрическими, например, квадратными, ромбовидными, круглыми, прямоугольными, треугольными. Обычно просечные прессы используют для перфорации, рифления, штампования, вырубки.
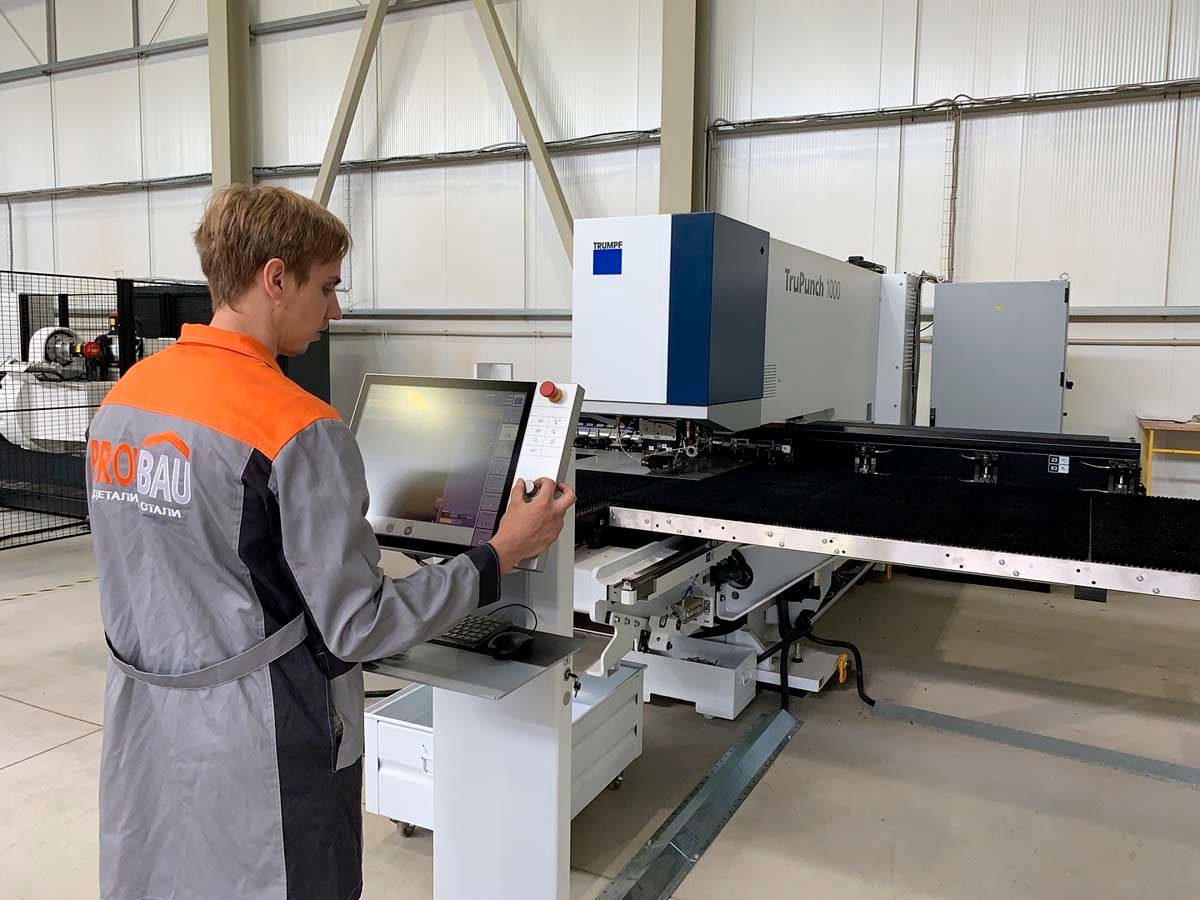
Гидроабразивная резка
Она также относится к механическим технологиям и подразумевает обработку водяной струёй или смесью воды с абразивными частицами. Жидкость или суспензия абразива подаётся с высокими показателями скорости и давления, что позволяет прорезать сплавы и металлы толщиной до 20 см. Можно обрабатывать как пластичные материалы, так и твёрдые. Гидроабразивной резкой мы выполняем операции со стальными, алюминиевыми, железными, медными, латунными, титановыми и другими полуфабрикатами.
Лазерная резка
Современная лазерная резка, которую предлагает наша компания, основана на непрерывном или импульсном воздействии луча сфокусированного мощного лазера, который локально и интенсивно нагревает металл до температур, превышающих значения плавления. В результате в зоне реза целостность нарушается, происходит разрезание. Образующуюся окалину для предотвращения неровностей кромок удаляют, например, вспомогательными газами.
Лазерные установки бывают газовыми, волоконными и твердотельными. Часто применяют CO2-лазеры (газовые) и типа YAG, то есть твердотельные. Их мощность варьируется от 50 ватт до 30 киловатт. Максимально возможная толщина материалов достигает 8 сантиметров. Но многие стандартные устройства рассчитаны на меньшие значения – не более 1 см. Размеры листов или полос тоже ограничиваются площадью рабочего основания, на котором заготовки закрепляются.
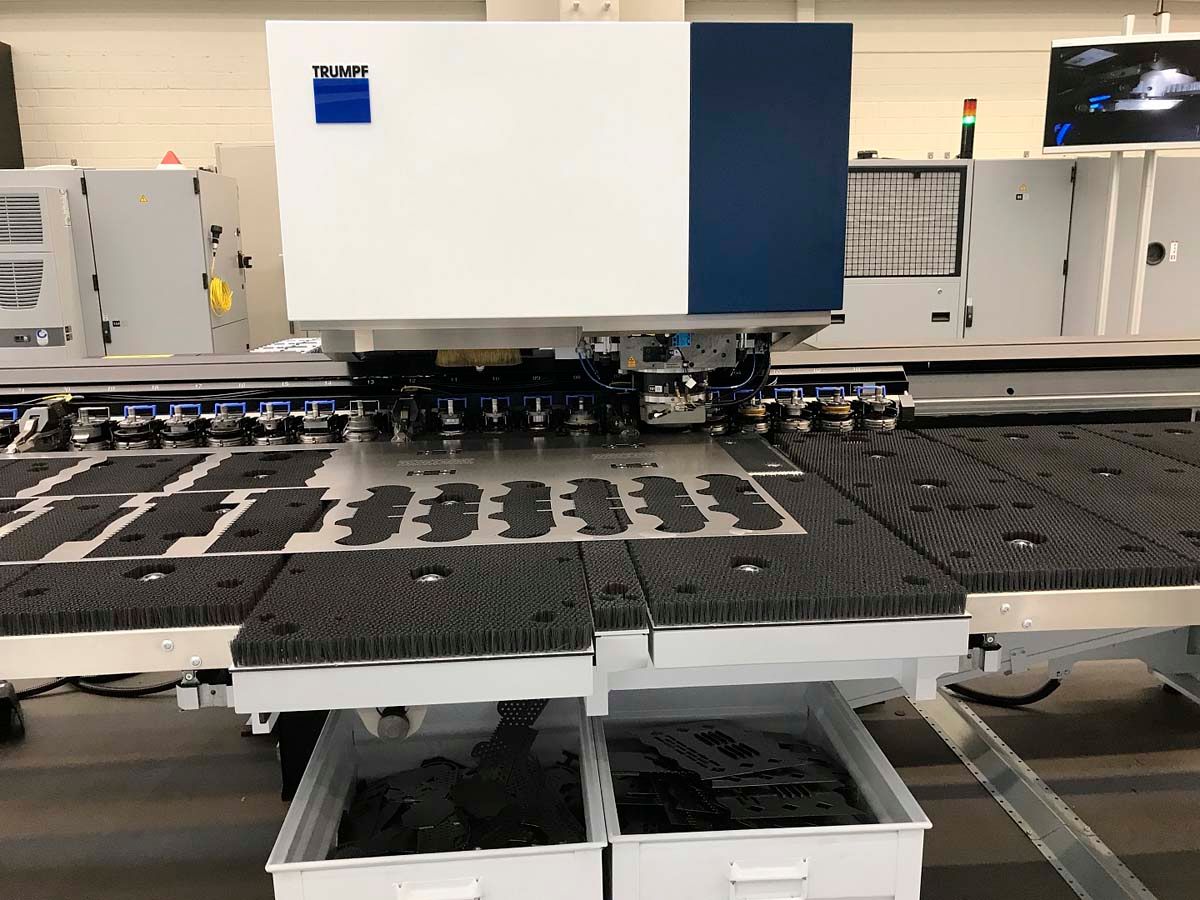
Плюсы:
- обработка различных металлов, включая хрупкие и обладающие высокой теплопроводностью, а также стекла, древесины, пластиков;
- получение сложных фигур с криволинейными очертаниями;
- автоматизированные технологические операции, выполняемые на станках с ЧПУ, роботизированных современных устройствах;
- незначительные технологические потери: толщина реза соответствует диаметру лазерного луча (а он мал), а термическое воздействие локальное, направленное на заданную зону и минимально затрагивающее остальное пространство;
- высокая точность: края без окалин, наплавов и шероховатостей, строго перпендикулярные кромки;
- высокоскоростная резка.
Минусы:
- ограниченная толщина полуфабрикатов – чаще всего до 1 см, в некоторых мощных установках до 8 см;
- дороговизна из-за высокой цены лазерных станков;
- меняющаяся скорость резки, на которую влияют состав, марка, толщина сплава или металла.
Плазменный раскрой
Принцип плазменной резки, выполняемой нашими мастерами, такой: в ограниченном участке возникает пучок плазмы. Он локально испаряет материал. Для достижения такого эффекта необходима располагающаяся между соплом и электродом электрическая дуга, на которую под давлением до 8 атмосфер поступает направленная струя воздуха или иного газа, такого как азот. При этом появляется поток ионизированного газа, то есть плазменный пучок. Он по температуре достигает 15-30 тысяч градусов.
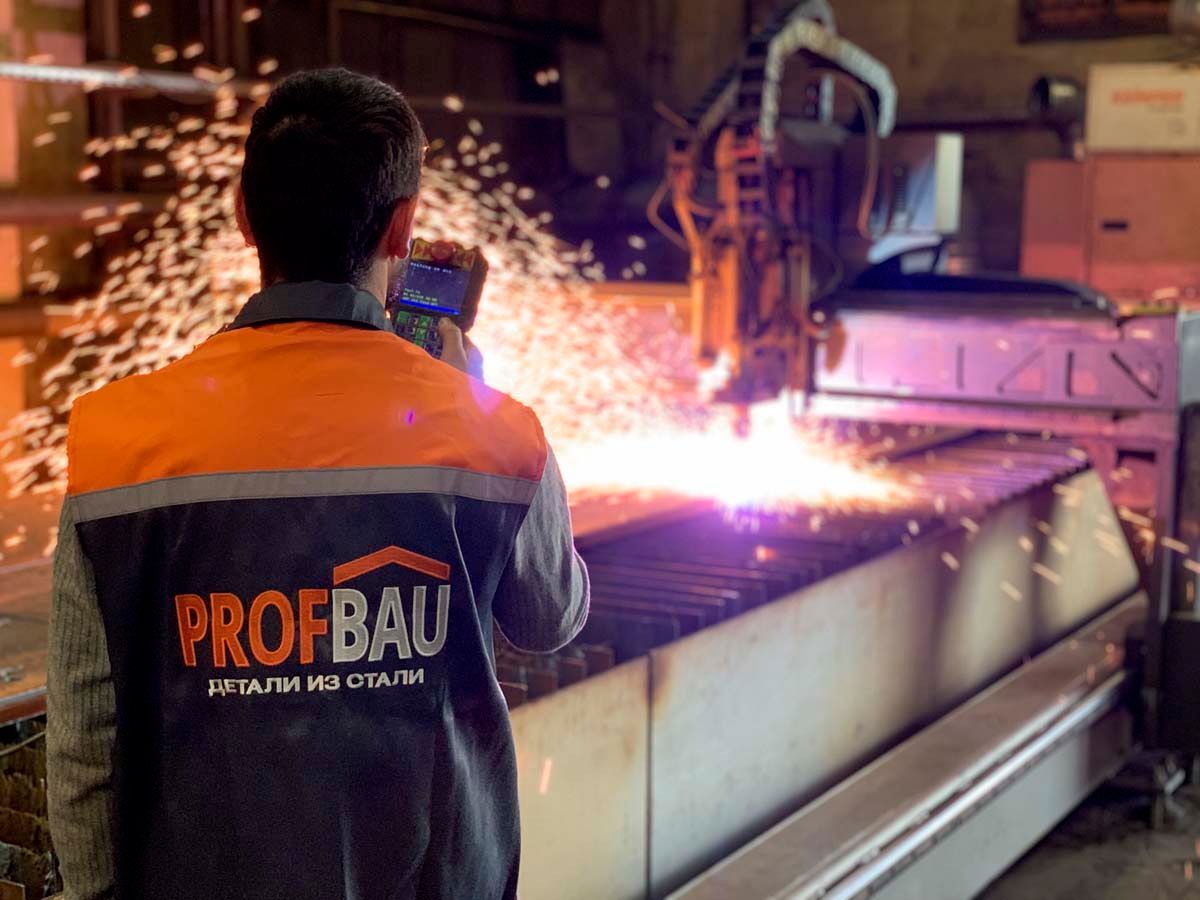
Данная технология подходит для металлов, имеющих толщину до 10-12 сантиметров. Вероятна конусность – меняющаяся ширина реза, сокращающаяся по мере увеличения глубины проникновения. Для цветных металлов и их сплавов этот показатель довольно велик – до 20°, а для чёрных меньше – от 1 до 10 градусов. В итоге геометрия кромки может меняться.
Преимущества:
- производительность;
- отличная скорость выполнения работ;
- небольшая ширина реза;
- совместимость с медью, сталями, алюминием, бронзой, чугуном (при этом полностью перенастраивать оборудование не нужно);
- отсутствующие дефекты: окалина, заусенцы, наплывы, деформации;
- сложная, криволинейная резка, в том числе шаблонная и автоматизированная;
- погрешности реза не больше 0,5 мм.
Недостатки:
- возможные отклонения от перпендикулярной направленности реза;
- необходимость подачи воздушной или газовой смеси, а также фильтрации.
При выпуске прецизионных изделий дуга сжимается, что вызывает увеличение плотности энергии. Такой подход оптимален в механизированных, автоматических комплексах. Но он отличается небольшой скоростью.
Газокислородный способ
Разрезание осуществляется струёй, состоящей из чистого кислорода и газа. Эта смесь подаётся на нужную область под высоким давлением. Материал быстро сгорает. А поток воздуха при этом убирает продукты сгорания и обеспечивает очистку.
Главная сложность заключается в необходимости настройки – подбора оптимальных скорости и интенсивности подачи струи. Если увеличить объём кислорода, то может происходить сильное охлаждение. При недостаточной подаче вероятно неполное окисление. При снижении скорости возможны оплавления краёв, а при её повышении – резание не на всю глубину.
Плюсы:
- резка толстых заготовок – до 500-600 мм;
- возможность исключения конусности при грамотном подборе горючей смеси;
- допустимость применения нескольких рабочих головок одновременно;
- хорошая скорость.
Минусы:
- способ не подходит для тонких листов, тонкостенных заготовок;
- совместимость лишь с некоторыми цветными и чёрными металлами;
- снижение качества при работах с полуфабрикатами тоньше 3-4 мм;
- обязательность соблюдения техники безопасности при использовании активных газов.
Расчет раскроя, минимизация отходов
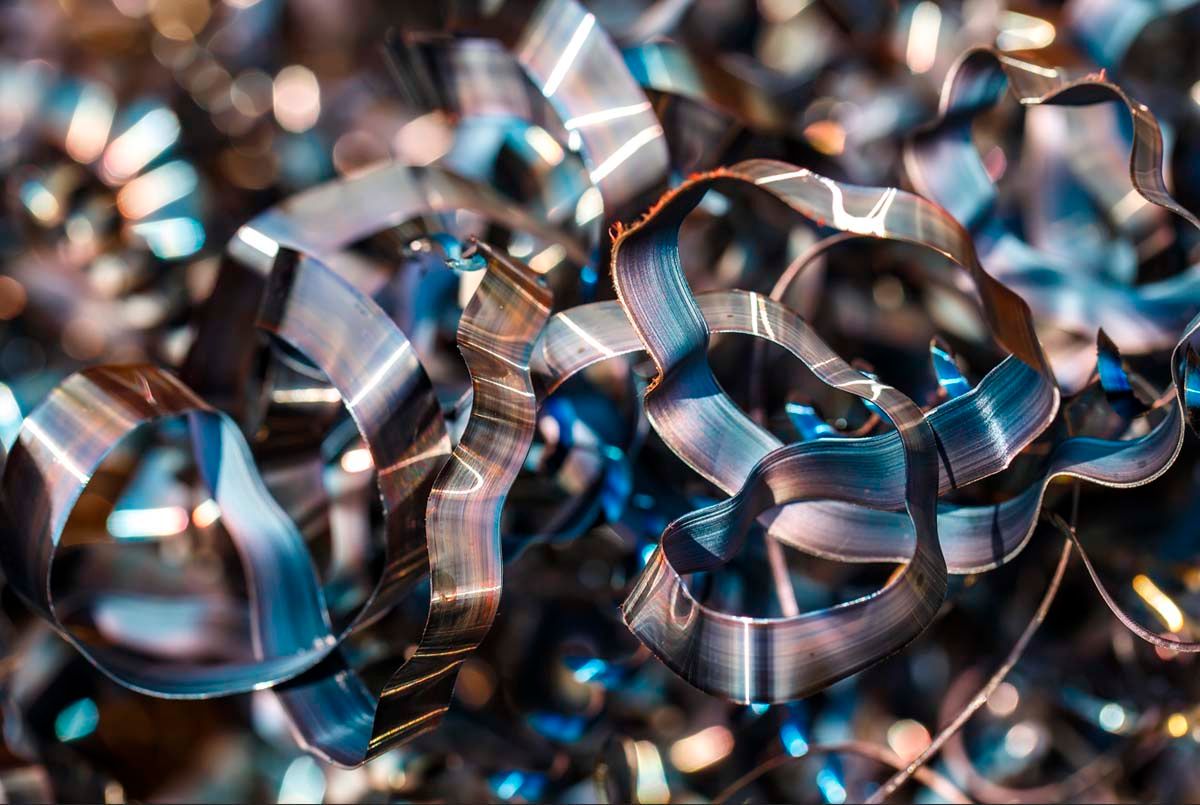
Перед производством подготавливается карта раскроя – схема, по которой на всей площади металлического листа будут располагаться отдельные заготовки. Она создаётся вручную или специальными программными комплексами при потоковом, крупносерийном выпуске.
Основные принципы подготовки карты:
- При однотипных изделиях использование материала экономичное и рациональное.
- Сначала отмечаются размеры самых широких и длинных элементов. Остающееся пространство заполняются остальными, более мелкими деталями.
- Чтобы оптимизировать порезку и сделать менее частыми проходы рабочего инструмента, контуры следует совмещать.
- Важно учитывать технологическую ширину реза. При термообработке с повышенными температурами она равна от 3 до 5 мм от фактического значения. Если раскрой механический, то такой показатель во внимание не берётся.
- Чем полуфабрикат больше, тем выше коэффициент раскроя.
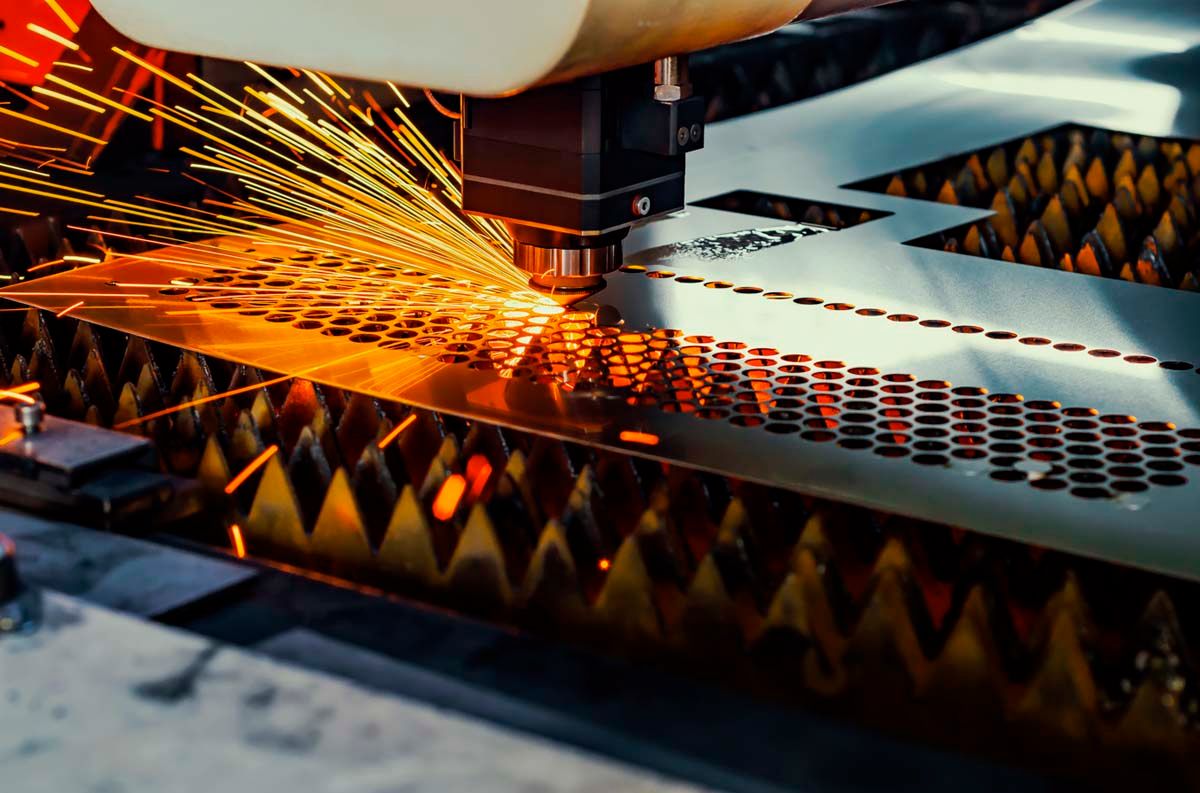
Следует учитывать оборудование и возможность оптимизации, изменения ширины реза – минимальной и максимальной. Нельзя игнорировать требующееся итоговое качество изделий. Так, при высокоточном изготовлении не должно быть конусности срезов.
Нормы раскроя
Нормы расхода для металла определяют количества исходных материалов, необходимые для получения единицы продукции. Они рассчитываются при выпуске любой детали. На норму влияют различные факторы: точность разметки, технология раскройки, размещение фрагментов, толщина, необходимое итоговое количество и геометрия заготовок. И расчётное значение будет среднеарифметическим, отличающимся в большую сторону от фактического и меняющимся под влиянием различных условий.
Коэффициенты
Норма раскроя металла требует учёта соответствующего коэффициента. Он вычисляется делением общей чистой площади всех сформированных изделий на общую площадь материала. В некоторых случаях за основу расчётов берутся чистые объёмы деталей и исходной заготовки или их массы.
При вычислении нормы применяют не только коэффициент раскроя, но и прочие параметры: показатель использования материала, выход продукции. Такие значения позволяют ещё до начала производства оценить и спрогнозировать его эффективность. Плановые цифры всегда сравниваются с фактическими.
Заключение
Компания Profbrau раскраивает различные металлы оперативно, профессионально и недорого. Наши мастера работают на современном оборудовании, грамотно выбирают и соблюдают технологии. Мы достигаем высокого качества продукции, максимальной точности её габаритов и геометрии, а также соответствия требованиям и стандартам. Обращайтесь к нам по телефону, лично в офисе, по электронной почте или в мессенджерах. Также можно оставить заявку на сайте.